Защита зоны сварки и легирование металла шва. Опыт внедрения автоматической сварки
Основной целью автоматической сварки (как и других способов) является обеспечение высокого качества сварного соединения, и в первую очередь — металла шва. Качество зависит от ряда факторов, в том числе от условий защиты зоны сварки от воздействия воздуха. В ряде случаев возникает необходимость легирования металла в сварочной ванне. Поэтому при разработке дуговой автоматической сварки одним из направлений было создание средств надежной защиты зоны сварки без участия человека во время выполнения соединения. Н. Г. Славянов предложил для этих целей применять металлургические молотые флюсы, которые засыпали в зону сварки и наплавки вручную. Вопросы непрерывной подачи флюса им разрабатывались, так как при его способе процесс плавления проходил при неподвижной сварочной головке. Успешное создание электродов для ручной сварки, имеющих высококачественное толстое покрытие, дало возможность механизировать процесс штучными электродами [252]. Были разработаны устройства в виде кассеты, куда закладывался десяток электродов. Так же, как и в ручном электрододержателе, ток подводили от зажимов к верхней оголенной части стержня. Электроды по очереди выдвигались из кассеты и подавались по мере оплавления. Сварочные автоматы, основанные на такой схеме сварки, были громоздкими и ненадежными, швы получались с перерывами [253]. Самым большим достижением в области сварки штучными электродами можно считать сварку наклонным электродом диаметром 14 мм на токе до 750 А. Эта технология «полуавтоматической» сварки была разработана в 1939 г. на «Уралвагонзаводе» (Нижний Тагил) Н. А. Силиным (а. с. СССР № 60938). Автоматы для сварки штучными электродами развития не получили, однако идея защиты зоны сварки веществами, размещенными на самом электроде (снаружи или внутри металлического трубчатого электрода), привлекла внимание ряда изобретателей. Среди проблем, возникших при разработке способа сварки покрытыми электродами, наиболее трудной была проблема подвода тока к электродам. Металлический стержень (проволока) должен быть покрыт таким образом, чтобы хотя бы часть поверхности оставалась свободной от обмазки. Преимущества автоматической сварки теоретически могут быть реализованы при условии, что плавящийся электрод будет неограниченной длины, а напряжение сварочного тока достаточно высоким. Электродная проволока, подаваемая с катушки, обеспечивает непрерывность процесса сварки, благодаря чему исключаются потери времени на замену огарка на новый штучный электрод, появление дефектов, вызванных перерывами, и другие недостатки сварки штучными электродами. Фирма «Дженерал электрик» в 1923—1925 гг. оказалась впереди всех на пути автоматизации дуговой сварки, начав применять гибкую электродную проволоку практически неограниченной длины, на поверхности которой путем накатки или наплавки выполняли металлические выступы, между которыми обычными способами наносили флюсовое покрытие (рис. 94, а). 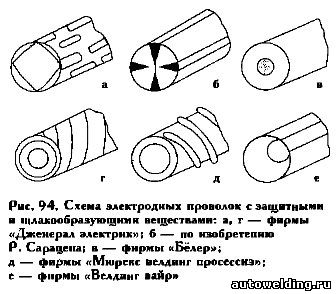
