«Электрическая ковка». Стыковая сварка
Первым из всех видов электрической энергии в тепловую — нагрев проводника протекающим током — был открыт в 1801 г, Л. Тенаром. Нагрев и плавку металлов электрическим током в 1802 г. исследовал В. В. Петров [56]. А в 1807 г. Г. Дэви сконструировал первые лабораторные электропечи сопротивления с прямым и косвенным нагревом для исследования свойств металлов [96]. Закон теплового действия тока, устанавливающий зависимость количества выделенной теплоты от параметров проходящего тока, открыли в 1842 г. независимо друг от друга Д. П. Джоуль и Э. X. Ленц. Джоуль и почти одновременно с ним У Томсон во время своих исследований электричества сплавляли пучки проводов в коробке с углем, пропуская по проводам электрический ток, т. е. в принципе осуществляли сварку сопротивлением. Впервые внедрили этот вид электронагрева в 1875 г. Вильгельм и Александр Сименсы. На их заводах концы телеграфных проводов со специально выполненным косым срезом торцов собирали внапуск и соединяли путем «накала» проходящим постоянным током прямо в линии для намотки. Однако эти и другие ранние технологии «не прижились», и в последующие годы их никто далее не разрабатывал. Проблема соединения проводов оставалась актуальной: пайка не обеспечивала равномерной электропроводности и равнопрочности проводов, поэтому на стыках оставляли усиление (увеличенный диаметр), а это мешало изготовлению кабелей, генераторов и др. Проблема была решена с помощью новой технологии — стыковой контактной сварки. В ее основу было положено явление, открытое профессором Элихью Томсоном. Во время лекции во Франклиновском технологическом институте в феврале 1877 г. он демонстрировал зарядку конденсатора (лейденской банки) от искровой катушки. У него вдруг возникла идеи проверить, что получится, если заряд пойдет обратно при разряде конденсатора на катушку. Профессору показалось, что результат опыта будет интересен не только ему, но и аудитории. В приборе его собственной конструкции вторичная обмотка катушки была сделана из тонкой проволоки, а первичная — из толстой. Томсон соединил между собой концы толстого провода, а вторичную тонкую обмотку подключил к источнику тока. Разряд через тонкую обмотку вызвал ток большой силы в первичной обмотке, и скрученные концы толстой проволоки сплавились в месте соединения. Именно там было наибольшее сопротивление и выделилось наибольшее количество теплоты. Так впервые в мире была осуществлена контактная стыковая сварка. Но к разработке своей новой идеи Томсон приступил лишь через несколько лет, поскольку в конце 1870-х гг. он, кроме преподавания, занимался еще и конструированием дуговых ламп, а также источников питания для них [97]. В 1880 г. Э. Томсон оставил преподавательскую деятельность и поступил в качестве инженера-электрика в фирму «Америкэн электрик компани», а через два года он и Э. Дж. Хьюстон для эксплуатации изобретенной ими системы дугового освещения, получившей название «системы Томсона-Хьюстона», организовали собственную фирму «Томсон-Хьюстон электрик компани». Фирма быстро росла, и в 1892 г. здесь работало уже около 4000 человек. За эти годы сфера деятельности компании значительно расширилась. Кроме оборудования для дугового освещения, она стала производить электрические двигатели, трансформаторы, распределительное оборудование, а также оборудование для городских электрических железных дорог (трамвайных линий) [97]. Процветанию фирмы способствовал изобретательский ум Э. Томсона. В короткое время Э. Томсон