Источники питания и аппараты управления электрической сваркой. История развития
Изучение тепловых воздействий тока, изобретение дуговой и контактной сварки стали возможными с появлением постоянно действующих источников электрической энергии. Ко времени изобретения первого способа дуговой сварки Н. Н. Бенардос не располагал источником тока, способным длительное время обеспечивать в сварочной цепи силу тока более 100 А и выдерживать короткие замыкания. Он использовал батарею аккумуляторов необходимой мощности, заряжаемую и подпитываемую в процессе сварки слаботочным генератором [20]. Первый генератор, обеспечивающий питание процесса сварки «напрямую», был изготовлен Н. Г. Славяновым в 1888 г. [89]. Источники тока обоих изобретателей использовали в отдельных случаях несколько десятилетий — уже после того, как начали разрабатывать специальные источники, учитывающие особенности дуговой сварки [95]. Однако известные к началу XX в. генераторы общего назначения имели серьезные недостатки: низкий КПД, недостаточную устойчивость дуги, сложность управления и пр. Перед электротехниками возникла задача создания специальных сварочных генераторов, обладающих лучшими эксплуатационными характеристиками. В конце 1890-х гт. Ф. Рихтер (фирма «Крупп», Германия) усовершенствовал установку Бенардоса, исключив батарею аккумуляторов и обеспечив возбуждение магнитного потока полюсов генератора постоянного тока с помощью специального аккумулятора, включенного последовательно в цепь аналогично регулирующему реостату. От генераторов с постоянным напряжением, подобных генератору Н. Г. Славянова, сварочная техника довольно быстро перешла к генераторам с регулируемым напряжением, кроме того, они снабжались обмоткой для обеспечения затухания колебаний тока. В 1904 г. Э. Розенберг (Австрия), занимаясь динамомашинами для освещения в поездах, изобрел генератор поперечного поля (рис. 40). 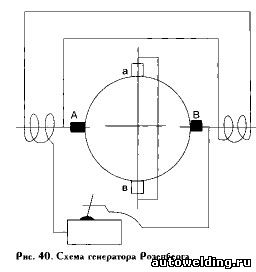
На коллекторе размещены четыре щетки. Две главные рабочие щетки А, В расположены по оси полюсов генератора. Вспомогательная пара щеток а, b находится на нейтрали к потоку полюсов и замкнута накоротко. Намагничивающая обмотка возбуждения подключается последовательно с якорем и дугой. На холостом ходу при разомкнутой цепи щеток А—В генератор обеспечивает максимальное напряжение. При подключении цепи главных щеток под нагрузку возникают потоки в последовательной обмотке и продольный поток н якоре, создаваемые рабочим током главной цени и направленные по оси Полюсов. Эти потоки действуют встречно, и результирующий поток ранен их разности. Поперечный поток, создаваемый коротко замкнутой обмоткой якоря, является основным рабочим потоком генератора и взаимодействует с потоками последовательной обмотки и продольным потоком якоря. Благодаря конструктивным особенностям полюсов, корпуса и якоря генератора размагничивающий продольный поток якоря непрерывно возрастает с увеличением силы сварочного тока, а результирующий поток в воздушном зазоре сначала возрастает при малых нагрузках, а затем уменьшается при увеличении сварочного тока. Внешняя характеристика генератора Розенберга падающая. Он оказался пригодным для ручной дуговой сварки плавящимся электродом. Развитие электротехники привело к созданию в разных странах множества фирм, компаний, заводов по производству электродвигателей и генераторов. Первые источники питания сварщики мастерили сами, основываясь на тех, что выпускались для разных других целей. В первом десятилетии XX в. в Германии и США начали выпускать специальные сварочные генераторы. С 1905 г. сварочные генераторы поперечного поля стала изготавливать фирма «АЭГ» (Германия) [122]. До Второй мировой войны генераторы этой системы выпускали также фирмы «Элин» (Австрия), «Сименс-Шуккерт» (Германия) и др. Конструкция генератора Розенберга явилась базой для развития сварочных генераторов