В конце 1920-х гг. многие фирмы США, Франции, Австрии и других стран применяли для автоматической сварки проволоку, конструкция которой была предложена Р. Сараценом (Франция). Идея заключалась в том, что обмазку помещали в нескольких канавках, выдавливаемых в процессе протяжки параллельно оси проволоки (рис. 94, б).Фирма «Бёлер» (Германия) разработала конструкцию и технологию изготовления электродной проволоки с защитными и шлакообразующими веществами, помещаемыми внутри в виде фитиля, занимающего около 5% сечения и проходящего по всей длине (рис. 94, в). Чтобы изготовить такую проволоку, перед отливкой заготовки в центре изложницы устанавливали толстостенную трубу с набитой в нее шихтой. Жидкая сталь заполняла пространство вокруг трубы, однако труба полностью не расплавлялась. Полученную болванку прокатывали и протягивали в проволоку до требуемого диаметра. Проволока с внутренней шихтой была надежна в эксплуатации, однако металлургические ее возможности были ограничены тем, что помещаемая в трубу шихта должна выдерживать температуру расплавления стали, не разлагаясь и не плавясь, и, следовательно, в ее состав нельзя было ввести многие органические и некоторые минеральные вещества.Эту проблему в 1920 г. решила фирма «Дженерал электрик». В соответствии с ее технологией электродная проволока, сматывавшаяся с катушки, обертывалась тонкой стальной лентой, а в это время в пространство между стержнем и полученной таким способом оболочкой подавалась шихта (рис. 94, г) [254]. Фирма «Элин» уделила большое внимание и сварке голой проволокой, на которую перед подачей в зону сварки накладывался спрессованный в виде полуцилиндров флюс. В американских аппаратах «Торнадо» электродная проволока перед ее подачей оборачивалась полоской бумаги. Сгорающая целлюлоза обеспечивала защиту зоны сварки. В 1934 г. Э. Д. Кларком (фирма «Мюрекс велдинг просессиз») была предложена электродная проволока (рис. 94, л), представляющая собой центральный металлический стержень, покрытый флюсом. На поверхность покрытия наматывались тонкая проволока диаметром 0,5 мм, через которую и осуществлялся токоподвод. Преследуя ту же цель — обеспечить токоподвод к покрытой электродной проволоке — Питере и Гудвин (фирма «Виндзор ворк», Великобритания) в 1939 г. предложили наматывать с определенным шагом тонкую проволочную спираль прямо на металлическую проволоку, а покрытие наносить такой толщины, чтобы оно не выступало за края спирали. В Институте электросварки в 1935 г. было найдено конструктивное решение обеспечения большой площади электрического контакта и достаточного количества обмазки. Был создан специальный аппарат для превращения проволоки круглого сечения в проволоку крестообразного сечения (рис. 95), дополняемую шихтой обмазки. 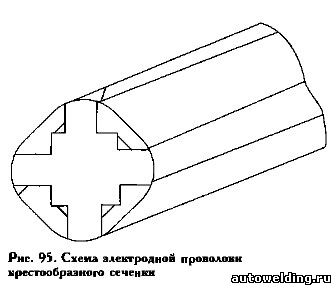
Однако, несмотря на многочисленные конструктивные решения, практика применения проволок с защитными покрытиями и специальными электропроводными элементами показала, что этот принцип обеспечения защиты при автоматической сварке имеет ряд недостатков. Наиболее существенным из них была невозможность подвести к электроду ток большой силы и повысить производительность процесса. В середине 1930-х гг. скорость сварки автоматами не намного превышала скорость ручной сварки штучными электродами. К идее Н. Г. Славянова о защите зоны сварки флюсом, который насыпается отдельно от электрода, обратились