Плазменная резка
Плазма — это электропроводный газ, содержащий электроны, ионы и нейтральные молекулы. При резке используют термическую плазму с температурами (5÷30) * 103 К, получаемую в результате продувания текучей плазмообразующей среды (обычно — газа, реже — жидкости, а также газожидкостных смесей) через электрический дуговой разряд в устройстве, называемом дуговым плазмотроном. В столбе дугового разряда плазма образует пространственную область, содержащую газообразный проводник между электродами с плотностью энергии до 1 * 106 Вт/см2, а за его пределами — высокоэнтальпийный факел. Эта формируемая в виде сжатой цилиндрической струи и надлежащим образом ориентированная пространственная область может служить концентрированным высокотемпературным теплообменным источником тепловой энергии. Истечение плазменной струи характеризуется скоростями, достигающими скорость звука. Радиальное распределение температуры и скорости в струе аппроксимируется кривыми Гаусса. Плазменная резка состоит в непрерывном проплавлении материала заготовки струей плазмы электрической дуги, перемещаемой по заданной линии, при сопутствующем удалении ею расплава с образованием полости реза. С этой целью режущую струю размещают в исходной позиции у кромки обрабатываемого металла и по мере его проплавления перемещают по намеченной линии. Однако в процессе резки плазменной струей используется лишь около 7 % энергии плазмогенерирующей дуги, что ограничивает его рациональность преимущественно обработкой неметаллических материалов. Для резки металлов (электропроводных материалов) используют не только плазменный факел и столб дуги, но прежде всего активно передающее энергию заряженных частиц пятно (обычно анодное) плазмогенерирующей дуги постоянного тока, которую принято называть режущей плазменной дугой. Такой способ плазменной (точнее — плазменнодуговой) резки дает возможность существенно (до 20—30 % и более) повысить использование энергии дугового разряда. Применяя металлическую подложку в качестве вспомогательного анода, возможно использовать для резки неметаллических материалов столб плазменной дуги. Столб дуги и струя плазмы имеют нужный для разделительной резки характер линейного источника тепла. Активное пятно дуги под действием потока плазмы вместе с радиальным участком столба перемещается от верхних кромок реза к нижним. Затем у верхних кромок происходит шунтирование радиального участка, нижнее пятно отмирает и процесс многократно повторяется, что придает теплопередаче квазилинейный характер. 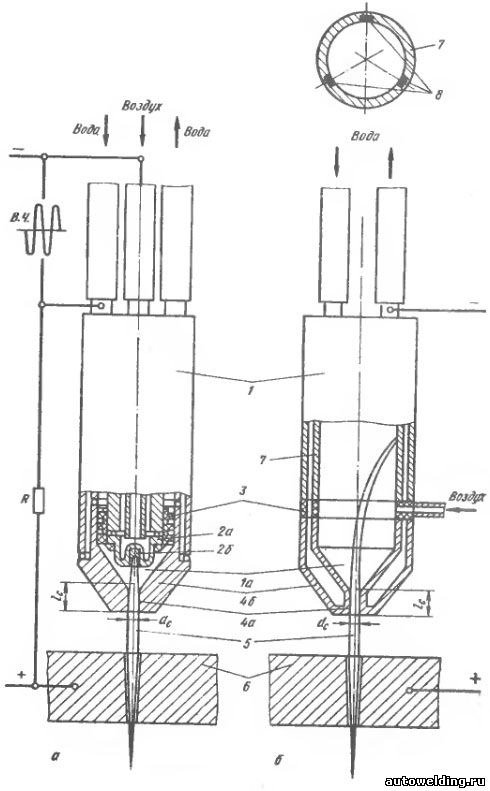
Рис. 27.1. Схемы резательных плазмотронов: а — с гильзовым катодом; б — с полым медным электродом; 1 — плазмотрон (1а — дуговая камера); 2 — гильзовый катод (2а — гильза; 2б — катодная вставка); 3 — завихритель; 4 — формирующее сопло (4а — канал сопла, 4б - корпус сопла, dc — диаметр сопла, lc — длина сопла); 5 - режущая плазменная дуга; 6 — разрезаемый металл; 7 — полый электрод; 8 — термоэмиссионные вставки; R — балластное сопротивление для питания вспомогательной дуги при зажигании режущего разряда; В. Ч.