Изменение деформаций и напряжений в околошовной зоне при сварке сталей и сплавов титана
Возникновение собственных сварочных деформаций и напряжений обусловлено неравномерным распределением температуры при сварке, фазовыми превращениями, протекающими с изменением удельного объема, и жесткостью свариваемых элементов, препятствующей развитию деформаций. В отличие от тепловых процессов, процессы изменения полей внутренних деформаций и напряжений первого рода при сварке изучены в меньшей степени, и расчеты их, как правило, весьма сложны. В настоящее время инженерные расчеты, разработанные в СССР В. П. Вологдиным, Н. О. Окербломом, Г. А. Николаевым, Н. Н. Рыкалиным, используются главным образом для определения конечных деформаций формоизменения и остаточных напряжений. Наиболее достоверные данные о кинетике изменения внутренних деформаций и напряжений в процессе сварки получены путем экспериментальных исследований на сталях с применением разработанного Н. Н. Прохоровым дифференциального метода определения деформации. По этому методу внутренняя деформация металла е в определенной зоне сварного соединения находится как разность между изменением размеров eф (формоизменением) в этой зоне при сварке на установленной базе измерения и свободной температурной деформацией eсв, определяемой дилатометрическим путем с помощью равномерно нагретого образца. Поскольку при сварке температура в зоне термического влияния распределена неравномерно (как в продольном, так и особенно в поперечном шву направлении), постольку даже дифференциальный метод является приближенным. Однако точность этого метода тем выше, чем меньше база измерения. Измерение Н. Н. Прохоровым продольных деформаций в околошовной зоне с помощью механических тензометров на базе 20 мм в условиях наплавки валика на кромку пластины показало, что в сплавах, не претерпевающих фазовых превращений (сталь ОХ18Н9Т), при нагреве происходит развитие упругопластических внутренних сжимающих деформаций и напряжений. При достижении Tmax цикла они меняют знак, и при последующем охлаждении в околошовной зоне монотонно возрастают растягивающие деформации и напряжения (рис. 12, а). 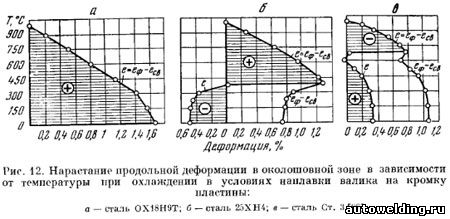
В табл. 4 приведены данные о деформациях и напряжениях в околошовной зоне, полученные при следующих условиях: размеры пластины 300x100x8 мм, наплавка на кромку длиной 200 мм электродами из малоуглеродистой стали; погонная энергия дуги q/v=3,3—4,2 ккал/см; скорость охлаждения при 550° около 6—8 град/сек; напряжения были измерены на модели в виде тонкостенных трубчатых образцов, нагреваемых током и воспринимающих сжимающие напряжения, которые создавались активными силами и имитировали реакцию соседних с околошовной, зоной участков металлов; для сталей Ст.3, 40Х и 25ХН4 остаточные напряжения были дополнительно проверены методом разрезания на пластинах с наплавленными на кромку валиками. 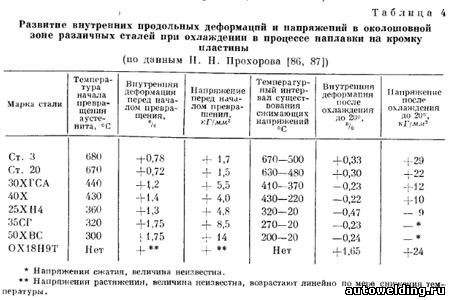
К моменту полного выравнивания температурного поля внутренняя деформация растяжения достигает 1,65%, а остаточное растягивающее напряжение, уравновешивающее упругую составляющую деформации, около 24 кг/мм2. В сталях марок 3 и 20 превращение перлита и феррита в аустенит при нагреве, протекающее с уменьшением объема, приводит к снижению сжимающих деформаций и напряжений, а обратное превращение аустенита в феррит и перлит при охлаждении, протекающее с увеличением объема, — к снижению растягивающих деформаций и напряжений. В процессе охлаждения деформация и напряжение дважды меняют свой знак: примерно при температурах начала и конца распада аустенита. При этом каждый раз пластическая составляющая внутренней деформации исчезает. В процессе распада аустенита развиваются сжимающие деформации и напряжения небольшой величины. По мере последующего охлаждения растягивающие деформации и напряжения вновь нарастают и при комнатной температуре достигают соответственно 0,3—0,33% и 29—22 кГ/мм2 (см. рис. 12, и табл. 4). В легированных сталях (например, 25ХН4), претерпевающих бейнитное и особенно мартенситное превращения, влияние этих фазовых превращений на кинетику развития деформаций и напряжений оказывается более существенным (см. рис. 12, б и табл. 4). Величина растягивающих деформаций перед началом превращения аустенита определяется