Сущность кислородной резки, классификация и области применения
Кислородная резка — один из наиболее распространенных технологических процессов термической резки. Это процесс интенсивного окисления металла в определенном объеме с последующим удалением жидкого оксида струей кислорода. Резку начинают с нагрева верхней кромки металла подогревающим пламенем до температуры воспламенения металла в кислороде, которая в зависимости от химического состава стали составляет 1323... 1473 K. По достижении температуры воспламенения на верхней кромке металла на нее из режущего сопла подают струю кислорода. Сталь начинает гореть в кислороде с образованием оксидов и выделением значительного количества теплоты, обеспечивающей разогрев металла у верхней кромки до температуры плавления. Образовавшийся на верхней кромке расплав оксидов и железа перемещается по боковой кромке металла струй кислорода и осуществляет нагрев нижних слоев металла, которые последовательно окисляются до тех пор, пока металл не будет прорезан на всю глубину. Одновременно с этим начинают перемещать резак с определенной скоростью в направлении резки. На лобовой поверхности реза по всей толщине образуется непрерывный слой горящего металла. Окисление металла начинается сверху и последовательно передается нижним слоям металла. При кислородной резке (рис. 14.1) струя кислорода перемещается в разрезе со скоростью ωг и окисляет жидкий металл в слое толщиной h'ж. За счет его окисления выделяется определенное количество теплоты, которая расплавляет металл в слое толщиной hж - h'ж и подогревает твердый металл впереди, по фронту резки. Окисление слоев расплавленного металла осуществляется при интенсивном перемешивании струей расплава на лобовой поверхности реза. 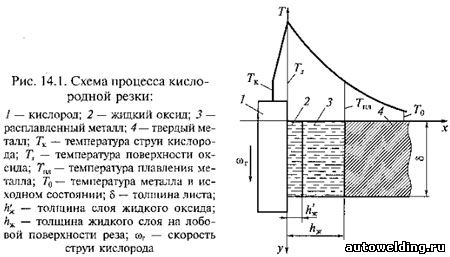
Для протекания процесса кислородной резки необходимы: - контакт между струей кислорода и жидким металлом;
- подогрев неокисленного металла до температуры воспламенения;
- выделение продуктами горения определенного количества теплоты, достаточного для создания на поверхности реза слоя расплавленного металла;
- достаточная вязкость жидкого расплава для обеспечения возможности перемешивания жидкого металла струей кислорода.
Приведенные условия определяют требования к металлу, обрабатываемому кислородной резкой. Прежде всего, температура плавления оксидов должна быть ниже температуры плавления металла. В противном случае струя кислорода не сможет окислить расплавленный металл. Помимо этого температура воспламенения металла должна быть выше температуры его плавления, иначе металл начнет плавиться и выдуваться струей кислорода без последующего его окисления (плавильный процесс). Этот процесс требует значительных энергетических затрат. При малой теплоте образования оксида лобовая поверхность реза не прогревается до температуры плавления, и процесс резки прерывается. По той же причине отрицательно сказывается на возможности подвергать металл кислородной резке его высокая теплопроводность. Значительная вязкость расплава не обеспечивает его турбулизации в поверхностном слое, что уменьшает выделение теплоты на кромке реза. Среди чистых металлов кислородной резкой хорошо обрабатываются железо, титан и марганец. Так, температура плавления железа равна 1808 К, температура воспламенения — 1323 К; температура плавления FеO составляет 1643 К. Тепловой эффект реакции горения железа довольно высок (269 МДж/моль). Поскольку теплопроводность железа невелика, лобовая поверхность реза разогревается при резке до высоких температур (1873 ...2273 К). Реакция горения титана сопровождается более значительным тепловым эффектом (906 МДж/моль), тогда как теплопроводность титана ниже, чем у железа. Температура лобовой поверхности при резке титана превышает 2773 К. Поэтому он разрезается с более высокой скоростью, чем сплавы железа. Нельзя разрезать обычным кислородным способом Ni, Сu, Аl, Mg, Сr и Zn. В технике за редким исключением применяют не чистые металлы, а их сплавы, причем наиболее широко используют сплавы железа и углерода — сталь и чугун. Для придания стали высоких прочностных характеристик, пластичности, коррозионной стойкости в различных средах, жаропрочности и других свойств в ее состав вводят различные легирующие элементы — Mn, Si, Сr, Ni, Ti, Аl и др. Наличие примесей влияет на возможность обработки стали кислородной резкой, поскольку в слое жидкого расплава, выдуваемого из реза кислородной струей, образуются тугоплавкие оксиды. Они уменьшают жидкотекучесть расплава и препятствуют интенсивному теплообмену между расплавом и кислородом режущей струи. Элементы, расположенные в ряду химической активности по отношению к кислороду за железом, снижают активность окисления расплава. При окислении расплава, перемещаемого струей кислорода вдоль лобовой поверхности реза, их содержание в расплаве увеличивается, что приводит к торможению процесса окисления стали. Остановимся более подробно на влиянии легирующих примесей на процесс кислородной резки стали. Увеличение содержания углерода в стали, с одной стороны, приводит к повышению температуры ее воспламенения в струе кислорода, а с другой — к снижению температуры плавления. При содержании углерода не более 1 % практически все стали (низкоуглеродистые, конструкционные, в том числе инструментальные) обрабатывают кислородной резкой без затруднений. Кроме того, повышение содержания углерода в стали снижает ее вязкость. Именно этим обстоятельством можно объяснить более низкие скорости резки армко-железа, содержащего сотые доли процента углерода. Увеличение содержания углерода в стали (более 1 %) вызывает повышение температуры ее воспламенения и снижение температуры ее плавления (рис. 14.2), что приводит к нарушению одного из условий осуществимости кислородной резки (см. выше). В связи с этим чугуны не могут подвергаться обычной кислородной резке. 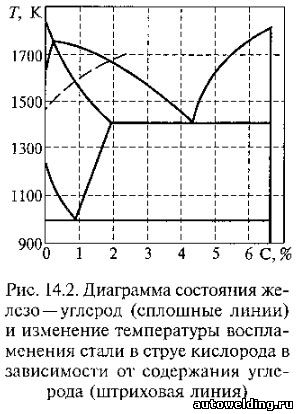