в начале 1920-х гг. Д. А. Дульчевский (Одесские железнодорожные мастерские) при сварке и наплавке медных изделий использовал для этой цели порошкообразные горючие вещества: древесный уголь, опилки, сажу, крахмал и т. п. [255]. Причем эти вещества, сгорая, не только оттесняли воздух, но и создавали восстановительную среду в ванне. В 1925 г. Г. Э. Кеннеди (фирма «Линде эйр продактс», США, входившая в корпорацию «Юнион карбайд энд карбон»), занимаясь проблемой приварки деталей к сосудам из эмалированного чугуна, предложил осуществлять легирование ванны элементами, переходящими в ванну из специальных флюсов. В то время идея не была применена на практике. Это объясняется тем, что работа была ориентирована на сварку чугунных изделий, которые обычно не имеют протяженных швов, а флюс предлагалось применять как средство легирования и науглероживания. Идею Кеннеди продолжали разрабатывать Б. С. Робинов, С. И. Пайн и У. И. Квиллен (фирма «Вестерн пайп энд стил», США), предложившие применять для дуговой сварки голой проволокой засыпку керамического флюса (пат. США№ 1782316). В 1935 г. фирма «Линде» доработала технологию, создав способ высокопроизводительной и высококачественной сварки под гранулированным флюсом из минеральных веществ. Изобретение было сделано Л. Т. Джонсом, Г. Э. Кеннеди и М. А. Роттермундом и запатентовано под названием «Юнионмелт» (пат. США № 2043960) (рис. 96). 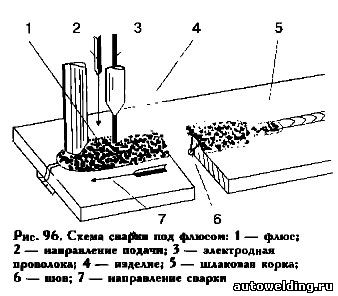
Следует отметить, что изобретатели способа «Юнионмелт» были убеждены в отсутствии дугового разряда под слоем расплавленного флюса. Плавление флюса, электродного и свариваемого металла приписывалось «джоулеву теплу», выделяющемуся при прохождении через расплав. В Германии, где процесс сварки под флюсом получил название «Эллира», допускали наличие дугового разряда, однако считали, что основная доля теплоты выделяется в расплавленном флюсе [256]. Конец спору был положен экспериментальными исследованиями Б. Е. Патона и А. М. Макары. В 1943—1944 гг. они доказали, что источником теплоты в этом способе сварки является дуга. В монографии исследователей впервые изложены основы теории автоматов для дуговой сварки [257]. В процессе совершенствования сварки под флюсом были предложены различные технические решения, некоторые из них представляют интерес. Так, для соединения деталей больших толщин фирма «Катерпиллер трактор» (США) в 1940 г. внедрила технологию, названную «Хотвайер», в соответствии с которой для увеличения коэффициента наплавки вылет электрода искусственно увеличивали, и на этом участке электрод дополнительно нагревался проходящим сварочным током. В 1938 г. фирмой «Томсон-Хьюстон» (США) был запатентован способ сварки с «видимой дугой», при котором сварочный флюс постоянно подавался шнеком через сопло к электродной проволоке (рис. 97, а). Кроме того, предусматривалась дополнительная защита зоны сварки газом, подаваемым через то же сопло. Несколькими фирмами («Браун Бровери», «Баден» и др.) был предложен способ с использованием магнитного флюса с притяжением его к проволоке магнитным полем проходящего сварочного тока и полем, создаваемым постоянными магнитами. Здесь флюс был подобен плотному электродному покрытию (рис. 97, б). 
