Сварка в производстве оружия в СССР
Как известно, Первая мировая война дала импульс развитию сварки, поставив перед сварщиками ряд серьезных технических проблем. В последующие 1920—1930-е гг. сварка находила применение в производстве военной техники, особенно такой металлоемкой, как кораблестроение. Благодаря использованию сварки Германии удалось построить мощные линкоры, соблюдая ограничения в водоизмещении, наложенные Версальским договором. Во многих странах сварка нашла широкое распространение при производстве танков. К концу 1930-х гг. сварка стала ведущей технологией в производстве вооружений, почти полностью вытеснив клепку. Однако не все достижения сварочной науки и техники были использованы в оборонной промышленности СССР. В частности, не нашли применения автоматическая сварка голой проволокой под флюсом, дуговая сварка и резка под водой. В СССР в 1937 г. при изготовлении корпуса танка Т—26 клепка была заменена сваркой (лобовая и бортовая броня толщиной 15 мм и башенная — толщиной 25 мм). В декабре 1939 г. в ходе войны с Финляндией обнаружили слабость брони танков Т-28. И тогда к корпусам и башням уже готовых машин были приварены дополнительные броневые листы толщиной 20-50 мм. 19 декабря 1939 г. был принят на вооружение Красной Армии, а в марте 1940 г. утвержден к серийному производству средний танк Т—34. Оптимальный наклон верхнего и нижнего лобовых листов обеспечивал этому танку хорошую снарядостойкость и большую жесткость передней части корпуса, наиболее подверженной обстрелу. Верхняя расширенная часть корпуса благодаря наклону верхнего бортового листа хорошо защищала гусеницы. Листы кормовой части также располагались наклонно. Прямой была только нижняя часть корпуса. Все эти особенности необходимо было сохранить в машинах массового производства. Важнейшей задачей головного завода-изготовителя танка Т—34 стала разработка технологии соединения всех этих листов броневых плит, имеющих различную толщину и пересекающихся между собой под различными углами [363]. Корпус и башня Т—34 были сварены вручную электродами со специальной обмазкой. Заводы, приступившие к серийному изготовлению танков, приняли технологию многослойной ручной электродуговой сварки. Всего выполняли несколько десятков швов (рис. 104). 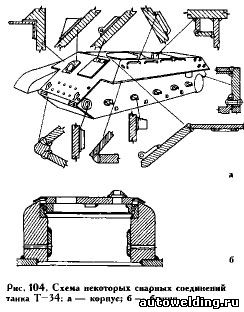
Выпуску новых боевых машин уделяли большое внимание. Танкостроители работали с предельным напряжением. К 22 июня 1941 г. на вооружении Красной Армии было уже 1355 танков Т—34 и 508 танков КВ-1. В первые же дни после нападения фашистских войск на СССР обнаружилось превосходство новых советских танков. В начале 1930-х гг. в ряде стран были разработаны конструкции самолета из коррозионно-стойких сталей и алюминиевых сплавов со сварными каркасами фюзеляжа, крыльев и хвостового оперения. В СССР это были самолеты А. И. Путилова «Сталь-2», контактной сваркой которых занимался П. Н. Львов. Большой вклад в развитие технологии изготовления узлов самолетов внесли А. С. Гельман, Е. В. Соколов и др. (ЦНИИТМАШ, Москва). Были разработаны устройства для контактной сварки узлов и приварки обшивки из хромоникелевых сталей толщиной 0,1—1,5 мм. С учетом необходимости сократить размеры зоны термического влияния, в которой возможна межкристаллитная коррозия, аппараты снабжали механическими синхронными прерывателями тока, позволяющими регулировать длительность импульсов тока от 0,02 с до нескольких секунд, совмещая импульсы с циклом плавления электродов. Атомно-водородной сваркой выполняли конструкции из металла толщиной 0,5—8 мм при силе тока 20—70 А. Диаметр присадочной проволоки составлял 1—3 мм, диаметр вольфрамовых электродов — 1,5—3 мм, расход водорода— 1—1,5 м3/ч. Самолетные конструкции из алюминиевых сплавов соединяли клепкой и газовой сваркой. В качестве присадочного материала использовали прутки того же состава или алюминиевую проволоку с содержанием 4,5—5% кремния, температура