разрабатывает новые типы дуговых ламп, коммутирующую аппаратуру, динамомашину для генерирования переменного тока, подаваемого на трансформатор большой удельной мощности, и наконец, специальные токоподводящие зажимы. Таким образом, к 1884 г. Э. Томсоном были созданы необходимые для контактной (стыковой) сварки элементы оборудования. В 1885 г. он отрабатывает технику сварки, доводит до безотказной работы сварочную аппаратуру и в начале 1886 г. подает заявку на патент, защищающий принципиально новый способ электрической сварки [98, 99]. Способ Томсона описывался так: «Свариваемые предметы приводятся в соприкосновение местами, которые должны быть сварены, И через них пропускается ток громадной силы (до 200 000 А) при низком напряжении (1—2 В). Место соприкосновения предоставит току наибольшее сопротивление и потому сильно нагреется. Если в этот момент начать сжимать свариваемые части и проковывать место сварки, то после охлаждения предметы окажутся хорошо сваренными». На способ был выдан патент США № 347140 от 10 августа 1886 г. (рис. 25). 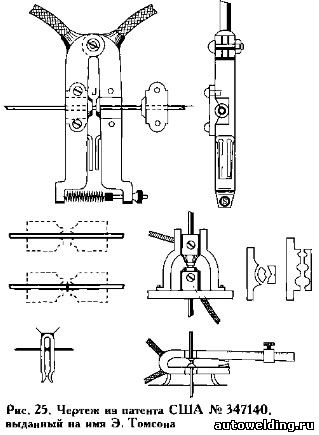
Проковка была не просто данью моде, остатком прежней технологии (кузнечной сварки и клепки), а явилась приемом, обеспечивающим повышение качества металла шва. Как известно, этот прием не отвергался и Н. Н. Бенардосом. Поскольку кроме нагрева применяли и механическое сдавливание, сходное с приложением силы при кузнечной сварке, первоначально способ называли «электрической ковкой» или «безогненным методом сварки». Первое устройство, выполняющее нагрев и сжатие двух проводов, состояло из двух рычагов, на одном конце соединенных шарниром из изоляционного материала, а с другого конца связанных пружиной через изоляционные втулки [100] (рис. 26). 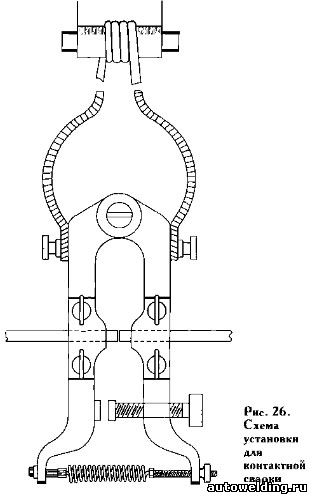
В этих рычагах посередине зажимают свариваемые детали — провода, втулки, стержни, соприкасающиеся благодаря сжимающейся пружине. Ток, проходящий по деталям, нагревает место стыка до пластического состояния, и под действием пружины металл сминается. Степень смятия устанавливают стопорным винтом. В следующей установке был использован трансформатор с замкнутым контуром (рис. 27). 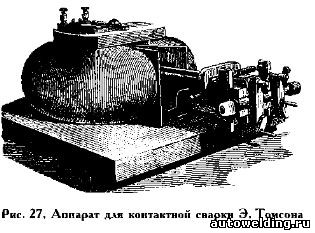
На его первичную обмотку подавалось напряжение 600 В, и по ней протекал ток силой 20 А. Эта обмотку наматывали на катушку диаметром 305 мм. Катушку охватывал и виток вторичной обмотки (по сути, кольцевой проводник), концы которой подключали через зажимы к свариваемым деталям. По сварочной цепи протекал ток 12 000 А при напряжении 1 В [65, 101]. Установка Томсона с разомкнутым магнитным контуром трансформатора состояла из первичной обмотки, расположенной на цилиндрическом сердечнике из стальных прутов длиной 30 см, и восьми витков вторичной обмотки из многожильного медного кабеля, навитых по спирали на первичную обмотку. Концы вторичной обмотки соединяли соответственно с подвижным и неподвижным зажимами (губками). Подвижную губку посредством кулачка вручную перемещали в осевом направлении [101]. В 1885 г. Э. Томсон сконструировал динамомашину с самовозбуждением (мощность 18,3 кВт, 1800 об/мин, масса 22,5 кг), которая обеспечивала сварочный трансформатор переменным током, имела высокую удельную мощность и работала с интервалами на подготовку к сварке. В последующие годы Томсон создает еще несколько типов генераторов, в том числе генератор с тремя обмотками, сварочный генератор для дуговой сварки по способу Бенардоса, генераторы переменного тока, питавшиеся непосредственно