с вращающимися частями. Совершенствованием схемы регулирования тока генератора занимались Бергманн, Кремер, Бурке-Скотт и др. Первый сварочный генератор в США был импортирован в 1907 г. из Германии Э. Зимундом (фирма «Зимунд-Венцель»), Генератор обеспечивал силу тока до 200 А с регулированием напряжения от 15 до 60 В. Зимунд передал динамомашину А. Эспиесу (фирма «Крокер энд Кортис электрик»), который скопировал ее и выпустил небольшую серию мотор-генераторов с ременным приводом [123]. Этот источник постоянного тока внедряли для сварки плавящимся электродом. Через два года Д. Вестингаус также начал серийное производство сварочных установок постоянного тока. В 1907 г. первый генератор с регулируемым напряжением был выпущен на заводе «Линкольн Электрик Компани», а фирма «Си-Си Электрик Компани» сделала мотор-генератор. Его разработал инженер-электрик Артур де Эспис, взяв за основу электрическую машину немецкого инженера Э. Зимунда и учтя работу первого специального генератора Славянова. В 1909 г. свой генератор постоянного тока создал Джон Вестингаус. И, наконец, сварочные мотор-генераторы стала выпускать фирма «Дженерал электрик Компани», возглавляемая Ч. А. Коффиным. Наиболее широкое применение в самом начале XX в. нашел генератор К ре мера, который отличался от обычных машин постоянного тока системой обмоток полюсов. Он имел три обмотки: сериесную обмотку А, шунтовую обмотку самовозбуждения В, действующую в одном направлении с обмоткой независимого возбуждения С, которая действовала в обратном направлении по отношению к обмотке А (рис. 41). 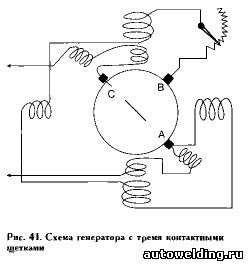
При увеличении силы тока, вызванном уменьшением сопротивления рабочей цепи, обмотка А уменьшает магнитный поток генератора. Происходящее при этом понижение напряжения на зажимах ослабляет действие обмотки В, что вызовет более интенсивное понижение ЭДС генератора с увеличением тока. При коротком замыкании внешней (рабочей) цепи действие обмотки В практически прекращается. Обмотка С создает при этом основную МДС, не изменяющуюся при изменении нагрузки генератора и предохраняющую его от перемагничивания, что могло бы иметь место при наличии только двух обмоток — А и В. Для настройки сварочного тока служит регулятор в цепи независимого возбуждения, регулятор в цепи шунтового возбуждения позволяет установить требуемое напряжение. Ток короткого замыкания устанавливался в зависимости от силы тока в обмотке независимого возбуждения и мог быть равным, больше или даже меньше рабочего тока. Это было тем более необходимо потому, что сварку часто выполняли голыми металлическими электродами, даже без ионизирующих обмазок. Система генератора Кремера позволяла настроиться на разнообразные режимы работы в процессе дуговой сварки и наплавки и была принята за основу при разработке новых генераторов. В 1907 г. фирма «Линкольн электрик велдинг» (США), основанная за 12 лет до этого Джоном К. Линкольном для производства электродвигателей, наладила выпуск первых сварочных аппаратов переменного и постоянного токов конструкции младшего брата основателя — Джеймса Ф. Линкольна [124]. В том же году О. Кьельберг (Швеция) оборудовал два сварочных поста на шаланде. Источником питания служили генераторы постоянного тока, вырабатывающие при 1250 об/мин напряжение от 50 до 120 В. Вращение осуществлялось от паровой турбины. В 1910 г. к производству мотор-генераторов постоянного тока в США подключились мощные фирмы «Дженерал электрик» и «Вильсон велдер энд металз». Обе фирмы способствовали резкому повышению объемов применения дуговой сварки во время Первой мировой войны. Почти одновременно с разработкой специальных генераторов для сварки были созданы моторы для их вращения. Появились производственные электрические, бензиновые и керосиновые двигатели. Некоторые из них были самоходными, часть снабжали компрессорами для пневматического оборудования. Такие установки применяли для дуговой сварки в полевых условиях иеще с 1910 г. В годы Первой мировой войны в войсках Германии, Великобритании и США использовали грузовики, оборудованные сварочными генераторами. Так, фирма «Вестингаус» расположила на кузове автомобиля генератор мощностью 26 кВт, который работал от бензинового двигателя 26 л.