плавления которой ниже температуры плавления авиационных алюминиевых сплавов. Узлы из углеродистой, кремнемолибденовой, хромо-марганцево-кремниевой стали изготавливали с помощью газовой сварки нейтральным пламенем и ручной дуговой сварки. В последнем случае применяли электроды из низкоуглеродистой проволоки с обмазкой, в состав которой входили барий углекислый (1 часть), мел (0,5 части), диоксид титана (1 часть), оксид алюминия (0,25 части), перекись марганца (0,25 части), замешанные на жидком стекле. Толщина обмазки составляла 0,2 мм. Сваривали достаточно сложные авиационные конструкции. Для уменьшения внутренних напряжений и деформаций устанавливали определенный порядок наложения швов и их направление. По возможности, свариваемые элементы собирали так, чтобы они могли свободно перемещаться при нагреве. Опыт конструирования и производства самолетов типа «Сталь» особенно пригодился при создании бомбардировщиков и самолетов-разведчиков, обладавших высокой «живучестью». Благодаря трубчатым лонжеронам и гофрированной обшивке самолеты могли держаться в воздухе, несмотря на большое количество пробоин от пуль. В годы Второй мировой войны необходимость в ускорении производства вооружений при одновременном сокращении специалистов, занятых на этом производстве, явилась сильным толчком для расширения применения и совершенствования сварочных процессов. Основной упор делался на поиск резервов, скрытых возможностей технологий, разработанных до 1940-х гг. Война потребовала от ученых, конструкторов, инженеров, рабочих решать сложнейшие проблемы в кратчайшие сроки. Советским специалистам пришлось работать в особенно трудных условиях, несравнимых с условиями работы в других воюющих странах. Вероломное нападение фашистской Германии на Советский Союз, потеря значительной части территории Украины с металлургическими и машиностроительными заводами, демонтаж оборудования заводов и переброска его в восточные регионы затормозили в конце 1941 г. темпы производства оружия. С июня по ноябрь 1941 г. валовая продукция промышленности СССР уменьшилась в 2,1 раза. Перебазирование 1523 крупных предприятий и 10 млн. человек, создание на новых, часто необжитых, местах более 3500 производств потребовали колоссальных затрат усилий и средств. Применение сварочной техники помогло в рекордно короткие сроки быстро демонтировать оборудование эвакуируемых заводов, расчленяя его в необходимых случаях на транспортабельные части, и обеспечить их ускоренный монтаж на новом месте. В декабре 1941 г. объем производства оборонной продукции стал увеличиваться. Через неделю-другую после выгрузки оборудования эвакуированные предприятия начинали давать продукцию. На заводах Сталинграда, Сормовском (Горький), Уралвагонзаводе (Нижний Тагил) развернулось производство танков Т-34. «Узким» местом в бронекорпусных цехах оказались участки сварки броневых плит. На этой операции были заняты сотни квалифицированных сварщиков, производящих операции вручную. Выход был найден в применении автоматической сварки. С началом Великой Отечественной войны был эвакуирован в Нижний Тагил и размещен на территории Уралвагонзавода Институт электросварки, возглавляемый Е. О. Патоном. На территорию того же предприятия был перебазирован и Харьковский завод № 183 им. Коминтерна. В конструкторском бюро последнего и был спроектирован лучший средний танк Второй мировой войны — Т—34, а в цехах — налажено его производство. Все усилия Института электросварки были направлены на решение научно-технических и организационных проблем производства танков. Первой из таких проблем явились трещины, возникающие при автосварке броневых сталей. Оптимальным решением, позволившим сохранить все преимущества автоматической сварки под флюсом, было предложение размещать в разделке кромок низкоуглеродистую присадочную проволоку. С помощью этого приема не только уменьшалось науглераживание шва и зоны, но и