Марганец и медь в количествах, обычно встречающихся в сталях, практически не влияют на технологические параметры кислородной резки. Этим способом можно разрезать стали, содержащие до 18 % марганца. Кремний, хром, алюминий и никель при увеличении их содержания в стали ухудшают процесс резки. В низколегированных сталях кремний обычно содержится в небольшом количестве (до 2 %), что почти не сказывается на скорости резки. При содержании в сталях до 2 % хрома их также разрезают с использованием режимов, принятых для низкоуглеродистых сталей. Увеличение содержания хрома до 6 % приводит к снижению скорости резки. При еще более высоком содержании хрома из-за образования тугоплавких оксидов хромистые стали не могут быть обработаны обычной кислородной резкой. В этом случае в разрез вводят специальные флюсующие материалы. Стали с высоким содержанием никеля (до 30 %) можно разрезать кислородным способом, если содержание углерода в них не превышает 0,35 %, иначе резка затрудняется и требуется предварительный подогрев. Кислородная резка стали, содержащей до 10 % вольфрама, осуществляется без затруднении. При более высоком содержании вольфрама в разрезе образуется большое количество вязких тугоплавких оксидов вольфрама, препятствующих удалению расплава из реза. В этом случае необходимо применять специальные способы кислородной резки. Следует отметить, что приведенные данные по влиянию легирующих примесей на способность стали подвергаться кислородной резке относятся лишь к отдельным компонентам. В стали, как правило, имеется несколько составляющих, которые при окислении могут образовывать в разрезе шлаки сложного химического состава, существенно влияющие на возможность кислородной резки стали. По типу образующихся разрезов различают разделительную кислородную резку, при проведении которой металл окисляется струей кислорода на всю толщину, после чего одна часть металла отделяется от другой, и поверхностную, позволяющую удалять слои металла с поверхности изделия. Низкоуглеродистые, конструкционные и низколегированные стали подвергают обычной кислородной резке, тогда как заготовки из высоколегированных сталей, чугуна и цветных сплавов — кислородно-флюсовой. Существуют особые способы кислородной резки — подводная, выполняемая, как правило, при ремонтных работах под водой, копьевая и электрокислородная. В настоящее время кислородная резка наряду с дуговой сваркой является одним из основных технологических процессов в заготовительном производстве и находит широкое применение в металлургии, металлообрабатывающих отраслях промышленности и строительстве. По степени механизации процесса кислородная резка подразделяется на ручную и механизированную. Ручная кислородная резка используется на тех предприятиях, где объем перерабатываемого металла невелик и применение средств механизации экономически неоправданно. Она служит для вырезки заготовок под последующую ковку и штамповку по разметке из листа, резки профильного проката и труб, отрезки прибылей и литников в литейном производстве, а также при проведении ремонтных работ. За последние годы достигнуты серьезные успехи в разработке и выпуске средств механизации процесса кислородной резки, и прежде всего координатных портальных и портально-консольных машин с фотоэлектронным и числовым программным управлением. Использование многорезаковых машин обеспечило значительное повышение уровня механизации газорезательных работ, рост производительности труда в заготовительном производстве и экономию материалов. В настоящее время в ведущих отраслях промышленности, таких, как тяжелое, транспортное, энергетическое и химическое машиностроение, связанных с переработкой наибольшего объема металла, уровень механизации газорезательных работ составляет 70... 80 %. Высокий уровень механизации процесса резки на современных машинах с фотоэлектронным и особенно с числовым программным управлением создал предпосылки для разработки и внедрения в производство поточных комплексно-механизированных и гибких автоматизированных линий термической резки листовой стали, на которых механизированы не только процесс резки, но и подготовка листа, его подача к режущей машине, разборка вырезанных заготовок, их разметка и складирование. Экономичным технологическим процессом зарекомендовала себя кислородная резка в металлургии при удалении прибылей, местных дефектов в отливках, сплошной огневой зачистке слябов и блюмов на специальных машинах с целью удаления дефектного поверхностного слоя перед прокаткой. Кислородная резка является одним из основных технологических процессов при непрерывной разливке стали и служит для разделения слябов и блюмов на мерные заготовки. Кислородно-флюсовая резка коррозионно-стойких сталей, чугуна и цветных металлов нашла широкое применение для обработки отливок, листовой стали и труб в различных отраслях экономики. Полевой Г.В. "Газопламенная обработка металлов"
|