с. со скоростью 1150 об/мин, вспомогательную аппаратуру для обработки сварных соединений и кабель длиной до 500 м. Фирма «Парсон-Мюрекс» разработала преобразователь, который содержал генератор, обеспечивавший силу тока 200 А при 30 В и работавший от керосинового двигателя. В 1923 г. на принципе намагничивающей параллельной и размагничивающей последовательной обмоток возбуждения В. П. Никитиным, К. К. Хреновым и А. Е. Алексеевым был сконструирован первый советский сварочный генератор типа СМ [125] (рис.42). 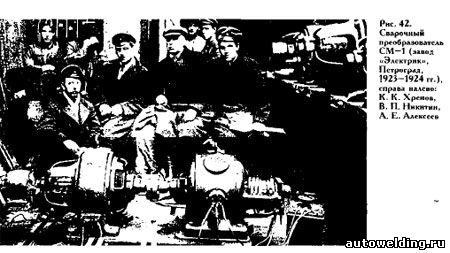
В следующем году начался серийный выпуск этих машин па заводе «Электрик» (Петроград). Источники питания продолжали совершенствоваться в КБ этого завода (А. А. Алексеев). Были разработаны генераторы нескольких типов и размеров, рассчитанные на работу в диапазонах 50—200, 100—300 и 150—600 А. В частности, был сконструирован преобразователь, где в одном корпусе размещались сварочный генератор и электродвигатель переменного (трехфазного с короткозамкнутым ротором) или постоянного тока. Когда в начале 1930 г. было принято постановление о сварочной специализации завода «Электрик», там выпускали уже более 2000 единиц сварочного оборудования. К концу 1931 г. завод занял первое место в мире по годовому объему выпуска сварочных генераторов (8000 тт.). В 1932 г. в промышленности СССР действовало 25 тыс. сварочных постов, из них более 17 тыс. с маркой завода «Электрик» [126]. В 1931 г. на этом заводе было освоено производство наиболее совершенных однопостовых генераторов типа СМГ. В 1933 г. выпущены первые многопостовые преобразователи СМГ-3 и СМГ—4, агрегаты САК—2—1 с бензиновым двигателем внутреннего сгорания. Почти одновременно с машинными преобразователями переменного тока в постоянный появились ламповые выпрямители. Они состояли из трехфазных трансформаторов, ток со вторичной обмотки которых поступал на выпрямительный блок. Такие преобразователи нашли достаточно широкое применение в европейских странах, менее заметное — в США. С 1924 г. фирма «Филипс» приступила к серийному выпуску выпрямителей, единственной вращающейся частью которых был вентилятор. Как это нередко бывает в истории техники, авторство крупных разработок оспаривали несколько фирм и изобретателен. Не стало исключением и создание первой моторно-генераторной установки. В декабре 1932 г. в журнале Американского сварочного общества было опубликовано обсуждение доклада С. А. Уилса о проектировании сварных изделий для металлургической промышленности. В статье говорилось, что эксперименты ее автора по ремонту стальных отливок относятся к тому же времени, что и появление первой моторно-генераторной установки, изготовленной в США исключительно для целей дуговой сварки. Эта установка-пионер была изготовлена в 1909 г. фирмой «Дженерал электрик». Однако в мае 1933 г. в том же журнале появилась статья Дж. Бурке, в которой он утверждал, что фирма «Си-Си электрик», приобретенная фирмой «Бурке электрик» в конце 1920-х гг., начала продажу установок мотор-генераторов для дуговой сварки еще в 1905 г. Одна из установок была куплена фирмой «Мастер стил кастинг» (Честер, штат Пенсильвания) и пущена в эксплуатацию в апреле 1905 г. [127]. Первый в мире специализированный трансформатор для стыковой контактной сварки был разработан Э. Томсоном в 1885 г. [99]. По сути, это была установка, состоящая из многовитковой первичной обмотки и одного витка вторичной обмотки сечением до 200 мм2 с закрепленными на концах зажимами в виде