повышалась производительность процесса. Одновременно с разработкой технологии были спроектированы и изготовлены две установки для сварки борта корпуса танка Т—34 с подкрылком. В январе 1942 г, был сварен первый опытный образец. Технология и оборудование прошли успешную апробацию. Тем не менее, производственники сначала отнеслись к автоматической сварке с недоверием. Только после настойчивых требований Е. О. Патона на участок, где были смонтированы автоматы, стали подавать заготовки корпусов — броневые плиты. Производительность автоматической сварки оказалась в 10 раз выше, чем ручной (башни танка были литыми). Конструкторская группа ИЭС подготовила 20 проектов специализированных установок для автоматической сварки различных типов швов на танках (рис. 105) и 8 — для сварки авиабомб и боеприпасов. Сварочные головки, изготовляемые в мастерских института, начали внедрять и на других заводах. 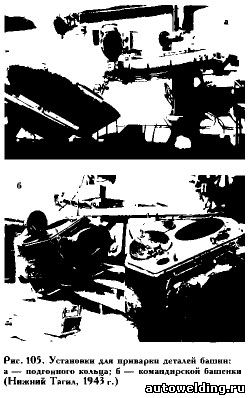
Однако коллективу института пришлось выдержать еще одно испытание — были исчерпаны запасы флюса АН-1, выплавленного еще до войны в Донбассе, оккупированном теперь Германией. Возникла реальная угроза отказа от автоматической сварки. Фундаментальным вкладом в развитие металлургии сварки можно назвать результаты поиска новых составов флюсов, в первую очередь из местного, доступного сырья. Опыт исследований устойчивости горения дуги, особенностей плавления электродов и ванны, начатых еще в Сварочной лаборатории ВУАН и продолженных в институте при создании первого отечественного флюса, позволил небольшой группе исследователей установить точные требования к этому сварочному материалу и в крайне сжатые сроки предложить новые эквивалентные компоненты. Однако для того, чтобы наладить промышленный выпуск новых флюсов, необходимо было разрабатывать карьеры, построить печи. В условиях военного положения это было почти невозможно. Наилучшим выходом из этого положения Е. О. Патон признал применение в качестве флюса доменных шлаков, А. И. Коренной исследовал шлак домны, работающей на древесном угле, в котором практически отсутствовала сера. Чтобы стать полноценным сварочным флюсом, доменному шлаку недоставало 10% оксида марганца. Металлурги добавили в шлак марганцевую руду, и к лету 1942 г. страна получила новый сварочный материал — флюс AШ. Была еще одна проблема: распространение автоматической сварки под флюсом. Сконструированная в мирное время, рассчитанная на эксплуатацию в нормальных условиях головка А—66 оказалась теперь недостаточно надежной. Два двигателя, обеспечивающие подачу электродной проволоки, в условиях военного времени выполняли свои функции плохо — колебания напряжения в сети влияли на мощность двигателя постоянного тока, а следовательно, и на скорость подачи. Нарушался режим сварки. Избежать брака в таких условиях было невозможно. Вторым недостатком (о котором в мирное время никто бы и не вспомнил) довоенной головки была ее сложность. Принцип автоматического регулирования длины дуги с помощью двухмоторного механизма стал в свое время удачной разработкой института. Но как наладить массовый выпуск таких головок теперь, когда запасы комплектующих деталей кончаются и среди них оказались дефицитные элементы? Кроме того, управление автоматами представляло определенную трудность для рабочих с низкой квалификацией. В 1942 г. старший научный сотрудник Института электросварки В. И. Дятлов предложил упростить конструкцию сварочных автоматов, исключив сложную систему возбуждения и поддержания длины дуги. В основу новой технологии и конструкции аппарата было положено явление саморегулирования мощной электрической дуги при постоянной скорости подачи электродной проволоки. Механическая часть сварочной головки, разработанная П. И. Севбо, и электрическая схема аппарата управления, разработанная Б. Е. Патоном, были настолько просты (рис. 106), что позволяли наладить выпуск аппаратуры силами мастерских института в достаточном для оборонной промышленности количестве. Это обстоятельство, а также простота аппаратов в эксплуатации обеспечили возможность широкого внедрения автоматической сварки под флюсом в годы Великой Отечественной войны и послевоенное время. 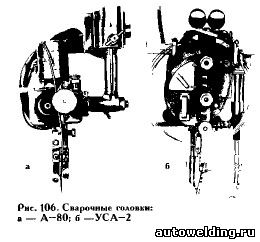