коэффициентом линейного расширения стали и температурой начала превращения. Чем ниже эта температура, тем больше величина растягивающих деформаций к началу превращения. В зависимости от состава стали деформация растяжения может достигать 0,7— 1,8%. Например, в сталях Ст.3 и Ст.20 к началу превращений аустенита в феррит и перлит (680—670°) деформация равна 0,78—0,72%; в сталях 30ХГСА и 40Х к началу бейнитного превращения (440—430°) она составляет 1,2—1,4%; в сталях 25НХ4, 35СГ и 50ХВС к началу мартенситного превращения (300—300°) деформация равна 1,3—1,75%: При анализе этих данных следует иметь в виду, что наплавку производили электродами из малоуглеродистой стали, вследствие чего превращение аустенита в наплавленном металле во всех случаях протекало при относительно высоких температурах ( ∼ 600°) с образованием феррито-перлитной структуры. Поэтому при наплавке на легированные стали, в околошовной зоне которых аустенит сохранялся до более низких температур, чем в шве, деформация растяжения аустенита в зоне возрастала также и вследствие дополнительного влияния увеличения удельного объема шва при превращении и разницы в коэффициентах теплового расширения шва и зоны при последующем охлаждении. Отсюда следует, что влияние состава металла шва на деформацию аустенита в околошовной зоне закаливающихся сталей будет тем значительнее, чем больше разница в температурах превращения аустенита в этих зонах сварного соединения. Таким образом, перед началом превращения аустенит подвергается небольшой по величине внутренней деформации растяжения, продольная составляющая которой равна 0,7—1,8%. Эта деформация тем больше,чем ниже температура начала превращения аустенита в околошовной зоне и чем выше эта температура превращения в шве. Хотя по своей величине упругопластическая деформация аустенита невелика, она может оказывать существенное влияние на кинетику мартенситного превращения и на сопротивляемость металла околошовной зоны образованию холодных трещин. При этом существенное значение приобретает разница в температурах превращения аустенита в шве и околошовной зоне, однако не столько в связи с изменением величины деформации, сколько из-за возникновения различий в условиях и степени развития релаксационных процессов в аустените. В процессе последующего превращения аустенита в околошовной зоне развиваются небольшие сжимающие деформации и напряжения. Величина их в легированных сталях больше, чем в малоуглеродистых (см. рис. 12, б и в). Одновременно с понижением температуры начала превращения аустенита в мартенситную область (особенно ниже 350°) восстановление растягивающих продольных напряжений к моменту полного выравнивания температуры становится маловероятным. Например, в сталях 25ХН4, 35СГ и 50ХВС возникают даже заметные сжимающие напряжения. Существенное увеличение влияния превращения аустенита на величину и знак остаточных внутренних деформаций и особенно напряжений при переходе от малоуглеродистых к легированным сталям в сравнении со сталью ОХ18Н9Т обусловлено тремя основными причинами: 1) протеканием ферритного и перлитного превращений (малоуглеродистая сталь) при высоких температурах, когда металл слабо сопротивляется пластической деформации, а бейнитного и мартенситного превращений (легированная сталь) — при относительно низких температурах, при которых металл обладает более высокой сопротивляемостью пластической деформации и значительными упругими свойствами; 2) большей величиной разности между удельными объемами мартенсита и аустенита, чем феррита (или феррито-карбидных смесей (Справедливо для сталей с содержанием углерода примерно до 0,5%, так как удельный объем у карбидов, как правило, больше, чем у мартенсита)) и аустенита; 3) возрастанием этой разности с понижением температуры, так как коэффициент линейного расширения у мартенсита меньше, чем у аустенита. В. Н. Земзин [88] и П. А. Мельников [89] также показали, что в околошовной зоне закаливающихся легированных сталей развиваются продольные деформации и напряжения сжатия. Кроме того, они обнаружили, что по обе стороны от околошовной зоны при переходе к шву или основному металлу продольные напряжения изменяются скачкообразно. При этом в основном металле они всегда растягивающие, а в шве их знак зависит от типа электродов, т. е. состава