от электродвигателя. В 1887 г. в Париже изобретатель демонстрирует контактную сварку прутков диаметром 12 мм при токе 20 000 А, что превышало ток, применявшийся до этого в каких-либо других технологиях. Прочность соединения стальных стержней составляла 97 /о прочности основного металла [102]. Необходимо отметить, что поскольку одной из двух важнейших функций машин для контактной сварки является сжатие, в основу их конструирования были положены такие науки как механика, гидравлика, гидромеханика. Механические и гидравлические системы широко применяли еще в древних цивилизациях (китайской, вавилонской, египетской, греческой и т. д.). В древнем Риме и в странах Халифата в период многовекового расцвета арабской культуры были открыты законы и заложены фундаменты многих наук, становление которых завершилось в основном в эпоху Возрождения, в период зарождения индустриального производства и строительства мощного кузнечно-прессового оборудования. Э. Томсон обладал глубокими познаниями в механике (полученными еще в институте) и в электротехнике (в развитии которой он активно участвовал сам) и эффективно использовал их при разработке контактной сварки. В 1889 г. он сконструировал установку, в которой ток прерывался синхронно с прикладываемым усилием сжатия. Происходило это при смещении тяги и подвижного зажима под действием пружины, закрепленной на неподвижном зажиме и тяге (рис. 28). 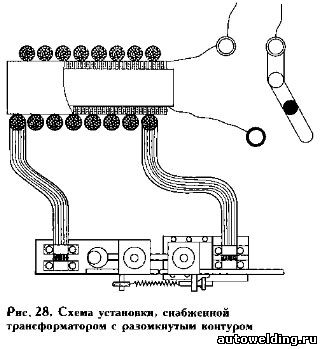
В процессе сварки торец колодки контактировал со стопором выключателя. Для развития больших усилий изобретатель разработал аппарат с гидравлической системой. При повороте рычага в ту или другую сторону прерывалась электрическая цепь трансформатора, а на поршень оказывалось давление, передаваемое на подвижный зажим с привариваемой деталью [86]. Следующим шагом в развитии стыковой контактной сварки было применение импульсов тока и давления. В механическую систему сварочной машины Томсон вводит шестерню с храповиком. Рычаг, приводящий в действие подвижный зажим, соединяли с сердечником, который вводили в соленоид, включенный в первичный контур, изменяя его индуктивное сопротивление и вызывая пульсацию тока. Томсону удалось предотвратить быстро нарастающие большие токовые нагрузки при отключении тока в первичном контуре путем подключения в тот же контур параллельно пары электродов-разрядников и последовательно — плавкого предохранителя. Для этой же цели служила и катушка индуктивности. Правда, некоторые из аппаратов снабжались молотом для проковки стыка сразу после сварки или роликами для прокатки. Томсон создает специализированные машины для сварки лент и прутков в процессе прокатки, для сварки звеньев цепей, велосипедных колес и др. (рис. 29). 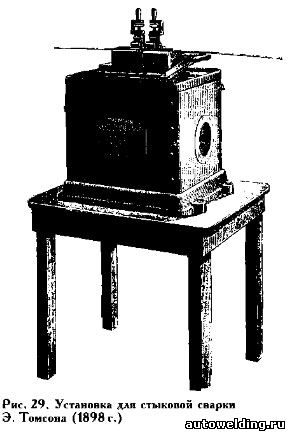
Для повышения КПД процесса изобретатель предлагает на первичную обмотку дополнительно навивать вторичную, а вторичный контур изготавливать из медной трубки прямоугольного сечения и прокачивать для охлаждения маслом. Растет номенклатура свариваемых соединений; кроме устройств для стыковой сварки двух соосных деталей, Томсон разрабатывает узлы машин для соединений деталей под углом. В начале 1890-х гг. была разработана технология стыковой сварки не только железа и стали, но и алюминия, свинца, цинка и олова. Была отработана и конструкция типовой установки, состоявшей из источников питания, узла сжатия, узла зажима деталей и подвода тока, а также элементов охлаждения. Питание осуществляли от генераторов переменного тока мощностью 5-40 кВт, через трансформатор от первичной обмотки. В установках были предусмотрены щиты управления системой отвода масла, реостаты и генераторы постоянного тока (до 40 А, напряжением 110 В), приводимые в действие генераторами переменного тока. В конце 1892 г. Томсон организовал собственную фирму «Томсон электрик вэлдинг компани», которая развернула серийный выпуск машин для стыковой сварки различной мощности (рис. 30). 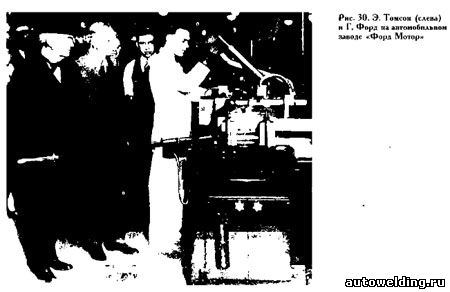