Производительность автоматической сварки не шла ни в какое сравнение с производительностью других способов сварки. Например, на приварке днища подкрылка к борту двумя мощными швами длиной более 5 м квалифицированный сварщик работал около 20 ч. Подросток, после 5—10 дней обучения, мог сварить автоматом этот шов за 2 ч. Сектор погона башни вручную сваривали за 5 ч, а с помощью автомата эту операцию производили за 49 мин; сварка носов длилась вместо 7,3 только 1,4 ч и т. д. Полезный съем продукции с единицы производственной площади увеличился в несколько раз. Ввод одной установки освобождал семь сварочных трансформаторов и восемь дросселей-регуляторов. Заводы экономили до 42% электроэнергии. В 1943 г. ИЭС установил на заводах Наркомата танковой промышленности около 50 аппаратов для автоматической сварки. В Нижнем Тагиле начала работать поточная линия по производству бронекорпусов со специальными сварочными установками, основой которых были автоматы. Уже тогда были созданы конструкции аппаратов для выполнения всех основных типов соединений, встречающихся в машиностроении: станки-автоматы карусельного типа для круговых швов, самоходные головки для сварки продольных швов небольшой длины. Пуск поточной линии позволил высвободить 280 квалифицированных рабочих. Оборонная промышленность СССР продолжала наращивать выпуск боевой техники. Итог 1943 г. — 24 тысячи танков и самоходно-артиллерийских установок (рис. 107). 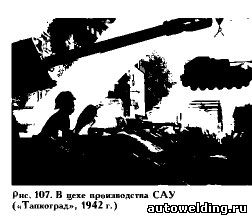
Повышалось и качество оружия. На фронте появились боевые машины ИС—1, а в конце декабря были изготовлены образцы ИС—2 — тяжелого танка с мощной броней и 122-миллиметровой пушкой. Патоновцам пришлось разработать технологию сварки брони толщиной 90 и 120 мм (рис. 108). 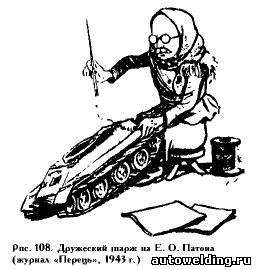
Следующим шагом в развитии сварочной аппаратуры стало создание сварочных тракторов — облегченных сварочных головок, смонтированных на самоходных тележках. Первый такой аппарат был разработан в ИЭС в 1944 г. (Б. Е. Патон и П. И. Севбо). Изменение принципа перемещения сразу же значительно расширило область применения автоматической сварки под флюсом. Трактор позволял сваривать швы, практически ограничиваемые только длиной кабелей питания и управления. В послевоенные годы этими аппаратами начали сваривать конструкции корпусов судов, элементы резервуаров, трубы, балки мостов и др. Тогда же была создана первая конструкция полуавтомата, обеспечивающая подачу электродной проволоки через держатель, перемещаемый вручную (Б. Е. Патон); разработан сварочный пистолет для приварки шпилек диаметром до 12 мм под флюсом в вертикальном и потолочном положении (Н. Г. Остапенко). Война не остановила развития сварочной науки. Не прекращая напряженной производственной работы, ученые-сварщики проводили экспериментальные исследования, закладывали теоретический фундамент, необходимый для дальнейшего совершенствования технологии, аппаратуры, сварных конструкций. Е. О. Патон переработал свою книгу «Скоростная автоматическая сварка под слоем флюса», которая вышла в свет в 1942 г. третьим изданием. Эта книга стала ценным пособием по внедрению скоростной автоматической сварки под флюсом на многих предприятиях страны. Б. Е. Патон и А. М. Макара в 1943-1944 гг. исследовали процесс сварки под флюсом и доказали, что вопреки мнению зарубежных специалистов этот способ по своему основному принципу (источник теплоты) не отличается от способа Н. Н. Бенардоса и Н. Г. Славянова, а является лишь его современной модификацией. В монографии Б. Е. Патона и А. М. Макары впервые изложены основы теории автоматов для