струбцин, стягивающихся пружинами. На следующий год Э. Томсон изготовил более мощный источник, способный дать ток до 200 000 А при напряжении 1-2 В. Системы управления подачей энергии для сварки являются важнейшей частью сварочной цепи и чаще всего составной частью источника энергии. При контактной, особенно точечной, сварке в месте соединения за короткое время выделяется значительное количество теплоты, что требует применения устройств для точного регулирования длительности поступления энергии. Первые источники тока для контактной сварки Э. Томсона не были снабжены какими-либо системами контроля процесса по времени. Трансформаторы включали и выключали вручную рубильником или кнопкой в цепи обмотки магнитного пускателя. В 1890—1900 гг. были разработаны установки для контактной сварки с встроенным генератором постоянного тока. Для сварки использовали ток низкого напряжения большой мощности. Позже появились установки с генератором переменного тока. Регулирование тока в обоих типах установок не представляло трудностей. Продолжали совершенствоваться и аппараты с питанием от трансформатора с секционированными катушками первичной обмотки, что позволило предварительно настраивать сварочное напряжение. Основные их недостатки обуславливались перегрузкой магнитной цепи, когда для работы включали небольшое количество витков катушки первичной обмотки. Чтобы свести к минимуму потери, необходимо было изготавливать источник питания с высокой точностью и использовать автотрансформатор. Размеры и конструкция вторичного витка были рассчитаны на ток большой силы. Витки охлаждались водой. С появлением более мощных трансформаторов и установок для точечной сварки начали создавать устройства для управления магнитными пускателями, которые включали или прекращали подачу энергии к установке. Эту систему управления долгое время использовали в машинах для точечной сварки с ручным или ножным управлением [128]. Для регулирования цикла сварки применяли также механические устройства — кулачки, коноиды и подобные им элементы, предназначенные для преобразования вращательного движения в запрограммированное поступательное. С этими устройствами появилась возможность сократить временные интервалы управления контактором, и они были применены в установках для точечной сварки. При разработке устройств регулирования времени было обнаружено, что идеальным механизмом контроля времени является тот, который определяет один цикл подачи энергии, т. е. при частоте 60 Гц цикл составил 1/120 с [129]. Для более точного соблюдения продолжительности сварки были внедрены «электрические хронометры», в которых конденсатор заряжали по экспоненциальному закону. Конденсаторы включали параллельно обмоткам реле (рис. 43). 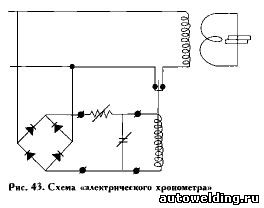
Имелись аппараты, реле которых включали во вторичную обмотку. В процессе эксплуатации оказалось, что не только электромагнитную систему сложно непрерывно регулировать. «Хронометр» также чувствителен к колебаниям напряжения в сети. Например, с увеличением напряжения сокращалась продолжительность зарядки конденсатора, а следовательно, и длительность сварки. В ряде аппаратов использовали продолжительность разрядки конденсатора. Погрешности в соблюдении требуемой длительности сварки возникали также из-за инерции контактов и механических узлов (кулачков, контакторов и др.). Такие системы управления не позволяли достигнуть достаточно точной выдержки времени, необходимой для точечной сварки тонких листов (например 0,08 с при токе 4000 А для стального листа толщиной 0,25 мм) или элементов из алюминия либо нержавеющей стали [129]. Существенно схемы управления были усовершенствованы в 1924 г., когда в схему реле включили неоновую лампу так, что через нее ток мог проходить только при определенном уровне напряжения. В 1932 г. после изобретения в США тиратрона — электронной лампы с легко ионизируемой газовой средой — на его основе были разработаны регуляторы длительности сварки. Поскольку тиратрон пропускает только полуволну, то для контроля переменного тока требовались две лампы (рис. 44, а). Управление сварочным током осуществляли через прерыватель. 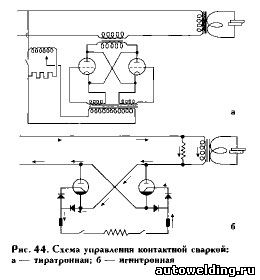