Следует отметить, что в середине 1920-х гг. были предприняты попытки механизировать процесс газоэлектрической сварки, созданной П. П. Александровым и И. Ленгмюром в фирме «Дженерал электрик» (США). Подвести струю водорода, аммиака или горючего газа к автомату, который обеспечивает перемещение головки с неплавящимися электродами, не представляло трудностей. Необходимость создания оборудования и технологии дуговой сварки в защитных газах была вызвана расширяющимся объемом изготовления конструкций из алюминиевых и магниевых сплавов, а также из специальных сталей. Используя для данного материала инертные газы (аргон, гелий, азот, хлор и др.) вместо электродных покрытий или флюсов из химических активных компонентов, легче было решить металлургические проблемы. В конце 1930-х гг. в США были разработаны и начали применяться автоматы для сварки в защитных газах [179]. Развитие оборудования, материалов и технологии дуговой автоматической сварки шло с некоторым отставанием от совершенствования ручной сварки. В 1920—1930-х гг. объемы промышленного использования автоматической сварки были незначительны по сравнению с ручной дуговой сваркой. Высокая стоимость оборудования и сложность его эксплуатации, повышенные требования к сборке, в том числе к сохранению постоянного зазора, невысокое качество металла шва были основными причинами скептического отношения производственников к автоматической дуговой сварке. Тем не менее, при сварке протяженных швов и в ряде других случаев пусть даже еще не совершенная технология обладала определенными преимуществами. Одной из первых в Европе венская фирма «Элин» наладила выпуск сварочных головок и аппаратов для сварки угольным электродом, которые нашли применение при производстве труб и сосудов. Автоматическую сварку угольной дугой с целлюлозной защитой в 1930 г. использовали на заводах Германии. Фирма «Нешнл тюб дивижн» (США) внедрила автоматическую сварку под флюсом (в виде порошка) электродной проволокой диаметром 4,77 мм для производства труб диаметром до 1800 мм, получив большие преимущества в скорости сварки по сравнению с ранее применявшейся газопрессовой сваркой. Способ «Юнионмелт» использовали при изготовлении кораблей, тепло- и электровозов [258], труб и трубопроводов [259], сосудов высокого давления [260] и др. За одни проход удавалось сваривать листы толщиной до 25 мм. Внедрение в промышленность автоматических сварочных головок положило начало дальнейшей автоматизации и механизации сварочных и сборочных операций. В СССР одна из первых сборочно-сварочных линий была создана в 1930 г. на заводе «Серп и молот» (Харьков), где с помощью полуавтоматической сварки изготавливали рамы молотилок. В 1930-х гг. автоматические сварочные головки были включены в поточные линии по изготовлению грузовых вагонов и цистерн на заводах в Днепродзержинске, Калинине, Бежице, Нижнем Тагиле. Рабочие позиции были расположены в технологической последовательности, однако для перемещения изделий использовали цеховой транспорт. О применении дуговой автоматической сварки голой проволокой под флюсом в Европе в конце 1930-х — начале 1940-х гг. сообщений не имеется, хотя этот способ был уже известен, и многие страны располагали необходимой аппаратурой. В СССР автоматическую сварку рассматривали как основное средство интенсификации производства. Предприятия получали дополнительные средства на освоение новой высокопроизводительной техники — как отечественной, так и закупаемой за рубежом. Впервые разработка Института электросварки — сварка крестообразной проволокой — была внедрена на Вагоностроительном заводе в Бежице. В 1930 г. опыт внедрения показал, что разработки ИЭС не уступают по основным параметрам аппаратам фирм «Дженерал электрик», «Элин», «Кьельберг» и др. С 1932 по 1935 гг. завод «Электрик» (Ленинград) изготовил 102 автоматические головки АМГ—1 собственной