дуговой сварки. Результаты этих исследований имели большое значение как для дальнейшего развития сварочной науки, так и для немедленного практического использования при разработке новых флюсов, выборе режимов, для создания новых аппаратов. Успешное продолжение исследований металлургических особенностей дуговой сварки под флюсом В. И. Дятловым, Т. М. Слуцкой другими сотрудниками Института электросварки позволило в кратчайшие сроки разработать технологию и флюс для сварки брони. Но не менее важным итогом научной и конструкторской деятельности коллектива института явилось создание на основе закона саморегулирования дугового Процесса нового класса сварочных автоматов — постоянной скоростью подачи электродной проволоки. В 1943 г. инженер А. И. Коренной предложил способ автоматической сварки расщепленным электродом, научные сотрудники Б. Е. Патон, А. М. Макара и С. А. Островская — способ сварки несколькими раздвинутыми дугами. Эти и ряд других идей в последующем были развиты в высокопроизводительные способы сварки (трехдуговая автоматическая сварка под флюсом, шланговая полуавтоматическая и др.). В специальной монографии, подготовленной Е. О. Патоном и его сотрудниками и опубликованной в 1944 г., изложены основы проектирования установок для автоматической сварки строительных металлоконструкций, а в других работах освещен опыт развития и использования автоматической сварки под флюсом в различных отраслях промышленности. Большие объемы работ по внедрению скоростной сварки под флюсом выполнил отдел сварки ЦНИИТМАШ. Разработанный К. В. Любавским флюс ОСЦ—45 хорошо зарекомендовал себя при сварке низкоуглеродистых сталей, из которых изготовляли боеприпасы. Так же, как и Институт электросварки АН УССР, ЦНИИТМАШ обеспечивал производство бомб и снарядов всем необходимым: технологической документацией, проектами разнообразных установок и т. д. Здесь были разработаны и другие марки флюсов, в том числе из недефицитного сырья и из шлака доменных печей. Коллектив ученых ЦНИИТМАШ разработал сварочную головку с постоянной скоростью подачи проволоки с фрикционной передачей. Скорость подачи электродной проволоки в аппарате плавно регулировалась, что давало возможность достичь хорошей настройки режима сварки. В 1944 г. под руководством И. Л. Бринберга в ЦНИИТМАШ был спроектирован сварочный трактор, который мог сваривать стыковые и угловые швы. В освобождаемых районах и районах боевых действий необходимо было сваривать сотни тысяч стыков рельсов. Сотрудники отдела сварки ЦНИИТМАШ и Народного комиссариата путей сообщения в конце 1942 г. предложили новый технологический процесс дуговой сварки рельсовых стыков без поворота рельса. В 1943 г. был спроектирован, смонтирован и пущен в эксплуатацию первый в СССР рельсовый поезд, изготовленный на заводе «Ревтруд» НКПС. В 1942 г. при участии ЦНИИТМАШ была спроектирована и изготовлена установка для работы с подвижной платформы, осуществлявшая контактную сварку рельсов. Установка, размещенная на первом в СССР рельсосварочном поезде, сварила за год более 30 тыс. стыков. В 1943 г. работало уже 10 таких поездов. С первых дней войны работа МММИ (с 1943 г. МВТУ им. Н. Э. Баумана) была направлена на производство вооружения. Под руководством К. К. Хренова и Г. А. Николаева решался ряд вопросов, возникавших в связи с переводом промышленности на производство и ремонт военной техники. В кратчайшие сроки были разработаны конструкции артиллерийского и стрелкового оружия с широким использованием сварки в технологическом процессе. В решении этой проблемы активное участие приняли Г. А. Николаев, С. Т. Назаров и другие сотрудники МВТУ. Г. С. Шпагин, конструктор пистолета-пулемета ППШ, писал: «С самого начала я поставил перед собой цель, чтобы новое автоматическое оружие было предельно простым и несложным в производстве. Если по-настоящему вооружить огромную Красную Армию автоматами, подумал я, и попытаться это