— высокое напряжение высокой частоты для первоначального пробоя дугового промежутка при зажигании дуги Плазмотрон (рис. 27.1) имеет дуговую камеру, содержащую электродный элемент для формирования катодной области режущего разряда и электрически изолированное от него сопловое устройство. В дуговую камеру подается рабочая среда, преобразуемая в плазму, вытекающую из сопла в виде цилиндрической струи. Анодом плазмогенерирующей дуги служит, как правило, разрезаемый металл (при плазменнодуговой резке) или корпус сопла (при резке струей плазмы). Корпус сопла используют в качестве анода также в начальной пусковой фазе. Поджиг дуги осуществляют наложением на дуговой промежуток напряжения источника тока, а также высокого напряжения тока высокой частоты, осуществляющего искровой пробой. Катод плазмотрона изготовляют из тугоплавких металлов с высокими эмиссионными характеристиками. Для работы в нейтральных плазмообразующих средах используют вольфрам. В окислительных средах применяют катоды из циркония или гафния (табл. 27.1), образующих при работе дуги защитную пленку тугоплавких оксидов и нитридов (пленочные термохимические катоды). В плазмотронах для машинной резки наиболее часто используют гильзовую конструкцию катодов (рис. 27.1, а), состоящую из медного катододержателя с катодной вставкой из вольфрама, графиня или циркония. Как правило, катододержатель интенсивно охлаждают проточной водой. Рабочий торец пленочных катодов — плоский. Катодное пятно дуги стабилизируется в центре катодной вставки вихревым потоком плаэмообразующего газа, для чего плазмотрон снабжают завихрителем. Вольфрамовые
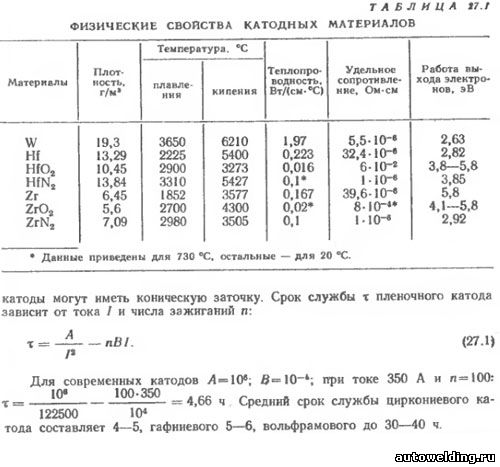
Малый срок службы пленочных катодов является их основным недостатком. Отечественными разработчиками предложены машинные плазмотроны с рабочим электродом (рис. 27.1, б) в виде полого медного цилиндра, по внутренней поверхности которого под действием газового вихря быстро перемещается активное пятно. Заметного расплавления меди электрода при этом не наблюдается, ее эрозия характеризуется малыми значениями от 10-6 до 10-7 г/К, и он сохраняет свою работоспособность в пределах 3— 6 смен. В плазмотронах с полым электродом при определенной гидродинамике течения рабочего газа приэлектродная зона разряда может самопроизвольно делиться на несколько самостоятельных приэлектродных участков. Для стационарного расщепления разряда в тело медного электрода заделывают термоэмиссионные вставки. Такой перспективный плазмотрон позволяет в несколько раз увеличить рабочий ток или повысить срок службы рабочих электродов. В плазмообразующих углеводородных смесях с углекислым газом перспективны графитовые самовозобновляющиеся высаживанием ионов углерода из плазмы катоды, ресурс которых составляет более 100 ч. Формирующее сопло обеспечивает ограничение диаметра столба дуги, введение в него рабочей среды с целью максимального преобразования ее в плазму и формирование скоростной цилиндрической плазменной струи, которая может быть использована для стабилизации дугового разряда на протяженном участке вне плазмотрона. Корпус сопла из теплопроводной меди интенсивно охлаждают и электрически изолируют от столба режущей дуги во избежание появления в металле параллельных токоведущих каналов и разрушения сопла активными пятнами возникающей при этом «двойной дуги» на участках «катод — сопло» и «сопло — разрезаемый металл» интенсивным вихревым потоком плазмообразующей среды. Срок службы сопел