В 1934 г. в США появились новые регуляторы, основанные на игнитронах — ртутных вентилях, которые составляли так называемый холодный катод, тогда как анод обычно выполняли из графита (рис. 44, б). С помощью поджигающего электрода мгновенно возникала электронная эмиссия и, следовательно, начиналось прохождение тока. Игнитроны выдерживали большие перегрузки по току. Два игнитрона включали в схему прерывателя машин для контактной сварки. Тиратронное управление предназначалось для машин малой и средней мощности. Благодаря игнитронам были созданы машины мощностью более 8 млн. кВА. Следует отметить, что во всех электронных устройствах управления цепь возбуждения игнитронов является только конечной частью цепи. К концу 1930-х гг. были разработаны конструкции машин, цепь регулирования мощности которых включала в себя комплекс элементов, необходимых для возбуждения игнитронов и регулирования по фазе синусоидального напряжения, конденсаторы, выдающие сигналы управления интервалами сварки и паузами, многочисленные вспомогательные, усилительные, защитные, сигнальные элементы. Электротехники в разных странах мира пытались осваивать переменный ток для дуговой сварки. Его применение сулило большие преимущества, и в первую очередь упрощение источников энергии. В 1905 г. профессор В. Ф. Миткевич в работе «О вольтовой дуге» предложил Применять для сварки металлов переменный ток, в том числе и трехфазный. Еще в 1920-х гг. в США и Германии было много противников применения переменного тока для дуговой сварки. Основными аргументами были низкое качество сварного соединения и трудность поддержания горения дуги. Тем не менее, совершенствование и распространение электродов с качественным покрытием для сварки на переменном токе постепенно завоевывало все больше сторонников. К тому времени были разработаны штучные электроды с обмазкой, в состав которой входили вещества с низким потенциалом ионизации (калий, натрий, кальций и др.), что облегчало возбуждение и поддержание дугового разряда. Первые трансформаторы для дуговой сварки на переменном токе были выпущены в 1923 г. фирмой «Веко», сначала небольшой мощности, а спустя два года — на силу тока до 1000 А при напряжении 90 В. Причем такой трансформатор можно было подключать к сетям напряжением от 110 до 500 В [130]. В середине 1920-х гг. получили распространение также сварочные машины переменного тока фирм «Сименс-Шуккерт», АЭГ (Германия) и др. [131]. Применение переменного тока для дуговой сварки угольным электродом не представляло трудностей. Однако сварка плавящимся электродом стала возможной только при нанесении на металлический стержень легко ионизирующихся элементов. В 1928 г. в составе сварочного оборудования промышленно развитых стран уже было несколько моделей трех- и однофазных трансформаторов, трансформаторов с катушками индуктивности и Др. Совершенствованием сварочных машин занимались фирмы «Эллой велдинг просессиз», «Аркос», «Парсонс-Мюрекс» (США), «Инглиш электрик» (Стаффорд), «Премьер электрик велдинг» (Великобритания), «Сименс-Шуккерт» (Германия) и др. Широкое внедрение сварки в судостроение и промышленное строительство, в производство других металлоконструкций, начавшееся в конце 1920-х гг. на Западе, несмотря на экономический кризис, вызвало значительную потребность в разнообразных источниках питания — от мощных стационарных электрических машин до портативных трансформаторов. В выпуске сварочных источников значительную роль играли фирмы АЭГ, «Дженерал электрик» и созданная в 1925 г. Н. С. Миллером фирма «Миллер электрик