сделать на базе принятой ранее сложной и трудоемкой технологии, то какой же неимоверный парк станков надо загрузить, какую огромную массу людей надо поставить к этим станкам. Так я пришел к мысли о штампосварной конструкции. Надо сказать правду, даже знатоки оружейного производства не верили в возможность создания штампосварного автомата ...». Конструкторы, руководители производства понимали, что только простота изготовления позволит выпустить нужное фронту количество оружия и обеспечит решающий выигрыш во времени. Такую возможность предоставляло использование сварки. С первых дней войны сварщики Ленинграда переключились на выпуск военной продукции и сделали все возможное для обороны города. Так, в ноябре 1941 г. на судостроительном Балтийском заводе за несколько суток изготовили конструкции переправы танков через Неву. Продолжали постройку эсминцев, сторожевиков, шхерных мониторов, тральщиков. Только за второе полугодие 1941 г. были достроены 84 корабля, В период блокады в Ленинграде и Кронштадте было отремонтировано около 850 кораблей. Строительство и ремонт судов продолжали всю войну. Только на верфи «Алмаз» было построено 700 катеров различного назначения. Особое значение для блокадного Ленинграда имела связь с «Большой землей». В навигацию 1942 г. было построено 14 самоходных барел грузоподъемностью до 900 т каждая (рис. 109). Секции сваривали в заводских условиях и там же на прихватках собирали корпус. Затем перед транспортировкой корпус разбирали, секции по Неве доставляли в район Охты, где их перегружали на железнодорожные платформы и доставляли на Ладожскую верфь. Строительство вели неслыханными темпами — последний корабль собрали за шесть дней. Ручную дуговую и газовую сварку широко применяли для ремонта танков . 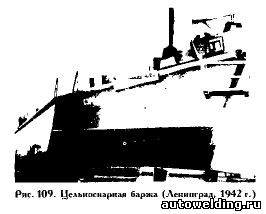
Весной 1942 г., когда Ленинград находился в блокаде, было принято решение о строительстве сварного подводного бензопровода через Ладожское озеро. Строительство было поручено Сварочно-монтажному тресту Наркомстроя (А. С. Фалькенич). Трубопровод высокого давления имел диаметр 101 мм и протяженность 30 км, в том числе 8,5 км по суше на восточном и западном берегах и 21,5 км под водой на глубине от 1 до 12,5 м. Толщина стенок труб составляла от 4,5 до 3,5 мм. Трубы, поставлявшиеся из наличных запасов, сертификатов не имели, химический анализ и механические испытания металла труб также провести не удалось. Их собирали и сваривали в секции длиной 50—80 м, а затем стягивали и сваривали в нитку. Поворотную сварку труб в секции осуществляли электродуговой сваркой электродами с меловой обмазкой; неповоротную сварку секций в нитку производили газовой сваркой. Только в одном из стыков была обнаружена неплотность, через которую в течение 1 мин просачивалась одна капля керосина. Бензопровод успешно эксплуатировался в течение 20 месяцев, вплоть до прорыва блокады. В период войны были построены и другие трубопроводы (крупнейший из них Астрахань—Сталинград). Ученые-сварщики Ленинграда (Н. О. Окерблом, А. А. Алексеев, Д. Н. Сагалович и др.) организовали ремонт военной техники, нашли новый способ изготовления понтонов, готовили молодых сварщиков на курсах. В годы войны возникла серьезная потребность в подводной сварке и резке металлов для ремонта кораблей, мостов, для аварийных и спасательных работ. Еще ранее К. К. Хренов в лабораторных условиях доказал возможность применения дуговой сварки и резки плавящимся электродом под водой. При переходе от лабораторных опытов к широкому практическому внедрению были решены такие вопросы, как безопасность водолазов, работающих с открытыми электродо-держателями, герметичность электродных покрытий при многочасовом пребывании под водой. К. К. Хренов продолжил исследования и разработку техники сварки и резки под водой в специальной лаборатории, организованной в марте 1942 г. при Московском электромеханическом институте инженеров