зависит от величины рабочего тока, диаметра и длины сопла, и толщины его стенки, расхода и состава плазмообразующей среды, интенсивности охлаждения и других факторов и может составлять несколько смен. Геометрические размеры сопла — его диаметр и длина (рис. 27.1) определяют качество поверхности и точность вырезанных заготовок, а также надежность работы плазмотрона. Рациональные соотношения диаметра и длины сопла в соответствии с величиной рабочего тока, установлены на основе сочетания этих требований (табл. 27.2). 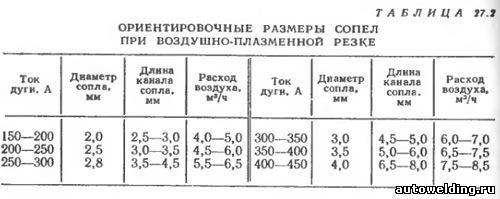
В Германии были созданы и получили распространение в европейских и других странах так называемые тонкоструйные резательные плазмотроны, рассчитанные на резку дугами с токами величиной до 100—160 А, формируемыми в соплах диаметром до 1,5 мм при подаче плазмообразующей аргоно-водородной смеси под повышенным давлением. Такие плазмотроны используют для резки цветных металлов или высоколегированных сталей в диапазоне толщин до 20—30 мм. Их преимущества состоят в получении узких разрезов повышенного качества. При резке цветных металлов улучшается использование потребляемой энергии. Резка сталей более целесообразна в кислородсодержащих смесях. Для микроплазменной резки (металлов толщиной <10 мм) используют (преимущественно в зарубежной технике) плазмотроны для токов 10— 100 А с еще меньшими диаметрами сопл. МатериалыРабочие плазмообразующие среды должны обеспечивать: - эффективное формирование режущей дуги
- получение высококачественных кромок реза
- эффективную передачу разрезаемому металлу тепловой энергии, заимствованной в столбе дуги
- длительную работу формирующих элементов плазмотрона
- получение дополнительной энергии для резки за счет экзотермических реакций
- экономичность и безопасность работы.
Рабочие среды наиболее широко используются в виде технических газов: азота, аргона, водорода, кислорода, сжатого воздуха и др. Рабочую среду выбирают с учетом ее свойств (табл. 27.3) и свойств обрабатываемого материала. Инертные газы обеспечивают получение наиболее чистых поверхностей реза, что особенно важно для резки цветных металлов. Двухатомные газы улучшают передачу энергии дуги разрезаемому металлу за счет механизма диссоциации — рекомбинации. Кислородсодержащие среды повышают энергетическую эффективность резки металлов, экзотермически реагирующих с кислородом, что обеспечивает для них наиболее высокую производительность резки. 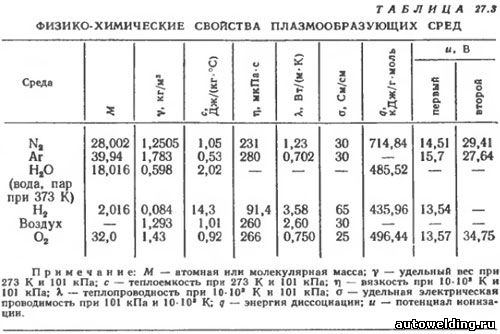
Наибольшее применение в СССР получила резка на основе использования плазмы кислородсодержащего сжатого воздуха (воздушно-плазменная резка). Области рационального использования сред указаны в табл. 27.4. 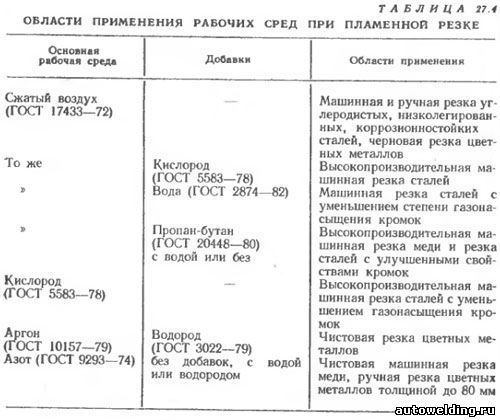
Перспективно использование интенсифицирующих плазмообразующих сред. При воздушно-плазменной резке обогащение воздуха кислородом обеспечивает повышение производительности резки сталей без увеличения затрат энергии и способствует улучшению качества металла на кромках. Подача воды в плазменную дугу также улучшает качество заготовок из сталей и способствует повышению скорости резки. Если к плазмообразующему воздуху добавлять углеводороды, заметно возрастает скорость резки меди и ее сплавов. и существенно улучшается качество заготовок. См. также:
|