конструкции для сварки плавящимся покрытым электродом и для сварки угольной дугой. С 1936 г. завод начал выпускать головки АГЭ—1 с приводом, работавшим на переменном токе (создан впервые в мире В. Е. Сахановичем). Автоматы использовали в судостроительной и вагоностроительной промышленности, при производстве резервуаров и других металлоемких изделий. В мае 1936 г. в Киеве по инициативе ИЭС состоялась Всесоюзная конференция по проблемам дуговой автоматической сварки. Участникам конференции были продемонстрированы установки для сварки и наплавки различных изделий, конструкции электродных проволок и оборудование для их изготовления. В конце 1930-х гг. большой опыт был накоплен в ИЭС при внедрении сварки под флюсом угольным электродом. К 1939 г. были определены составы флюсов и размеры гранул, требования к подготовке кромок, техника сварки. Установка для автоматической сварки угольным электродом была применена при изготовлении стальных балок. Этими способами выполняли стыковые соединения низкоуглеродистых сталей толщиной до 18 мм. Внедрение автоматической сварки требовало повышения культуры производства, специального ухода за оборудованием, более точной сборки свариваемых деталей. В СССР темпы исследований и опытно-промышленной проверки дуговой автоматической сварки намного превосходили темпы работ по совершенствованию этого способа в США и других странах. В течение 1939—1940 г. в Институте электросварки под руководством Е. О. Патона самостоятельно были разработаны не только принципы автоматической сварки под слоем флюса, но и решен весь комплекс вопросов, относящихся к конструированию специальной аппаратуры, составу сварочных материалов, режимам сварки. Производительность сварки плавящимся электродом была почти на порядок выше, чем у ручной дуговой сварки: благодаря разработанной аппаратуре (головка с дифференциалом) скорость при сварке в автоматическом режиме могла составлять 30 м/ч. Флюсы взаимодействовали с жидким металлом ванны, поэтому появилась возможность влиять на характер протекающих там металлургических реакций и улучшать качество металла шва. К концу 1930-х гг. были разработаны два вида флюсов — плавленые и неплавленые. Плавленые флюсы получали путем сплавления компонентов шихты. В США фирма «Дженерал электрик» осуществляла выплавку флюсов в электрических печах. Е. О. Патон предложил использовать для этих целей более производительные пламенные печи. Наиболее простой технологией изготовления флюсов было механическое смешивание крупинок и порошков различных материалов. Однако такой флюс-смесь разделялся послойно при транспортировке и в процессе подачи в зону сварки из-за неодинаковых размеров и плотности компонентов. Этих недостатков лишен керамический флюс. В СССР в 1938 г. он был предложен К. К. Хреновым (МММИ им. Н. Э. Баумана). При изготовлении флюса небольшие капельки клея, попадая на шихту, связывали ее в отдельные частицы. Была разработана еще одна технология производства — спекание брикетов шихты при повышенных температурах без сплавления, после чего брикеты измельчали. В керамические флюсы можно ввести любые компоненты (минералы, руды, ферросплавы, углеродистые вещества) независимо от их взаимной растворимости [261]. В. М. Кон (фирма «Вестерн райр энд стил», США) отмечал, что применение керамических флюсов при автоматической сварке позволяет ввести в металл шва такие легирующие вещества, как титан, молибден, марганец [262]. Однако воспользоваться этой возможностью в полной мере трудно, поскольку ванна существует несколько секунд, еще меньше времени остается на металлургические превращения и химические реакции. Поэтому предпочтение следует отдавать плавленым флюсам, при изготовлении которых уже прошли некоторые реакции. Состав керамических флюсов, использованных при сварке фирмой «Нешнл тюб дивижн» по патенту Б. С. Робинова, повторял состав качественных