железнодорожного транспорта. Были разработаны составы и конструкции электродных покрытий, обеспечивающих стабильность горения дуги под водой. Лаборатория обучала сварочным работам водолазов-сварщиков для Военно-Морского Флота и железнодорожного транспорта, а в декабре 1942 г. был сформирован специальный поезд, в состав которого вошли электростанция, водолазная станция, сварочные агрегаты, подъемные и плавательные средства и т, д. Персонал поезда оперативно освобождал фарватеры рек от взорванных мостов, проводил сложные работы по восстановлению мостов через Дон, Днепр, осуществлял подъем затонувших кораблей. Результаты всесторонних исследований свойств и состава металла швов на сваренных под водой деталях доказывали возможность применения сварки для ремонта подводных частей корпусов кораблей прямо на плаву. С этой целью было создано несколько станций подводного судоремонта. К. К. Хренов подготовил соответствующие инструкции и методические пособия. В период войны по примеру Советского Союза сварку и резку под водой начали применять и другие воюющие страны. В 1941 г. электросварочное оборудование начал выпускать завод в пос. Новая Утка (Свердловская обл.), куда была эвакуирована часть рабочих и ИТР завода «Электрик». В кратчайшие сроки коллектив освоил производство и выпустил за годы войны 6 тыс. передвижных сварочных агрегатов, смонтированных на автомашинах, 15 тыс. сварочных трансформаторов, около 500 головок АГЭ—5—2 для дуговой сварки. В годы войны получила развитие термитная сварка металлов. Научными сотрудниками отделения связи ЦНИИ железнодорожного транспорта (М. И. Вахнин, А. Н. Кукин, А. А. Талыков) был разработан магниевый термит, который упростил технологию этого способа и позволил легко производить сварку телеграфных и телефонных проводов диаметром 3—6 мм в полевых условиях. В 1941 г. создана секция по научной разработке проблем электросварки и электротермии Академии наук СССР. Под руководством В. П. Никитина был разработан способ автоматической сварки с разделением процессов тепловой подготовки основного и присадочного металлов (сварка с заливкой жидкого присадочного металла). Дефицит металла, в том числе стального проката, вынуждал изготавливать металлоконструкции и вооружение из некондиционных по составу сплавов. Благодаря удачно составленным обмазкам электродов «сваривающимися» были признаны многие марки сталей. Универсальными, обеспечивающими высокое качество шва оказались электроды серии УОНИ-13, разработанные К. В. Петранем. Большую работу по созданию новых электродных покрытий из недефицитных материалов выполняли в МВТУ им. Н. Э. Баумана (К. К. Хренов и др.), в ЦНИИТМАШ (А.А.Алов, В. И. Ярхо и др.), на Уралмаше (А. Н. Шашков). В состав обмазки электродов ОММ—5 были введены древесина (вместо муки и крахмала) и гранит (вместо полевого шпата). В ЦНИИТМАШ были созданы электроды ЦС—1 и ЦС—2 для наплавки твердых сплавов сормайт, электроды для сварки углеродистых сталей. В годы войны Н. Н. Рыкалин провел исследования в области расплавления электродов и про плавления основного металла. А. А. Алов работал над изучением шлаковых включений И пор в металле шва. Успешные исследования точечной контактной электросварки элементов больших толщин проводил А. С. Гельман. Над раскрытием механизма возникновения напряжений и деформаций в процессе сварки работали В. П. Вологдин и Н. О. Окерблом. Теоретические исследования прочности элементов сварных конструкций выполнил С. А. Данилов. В условиях наступления Советской Армии, когда промышленные ремонтные базы городов остались далеко в тылу, а предприятия освобожденных городов еще не работали, начали создавать полевые подвижные ремонтные базы. Для этого переоборудовали танки, в основном производства США и Англии, поставляемые по ленд-лизу и имевшие худшую, чем советские танки, боеспособность. В комплект оборудования входили установки для ручной дуговой сварки и резки.
|