наплавленного металла. Чем ниже температура превращения аустенита в металле шва, тем вероятнее развитие в нем сжимающих напряжений. Для анализа кинетики развития деформаций при сварке и их влиянияна технологическую прочность, а также структуру и свойства околошовной зоны весьма важно располагать сведениями об изменении скорости деформации в процессе нагрева и охлаждения. В работе [86] показано, что и для малоуглеродистых и для закаливающихся легированных сталей развитие внутренних деформаций в околошовной зоне с относительно высокими скоростями (0,02—0,03 мм/сек) происходит только в период нагрева и в начальной стадии охлаждения при высоких температурах. Резкое увеличение скорости деформации в области высоких температур обусловлено рядом причин: повышением коэффициента теплового расширения вследствие фазового превращения при нагреве (у аустенита он примерно в два раза выше, чем у мартенсита), увеличением скорости изменения температуры и снижением сопротивления металла пластической деформации. Перед превращением аустенита при охлаждении скорость деформации растяжения (0,0008—0,002 мм/сек) не менее, чем на один порядок ниже скорости деформации сжатия перед превращением в аустенит при нагреве (0,015—0,02 мм/сек). В процессе превращения аустенита и при последующем охлаждении она снижается еще почти на один порядок (до 0,003—0,0005 мм/сек), что при наличии мартенситной структуры указывает на вероятность локализации деформации преимущественно по границам зерен. Скорости изменения поперечных деформаций в процессе охлаждения практически такие же, как и продольных. Разница заключается лишь в величине и знаке внутренних деформаций после полного охлаждения соединения [86]. В работе [87] Н. Н. Прохоров указывает, что в околошовной зоне закаливающихся сталей могут возникать растягивающие поперечные напряжения. Проведенные им и В. С. Игнатьевой расчеты [90] показали, что вследствие мартенситного превращения растягивающие поперечные напряжения в поверхностных участках околошовной зоны могут достигать величин, близких к пределу прочности стали. А. М. Макара [91] с помощью датчиков сопротивления с базой измерения 5 мм определил, что при сварке закаливающейся стали 35ХЗНЗМ в околошовной зоне в средней части длины шва возникают растягивающие поперечные остаточные напряжения до 10 кГ/мм2, а в концевых участках шва — в два раза более высокие сжимающие. На величину деформаций и напряжений существенное влияние оказывает ряд факторов: «жесткость» или размеры (до определенного предела) и конструкция соединяемых элементов; реактивные силы, возникающие обычно вследствие ограничения деформаций свариваемых элементов; активные силы от собственного веса изделия или от полезной нагрузки; последовательность наложения швов; режим сварки и число слоев; температура подогрева; различия в составе, теплофизических свойствах, в характере и температурных интервалах фазовых превращений металла шва и основного металла и т. п. [81—83, 86]. Существенное влияние закреплений и близкого расположения швов на величину остаточных продольных и поперечных напряжений часто используется при разработке конструкции жестких проб, предназначенных для оценки склонности сталей и сплавов титана к образованию холодных трещин. Н. О. Окерблом [81, 82] показал, что в общем случае для стыковых соединений при данной ширине свариваемых листов с увеличением погонной энергии величина напряжений в околошовной зоне сначала возрастает, а затем по достижении некоторого максимума снижается. Наибольшие напряжения возникают при определенном соотношении между объемом расплавленного металла и шириной листов. В частности он предположил, что при сварке малоуглеродистой стали аустенитными электродами снижение продольных (от 35 до 30 кГ/мм2) и повышение поперечных напряжений (от 5 до 10 кГ/мм2) по сравнению со сваркой ферритными электродами обусловлены не столько различиями в характере фазовых превращений и свойствах металла шва, сколько неодинаковыми тепловыми режимами сварки за счет разных коэффициентов наплавки. Однако А. М. Макара и И. П. Карета [91] с помощью рентгеновского метода, а также датчиков сопротивления и механических тензометров при сварке под флюсом стали 35Х3HЗМ толщиной 14 мм электродными проволоками трех типов (ферритная Св08ГА, легированная ферритная