Наиболее мощные из них применяли для сварки труб. «Легкие» сварочные аппараты использовали для сварки проволок и кабелей. При помощи стыковой сварки изготавливали режущий инструмент, валы, детали велосипедов, болты и прочее, часто из сплавов разных марок [98]. Фирма «Джонсон Компани» из Джонстауна (штат Пенсильвания) приобрела патенты Томсона и начала выпускать машины для сварки рельсов. Первые четыре машины мощностью 40 кВт и две мощностью 80 кВт были приобретены в 1894 г. для строительства 65 км сплошного железнодорожного полотна в разных регионах США. Мощный трансформатор, генератор, паровую машину и гидравлическую систему располагали в специальном вагоне, к которому на стрелах подвешивали соединенные гибкой шиной сварочные головки, действующие наподобие клещей. Соединяемые концы рельсов тщательно зачищали, и рельсы сдвигали вплотную. В месте стыка перпендикулярно к оси рельсов приваривали «стыковые планки», примыкающие к подошве и к нижней части шейки. Планки попарно зажимали с двух сторон клещами, ток пропускали через стыкуемый участок до тех пор, пока металл не нагревался до белого каления. Затем включали гидравлическую систему, сжимающую клещи до тех пор, пока смятый металл планок не образовывал швов вокруг стыка и между торцами рельсов [103]. Наибольшее применение сварка рельсов нашла при прокладке трамвайных путей. К 1910 г. способ Томсона использовали и в ряде стран Западной Европы (рис. 31). 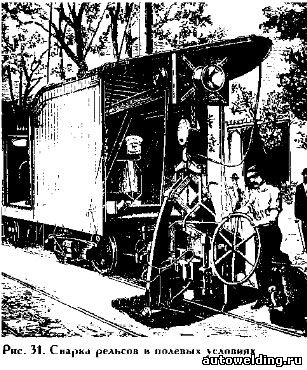
Стыковая сварка нашла эффективное применение в производстве снарядов. Большой экономии достигали за счет изготовления основной части снаряда из обычных сталей с приваркой наконечника из легированной стали. Для этого производства были разработаны специальные [86]. По мере расширения сферы применения стыковой сварки, а также в связи с совершенствованием электрической и механическом частей машин увеличивался и интерес к самому процессу сварки. В частности, отмечалось, что при разработке технологии сварки необходимо учитывать особенности нагрева: первоначально нагреваются маленькие участки в точках соприкосновения, но при этом здесь увеличивается сопротивление, и ток начинает идти по другим, менее сжатым, но холодным участкам, тем самым быстро выравнивая температуру нагрева всего участка. Томсон, Коффин, Дьюи, Лемп, Раис и другие энтузиасты контактной сварки проводили оригинальные исследования, совершенствуя технологию стыковой сварки и разрабатывая новые схемы нагрева. Были предложены несколько способов комбинированной (дуговой и контактной) сварки. Ч. А. Коффин разработал технологию сварки с промежуточной угольной пластиной-электродом, подключаемой к вторичной обмотке и вставляемой на время разогрева между стыкуемыми деталями. В других устройствах между свариваемыми деталями помещали металлическую пластину, а ток подводили к концам деталей через угольные контакты. Пластину выбирали из материала с проводимостью худшей, чем у свариваемого металла, благодаря чему ускорялся нагрев. Перед сжатием вставку удаляли. Предлагался также предварительный подогрев стыка