электродных покрытий. В 1934 г. В. Миллер запатентовал специальный флюс, содержащий диоксид титана —18%, полевой шпат — 53%, бентонит — 1%, соду — 6% и воду— 22% (пат. США № 1978316). Этот флюс наносили на кромки в виде пасты вручную. Он обеспечивал удовлетворительное качество швов при сварке низкоуглеродистых сталей. Плавленый флюс впервые был предложен Л. Т. Джонсоном и его соавторами в известном патенте на автоматическую сварку. Считая, что дуговой процесс здесь отсутствует, авторы изобретения рассматривали флюс, расплавляющийся за счет «джоулева тепла», как источник теплоты для металлической ванны. Флюс имел следующий состав: Са — 31,24%, MgO — 11,01%, SiO2— 52,40%, Аl2O3,— 4,11%, Fe2O3 — 0,13%. Сюда рекомендовалось вводить дополнительно CaF2 — 6%. Способ «Юнионмелт», несмотря на отрицание авторами дугового разряда, был реализован на автоматических головках для дуговой сварки. В лаборатории удалось сварить стальные пластины толщиной один дюйм (около 25 мм) за один проход при скорости, в несколько раз превышающей существовавшие ранее [160]. В 1940 г. В. М. Кон предложил флюс для сварки алюминия и его сплавов (пат. США № 2194200), отличающийся высокой температурой плавления, что обеспечило относительно длительное существование сварочной ванны. Порошкообразный флюс содержал следующие компоненты: Аl2O3 — 57,6%, SiO2 — 41,8%. TiO2 —0.6%, и в его состав добавляли флюоритовый концентрат [262]. В 1930 г. а США фирма «Вестингауз» применяла автоматическую дуговую сварку при изготовлении паровых котлов. Указывалось также на возможность и целесообразность выгодного использования ее при производстве других изделий и конструкций — мостов, металлоконструкций, судов, самолетов, автомобилей, вагонов и т. д. В 1928 г. в США трубы изготавливали из тонкого листового проката. Сварочные автоматы имели по две головки, из которых первая работала с голым электродом, а вторая — с армированным. Автоматическую сварку применяли в конце 1920-х гг. в США при изготовлении балок и колонн. Например, на одном из заводов близ Чикаго для этих целей был смонтирован автомат со столом длиной 20 м, состоящим из роликов длиной 900 мм, поставленных на расстоянии 1500 мм друг от друга по оси стола. Ролики имели на концах шейки для вращения в подшипниках, прикрепленных к двум швеллерам, которые являлись продольными балками стола. При помощи цепной передачи ролики приводились в движение от двигателя. Находили применение сварочные дуговые автоматы и на заводах фирмы «Дженерал электрик» при выполнении крупных работ в области электромашино- и аппаратостроения. Они показали высокую «выносливость», так как с их помощью в ряде случаев сварку, например, шва крупного гидрогенератора, можно продолжать больше часа. В США появились аналитические работы, раскрывающие тенденции развития автоматической дуговой сварки, в которых указывались пути дальнейшего усовершенствования оборудования, возможные области применения и т. д., доказывалась также экономическая выгода процессов автоматической сварки. Одной из главных причин, тормозивших развитие автоматической сварки в середине 1930-х гг., был недостаток сварочных автоматов. Большим недостатком была толчкообразная подача электродной проволоки. Инерционные силы, возникающие в системе автоматов, не способствовали быстрым переменам скоростей подачи электродной проволоки с неравномерным горением дуги, т. е. перемены скорости подачи электродной проволоки не могли быстро следовать за изменением напряжения на дуге, что нарушало нормальную работу. Это создавало у производственников мнение, что автоматические сварочные головки — ненадежные машины. Поэтому, несмотря на то, что выпуск автоматов в СССР начался с 1932 г., не все они работали даже к концу 1936 г.