мэнью-фекчуринг» (США). В 1929 г. Миллер разработал четырехкатушечный сварочный трансформатор, а в 1936 г. — трансформатор, переменный ток высокой частоты которого накладывался на сварочный ток, что облегчало повторное возбуждение дуги. В Европе нашел применение аналогичный трансформатор конструкции Бетено. Указанные источники переменного тока были предназначены и их успешно использовали для сварки плавящимся электродом без обмазки или с тонкой обмазкой, а также угольными электродами. К. Дж. Хольслаг (США), автор ряда стабилизирующих и шлакообразующих электродных покрытий, вводил в их составы ионизирующие компоненты. Сварка такими электродами позволила упростить конструкцию трансформатора, исключив обмотки, обеспечивающие импульсы повышенного напряжения [132]. Трансформатор имел две вторичных обмотки, первая из которых была включена параллельно цепи питания 80 В, тогда как вторая (внутренняя) — последовательно подаваемому напряжению, и она оставалась разомкнутой до тех пор, пока существовал контакт. К концу 1930-х гг. были сформулированы три принципа регулирования силы тока в сварочных трансформаторах: с несколькими выводами, с магнитным шунтом и с регулируемым воздушным зазором; каждая из схем имеет несколько отличающихся статических вольтамперных характеристик. Практика показала, что последняя из этих трех схем (рис. 45, в) имеет по сравнению с цервой (рис. 45, а) преимущество, заключающееся в возможности плавного регулирования тока, а по сравнению со второй — в более высоком напряжении холостого хода (рис. 45, б). В системе с магнитным шунтом низким значениям тока соответствует и низкое напряжение холостого хода. При таких параметрах труднее выполнять сварку электродами малых диаметров, низкая тепловая инерция которых требует высоких напряжений холостого хода. 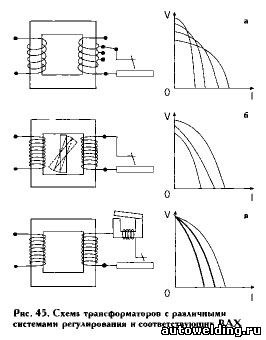
В течение 1920-х гг. были предложены различные конструктивные усовершенствования для улучшения эксплуатационных характеристик каждого из типов трансформаторов. Так, в некоторых вариантах исполнения трансформаторов удавалось обеспечить более низкие напряжения холостого хода при выключении из цепи резистора или катушки индуктивности, начиная уже с момента возбуждения дуги. Были и другие конструкции (с ненасыщенными магнитными цепями, специальными обмотками и т. п.). Трансформаторы оказались проще в управлении и дешевле в изготовлении, чем генераторы. Однако однофазное питание обусловило низкое значение коэффициента мощности этих источников. Для решения данной проблемы был предложен способ подключения конденсаторов параллельно сети. В начале 1930-х гг. в Советском Союзе появляются оригинальные сварочные трансформаторы. На заводе «Электрик» в Ленинграде было налажено производство однокорпусного трансформатора В.П.Никитина— СТН, а трансформатор СТХ конструкции К. К. Хренова изготовлялся промкооперацией. Это были трансформаторы с реактивными катушками, включенными последовательно во вторичную (рабочую) цепь. Для небольших сварочных токов В. П. Никитиным был сконструирован трансформатор с внутренним реактивным сопротивлением, представляющий собой комбинацию трансформатора и реактивной катушки (рис. 46). Перечисленные источники питания имели падающую внешнюю характеристику. В последующие годы на заводе «Электрик» освоили производство еще нескольких типов трансформаторов, в том числе СТЭ—3, СТЭ—24 и СТЭ—34 с номинальной силой тока до 450 А. 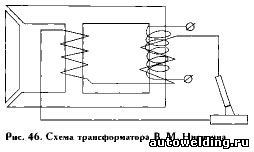