газовым пламенем. Коффин предложил также пропускать магнитное поле через свариваемый участок, считая, что это вызовет структурные изменения, приводящие к уменьшению проводимости, а следовательно, к ускорению нагрева. Были и другие предложения, большинство из которых оказались малоэффективными и сложными. Принцип контактной сварки — нагрев проходящим током и последующее сжатие (или проковка) — использовал в «кузнечном горне для ювелиров» Э. Раис (1892 г.). Он предложил пластины, к которым нужно было приваривать орнамент из проволоки, помещать на металлическую плиту, подводя к ней ток от вторичной обмотки сварочной машины. Плиту закрывали экраном. Сотрудник Томсона Г. Лемп в 1892 г. разработал машину с новой системой подвижных зажимов с двойным набором роликов (это сократило длительность сборки и снятия изделия), а также машину со схемой соединения нескольких трансформаторов, что увеличивало мощность и КПД. К концу 1890-Х гг. наибольшее применение нашли машины мощностью 15—60 кВт. Работали они на переменном токе, который вырабатывали специальные генераторы. Так как в заводских распределительных сетях, как правило, проходил постоянный ток. Для машин мощностью 100 кВт, применявшихся для сварки задних мостов автомобилей и других крупных изделий, на заводах устанавливали автономные приводы генераторов (от паровых машин и дизелей). Проблема централизованного питания несколько сдерживала применение контактной сварки, хотя уже в первом десятилетии XX в. изобретения Томсона и его американских последователей были широко известны в Европе, их совершенствовали и применяли в Великобритании и Германии. Большое распространение контактная сварка получила в 1920-х гг. с переходом заводских сетей на переменный ток при крупносерийном производстве автомобилей, бытовой техники, сельскохозяйственного инвентаря, и продолжала совершенствоваться. Сварка с предварительным оплавлением деталей нашла широкое применение при изготовлении и ремонте деталей автомобилей, самолетов и железнодорожного транспорта (коленчатых валов, втулок и ободьев колес, кронштейнов, шасси, поршней), а также инструментов (рис. 32). 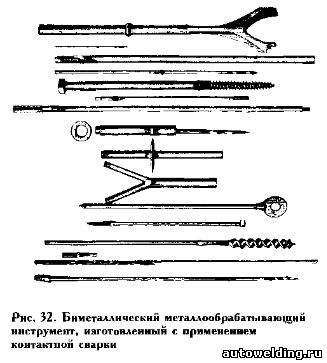
Она была принята в металлургических цехах как вспомогательная операция в непрерывном цикле прокатки прутков и полос. Несмотря на то, что еще в 1892 г. Коффин применял сварку стержней большого сечения с предварительным нагревом вибрирующей короткой дугой, только в 1913 г. Клайншмидт из фирмы «Лорен стал компани» ввел в широкое употребление «искровой метод», получивший впоследствии название стыковой сварки непрерывным оплавлением. Он увеличил напряжение питания на головках сварочных машин Томсона, что обеспечило возникновение периодических дуговых и искровых разрядов между стыкуемыми поверхностями при непрерывном сближении и оплавлении последних. Проблеме производительности сварочных машин особое внимание уделялось в период Первой мировой войны. Тогда многими фирмами в США и Европе были улучшены стыковые машины, разработана оптимальная технология процесса [104-106]. К 1930 г. были разработаны, в частности, фирмами «Ля судур электрик» (Франция) и «Дженерал электрик», специальные машины для сварки оплавлением, обеспечивающие контроль времени выполнения технологического процесса с высокой точностью. Машина мощностью 1500 кВ А при токе 100 000 А и усилии сжатия 2500 кН, рассчитанная на сварку встык изделий сечением до 25 000 мм2, автоматически воспроизводила весь цикл сварки в течение всего времени, пока была нажата