Перед Второй мировой войной в промышленности США работало 2,5 тыс. дуговых автоматов, а в СССР на заводе «Электрик» было выпущено около 400 автоматических головок для дуговой сварки. Создание в ИЭС автоматической сварки под флюсом и организация серийного выпуска сварочных головок открывало путь к совершенствованию производства ряда ответственных изделий. 20 декабря 1940 г. Совнарком СССР и ЦК ВКП(б) приняли постановление о внедрении скоростной автоматической сварки под флюсом в промышленность. Способ намечали освоить на 20 заводах в течение полугода. Были созданы условия для скорейшего изготовления оборудования и сварочных материалов. Новую технологию применяли при изготовлении крупных двутавровых балок на заводах им. В. М. Молотова (Днепропетровск), химического оборудования и сосудов высокого давления на заводе «Красный котельщик» (Таганрог), заводе им. С. Орджоникидзе (Подольск), вагонов на Калининском вагоностроительном заводе, Уралвагонзаводе (Нижний Тагил), котлов на Ворошиловграде ком паровозостроительном и Людиновском локомобилестроительном заводах, а также других ответственных изделий. Высокая производительность сварки при отличном качестве соединений стала возможной благодаря научно-исследовательской и конструкторской работе небольшого коллектива Института электросварки. За короткое время ИЭС стал лидером в совершенствовании автосварки под флюсом. Здесь были четко определены технологические возможности процесса; кроме аппаратуры и материалов, создано оригинальное вспомогательное оборудование, в частности, формирующие подкладки, флюсовые подушки и др. (рис. 98—101). Однако руководителя работ Е. О. Патона достигнутые успехи не удовлетворяли. Анализируя результаты внедрения, он отмечал: «Работы по скоростной сварке, проведенные на заводах в 1941 г., выявили чрезмерную сложность сварочной аппаратуры. Поэтому сотрудники Института электросварки задались целью упростить и усовершенствовать эту аппаратуру. Создан и испытан новый универсальный аппарат для скоростной сварки. Разработан новый способ автоматической сварки двумя проволоками. Взамен ненадежных пылесосов разработан отсос флюса форсункой, действующей сжатым воздухом заводской сети. Создан новый мундштук, надежно подводящий ток к концу электродной проволоки. Разработаны упрощенные флюсы, не требующие сплавления компонентов и изготавливаемые путем смешивания простейших сырых компонентов местного происхождения. В институте проведены работы по упрощению сварочной аппаратуры, по замене дефицитных двигателей постоянного тока двигателями трехфазного тока, выпущена сварочная головка с одним двигателем, работающая исключительно на переменном токе, устранены ненадежные электромагнитные муфты. Дальнейшее развитие получили вопросы, касающиеся технологии скоростной сварки под флюсом» (рис. 102, 103) [134]. 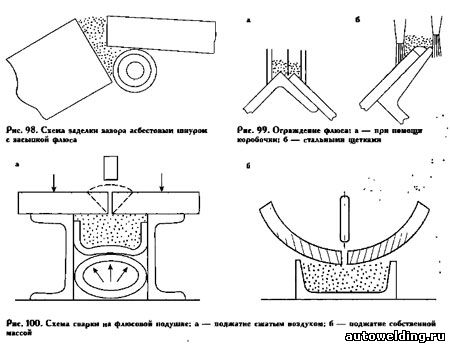
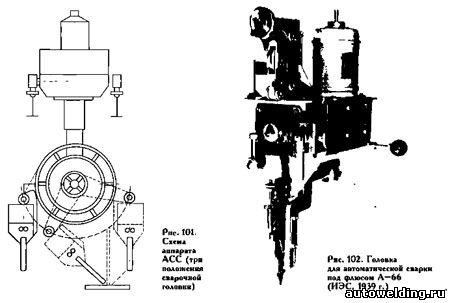
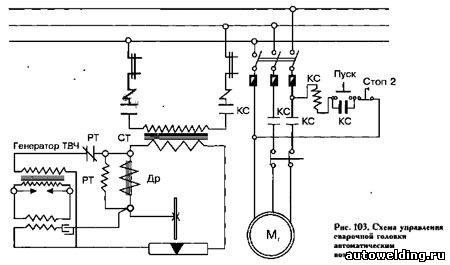
Рис. 103. Схема управления сварочной головки автоматическим возбуждением дуги
Успешное совершенствование и внедрение дуговой автоматической сварки под флюсом применительно к производству изделий из конструкционных низкоуглеродистых сталей в СССР было прервано в 1941 г. нападением фашистской Германии и эвакуацией Института электросварки на Урал в Нижний Тагил. Наука и промышленное производство были подчинены интересам обороны страны. Возникла настоятельная потребность в автоматической сварке броневых сталей. В годы Второй мировой войны значительно возросло производство изделий из цветных металлов, особенно из алюминиевых сплавов, наряду с автоматизацией газовой и газоэлектрической сварки, осуществлена автоматизация способа дуговой сварки в защитных газах, созданы материалы и технология дуговой автоматической сварки по флюсу. Решить эти задачи в кратчайшие сроки удалось на основе конструкторских разработок и результатов технологических исследований, выполненных в СССР, США и ряде других стран в 1920—1930-х гг.
|