При сварке угольной дугой главным моментом являлось достижение лучшей устойчивости дуги, чувствительной к воздействию магнитных полей. Для ее стабилизации применяли принцип наложения сильного магнитного поля на дугу, воздействие которого должно превалировать над прочими побочными полями, отклоняющими дугу. В автоматах с угольной дугой этот принцип нашел свое осуществление в виде сварки по способу «электронного вихря», разработанному фирмами «Линкольн» (США) и «Елин» (Австрия). При этом угольный электрод окружается трубкой с навитым на нее спиральным проводом, по которому во время сварки проходит ток, образующий сильное магнитное поле, воздействующее на дугу. В этих аппаратах автоматически производится регулировка длины дуги и подача к месту сварки угольного электрода по мере его сгорания. Взаимное перемещение угольной головки и свариваемого изделия производится также автоматически. Работа над автоматизацией процесса дуговой сварки плавящимся электродом потребовала создания не только головок для подачи проволоки, обеспечения защитной среды и перемещения вдоль изделия, но и специальных источников питания, а также аппаратуры управления. Так, в конце 1930-х гг. на заводе «Электрик» начали выпускать дуговые сварочные автоматы с тиратронным управлением (сделанные по образцу фирмы «Дженерал электрик») [133]. Однако в принципе процесс дуговой автоматической сварки инерционен и не требует высокой точности регулирования длительности технологического цикла. Поэтому в практике нашли применение системы управления, выполняющие функции возбуждения и поддержания постоянной длины дуги, построенные на электромагнитных реле и контакторах. Основным фактором, определяющим конструкцию сварочной головки, являлся принцип регулирования длины дуги. Исходя из этого, головки разделяли на две категории: с плавной и импульсной системами регулирования. Головки, созданные в конце 1930-х гг. в Институте электросварки под руководством Е. О. Патона и нашедшие применение для сварки голой проволокой под флюсом, имели схемы плавного регулирования. Подающий механизм состоял из дифференциала с четырьмя коническими зубчатыми колесами, двигателей постоянного и переменного тока, электрической схемы управления, подающих роликов и т. д. [134]. Ролик, подающий электродную проволоку, приводят в движение от мотора М—1 постоянного тока и асинхронного двигателя М —2 трехфазного тока. При равенстве оборотов М—1 и М—2 крестовина дифференциала с сателлитами и вал ведущего ролика не вращаются. При ненасыщенной магнитной системе генератора постоянного тока ДУРГ и М—1 число оборотов М-1 находится в прямолинейной зависимости от напряжения на дуге. Изменение длины дуги и соответственно скорости подачи электродной проволоки осуществляется при помощи реостатов в цепях обмотки возбуждения ДУРГ и М-1 (рис. 47). 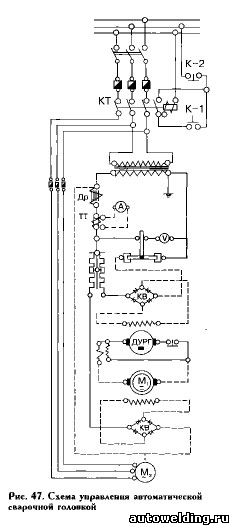
При автоматической сварке на переменном токе для устойчивого горения дуги необходимо наличие индуктивности, создающей достаточный сдвиг фаз между током и напряжением. При этом напряжение между электродом и изделием при холостом ходе должно быть по возможности меньшим, но достаточным для обеспечения устойчивого горения и надежного возбуждения дуги. Причем источники питания должны быть рассчитаны на условия работы при непрерывной загрузке. Следует отметить, что до 1940-х гг. сварочные головки, разработанные для автоматической сварки открытой дугой, снабжались довольно сложными электрическими схемами регулирования. В первые годы работы над автоматической сваркой под флюсом конструкторы продолжали стремиться к максимальному повышению чувствительности схем регулирования. В результате значительно усложнялась схема и понижалась надежность их работы. И все же при массовой однообразной работе и соответственных условиях работа автоматом являлась более успешной, чем ручная сварка. Непрерывность и постоянство режима сварки при автоматической работе обеспечивали однородность электрометалла и способствовали улучшению его качества. Отсутствие траты времени на смену электродов и перемещение изделия ускоряло процесс сварки, что уменьшало ее стоимость. Скорость сварки можно еще увеличить посредством повышения силы тока приблизительно на 30% выше нормальной при подводке тока к концу электродной проволоки.
|