Х5М, аустенитная Х20Н10Г6Т) получили настолько большую разницу в величине остаточных продольных сжимающих напряжений в околошовной зоне, что ее нельзя было объяснить изменением режима сварки. Сжимающие напряжения при применении ферритных электродов были равны 15, аустенитных — 20, а легированных ферритных — 35 кГ/мм2. При этом в первых двух случаях имел место резкий перепад остаточных продольных напряжений на границе сплавления от растягивающих в шве (соответственно 30 и 20 кГ/мм2) до сжимающих в околошовной зоне. При сварке легированными ферритными электродами в шве были сжимающие напряжения 7 кГ/мм2. В соседнем с околошовной зоной участке основного металла во всех трех случаях были обнаружены высокие растягивающие продольные напряжения (легированные ферритные электроды - 45, аустенитные и ферритные — 85 кГ/мм2.) Эти данные показывают также, что при сварке закаливающихся сталей наибольшие сжимающие продольные остаточные напряжения по абсолютной величине обычно больше растягивающих поперечных. Рациональными методами снижения остаточных напряжений при сварке являются общий подогрев, ограничение температуры охлаждения шва при многослойной сварке, повышение погонной энергии дуги при укладке второго слоя или отжигающего валика [86, 81]. Однако наиболее часто используется отпуск или отжиг изделий после сварки. О кинетике изменения и величине внутренних деформаций и напряжений в околошовной зоне при сварке титана данных очень мало. Однако, располагая сведениями о коэффициенте линейного расширения титана (8,5 * 10-6 0/1°С при 0—100° в сравнении с 11,7 * 10-6 1/°С для железа), о модуле упругости (11250 в сравнении с 21000 кГ/мм2 для железа) и характере изменений удельного объема при протекании фазовых превращений, можно в первом приближении оценить знак и порядок величин остаточных деформаций и напряжения. Превращение β→α а в титане и его α- и α + β-сплавах, а также превращениеβ→ω в α + β-сплавах титана протекают не с увеличением объема, как превращение γ→α а в железе и стали, а с небольшим уменьшением его. Единственное превращение в титане и его сплавах, которое происходит с увеличением объема, — это гидридное (на 15% при TiH 100%). Однако расчеты показывают, что при содержании 0,01% H изменение удельного объема технического титана вследствие гидридного превращения не превышает 0,1%. При полном превращении аустенита в мартенсит, например в стали с 0,38% С и 1,4% Сr, удельный объем увеличивается в среднем на 5%, т. е. в 50 раз больше (Расчет для титана проведен нами по параметру решетки гидрида α=4,409 *10-8 см (24], а для стали — по данным А. П. Гуляева [35].). Столь малый общий объемный эффект гидридного превращения в околошовной зоне, вероятно, не может привести к изменению знака остаточных продольных растягивающих деформаций и напряжений первого рода. Таким образом, следует полагать, что в отличие от закаливающихся сталей при сварке титана и его сплавов в околошовной зоне растягивающие деформации и напряжения развиваются не только поперек шва, но и вдоль него, т. е. так же, как в малоуглеродистых и аустенитных сталях. По своей величине внутренние деформации растяжения в титане в большинстве его α- и α+β-сплавов, по-видимому, должны быть не ниже, а выше, чем в стали типа 0Х18Н9Т, поскольку в сопоставимых условиях сварки этих материалов градиенты температурных полей и коэффициенты линейного расширения отличаются незначительно, но зато модуль упругости титана в два раза ниже, чем у стали. Однако предположить то же самое относительно остаточных растягивающих напряжений без специальных исследований трудно, так как, несмотря на относительно высокие значения предела текучести сплавов титана, с повышением температуры он падает более резко, чем у стали. В одной из немногочисленных работ [92] показано, что в стыковых сварных соединениях полос из сплавов титана ОТ4-1 и ВТ5-1 шириной 150 и толщиной 0,8—1,0 мм остаточные продольные растягивающие напряжения в шве и околошовной зоне достигают 37—47 кГ/мм2, Вне этой зоны на расстоянии 5 мм от центра шва напряжения резко меняют знак. Сжимающие напряжения сохраняются на расстоянии от шва до 100 мм и не превышают 2—4 кГ/мм2. По краям полос напряжения вновь становятся растягивающими (1,5—3 кГ/мм2). М.Х. Шоршоров. Металловедение. Сварка стали и сплавов титана
|