педаль. При этом оплавляют поверхность частей до того, пока все поперечное сечение равномерно не нагреется, и тогда производится стягивание стыка ударом при одновременном включении первичного тока. Существенной частью машины для сварки плавлением таким образом является устройство для стягивания стыка. Механическое устройство этой машины в остальном одинаково с механическим устройством простой машины для сварки встык. Машины для сварки оплавлением применяли для сварки больших поперечных сечений, для труб и высокосортных сталей. В 1902 г. Э. Томсон разработал прямошовный способ изготовления труб с помощью стыковой сварки. В то же время в США фирма «А. О. Смит» наладила производство труб с толщиной стенки 5 мм и диаметром 500 мм, которые сваривали по всей длине (12 м) способом оплавления на машинах мощностью 5000 кВА. Было немало и других разработок, отличавшихся по виду тока, применяемым вспомогательным материалам и т. д. (патенты Фуку, Зоннихсена, Сиаки, Спалдинга, Харматы, Ритцеля, Малагути, Джонстона, Бухера и др.). К концу 1930-х гг. технология сварки рельсов определилась по-своему в разных странах. В США в основном был принят способ сварки рельсов непрерывным оплавлением. В странах Европы рельсы сваривали оплавлением с прерывистым подогревом, в процессе которого происходит чередование искрообразования и плотногоконтакта, достигаемого сближением и раздвижением свариваемых частей, постоянно находящихся под напряжением. Способ сварки, отличающийся от различных приемов стыковой сварки труб рядом существенных признаков, предложили швейцарцы А. и Ю. Вайбели в 1938 г. [107]: ток подводился к свариваемым кромкам с помощью угольных электродов, непосредственно соединенных с трансформатором через держатель. Данный способ оказался экономичным и пригодным для сварки почти всех металлов толщиной до 2—3 мм как с присадкой, так и без нее. Например, сварку алюминиевых трубок из листов толщиной 0,2—2 мм выполняли с отбортовкой при силе тока 200—500 А, напряжении 4—9 В и скорости 0,5-1,3 м/мин. В начале 1930-х гг. к совершенствованию стыковой сварки подключаются советские ученые и инженеры из Ленинграда, Москвы, Харькова, Нижнего Новгорода, изучившие и освоившие купленное в США и Германии оборудование для строящихся автомобильных и тракторных заводов, а также для реконструируемых предприятий. В 1933 г. ленинградским заводом «Электрик» были выпущены четыре марки машин для контактной сварки различной мощности; при этом мощность машины АСА—3 достигала 6 кВА, а машины АС—75 при непрерывной работе — 75 кВА, при прерывистой работе — 120 кВА (сечение свариваемого железа при открытом контуре 1800 мм2, латуни — 600 мм2) [108, 109]. Машины для стыковой контактной сварки и специальные машины с подобными схемами применяли не только для целей сварки, но и просто для нагревания деталей для закалки, куэнечно-прессовой обработки и для нагревания заклепок. Именно за таким оборудованием сохранилось название «Электрические горны». Одна из таких машин — большая «тройная» эаклепочно-нагревательная установка — была разработана в Германии. Заклепки между нагревательными электродами вводили при помощи ножного рычага. Заклепку можно было нагревать как угодно, если нужно, можно было нагреть одну головку, один стержень или же головку и стержень вместе. Во всякое время нагревание можно было прекратить и снова возобновить. «Электрические горны» экономили уголь и материал и обеспечивали использование теплоты в 90% против 10% использования в угольном или газовом кузнечном горне.
|