Сварка деталей тяжелого и энергетического машиностроения
В тяжелых машинах габариты, вес и сечения деталей часто оказываются настолько велики, что получение заготовок требуемого размера и формы с помощью ковки или литья вызывает большие трудности. Преодоление этих трудностей обеспечивается расчленением крупной сложной детали на более простые по форме элементы меньшего веса с последующим соединением сваркой. При этом технологичность составной детали во многом определяется выбором расположения и конструктивного оформления стыков между отдельными элементами. Поэтому вопросы расчленения крупной детали необходимо решать с учетом как методов получения заготовок отдельных элементов, так и приемов их сборки, сварки и последующей механической и термической обработки. Для машиностроения наиболее характерными деталями являются рамы, станины, валы и колеса. Рассмотрим примеры их изготовления применительно к машинам тяжелого и энергетического оборудования в условиях индивидуального или мелкосерийного производства. 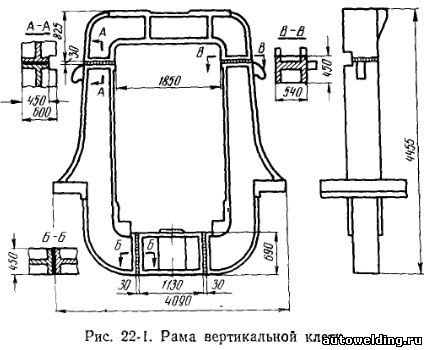
На рис. 22-1 показана рама вертикальной клети прокатного стана, составленная из четырех литых заготовок стали 35Л. Места стыков выбраны из условия симметрии сварочных деформаций и относительной простоты формы каждого элемента. Сложное очертание двутаврового сечения в месте стыка заменено сплошным (разрезы А—А, Б—Б) в целях удобства выполнения его электрошлаковой сваркой пластинчатыми электродами. Несмотря на заметное увеличение количества наплавленного металла, такое конструктивное оформление стыка оказывается более технологичным, чем выполнение номинального сечения многослойной сваркой. Это наглядно подтверждается данными диаграммы рис. 22-2, сопоставляющей стоимость выполнения 1 м длины стыкового шва металла большой толщины различными методами. 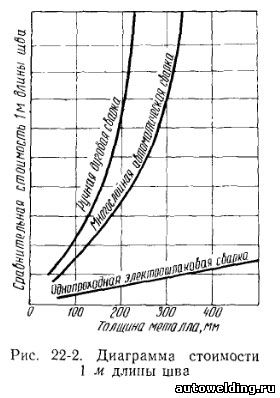
На рис. 22-3 показана другая рама, подготовленная к электрошлаковой сварке плавящимся мундштуком. Можно видеть, что сборка под сварку выполняется в горизонтальном положении с помощью скоб, стыки свариваются попарно. 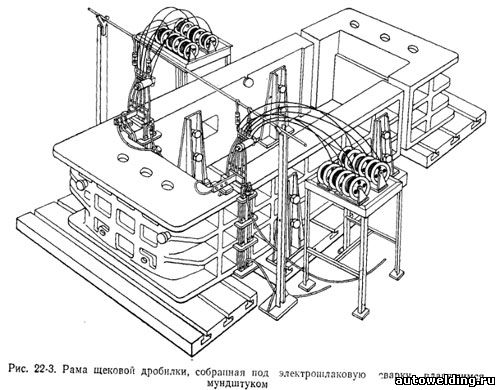
Станины тяжелых прессов изготовляют с помощью сварки сравнительно недавно, и поэтому опыт их конструирования еще не велик. Вначале наблюдалось стремление в сварном исполнении повторять формы литых конструкций. Характерным для этого случая является пример, приведенный на рис. 22-4, где рассматриваются четыре варианта конструкции поперечины пресса усилием 4500 Т. Последний вариант (рис. 22-4, г), который наиболее отличается от первоначальной литой конструкции, является наиболее легким и технологичным. 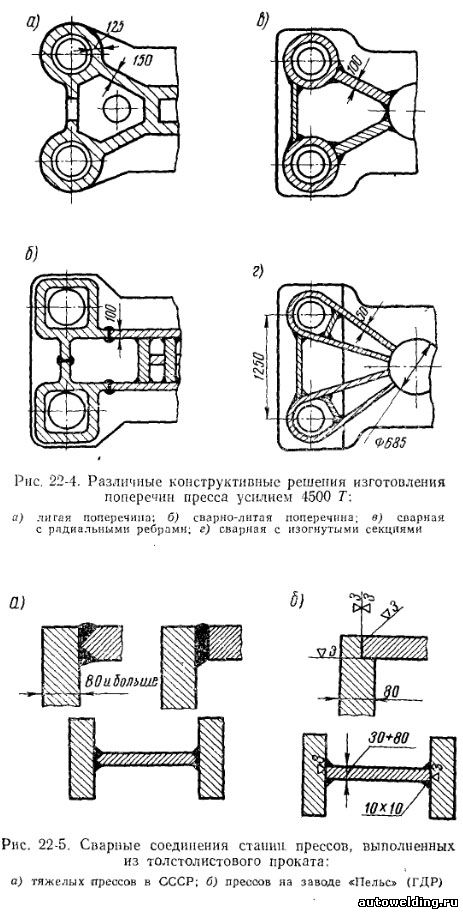
В СССР сварные соединения станин тяжелых прессов обычно выполняют с полным проплавлением присоединяемого элемента (рис. 22-5, а). В ГДР, на заводе «Пельс», выпускающем сварные станины прессов средней мощности с 1929 г., ограничиваются минимальными размерами швов (рис. 22-5, б), однако при этом производится плотная подгонка мест сопряжений листов и постановка разгрузочных заплечиков, штифтов, шипов и пазов. Дополнительные затраты на подгоночные работы компенсируются снижением трудоемкости сварочных работ. Кроме того, малый объем наплавленного металла позволяет в этом случае обходиться без последующей термообработки конструкций. 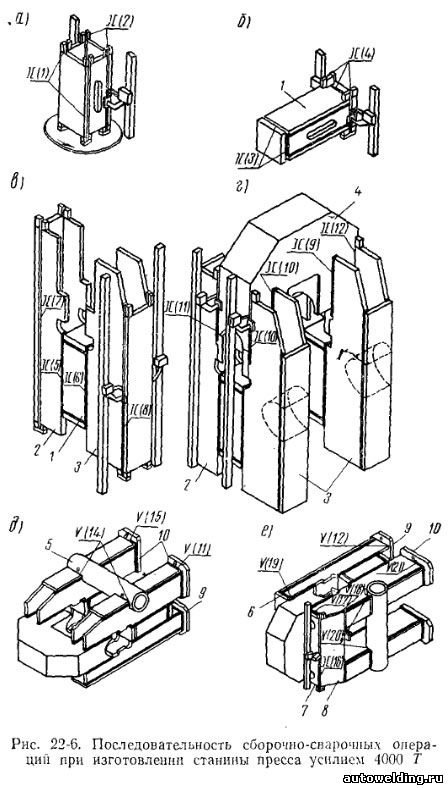
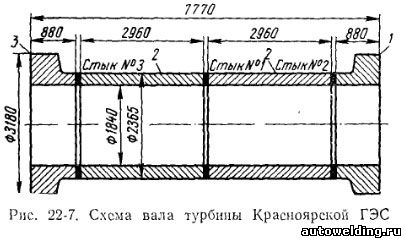
На рис. 21-7 показана сварная станина пресса усилием 4000 Т, выполненная из толстолистового проката, массивной литой траверсы и кованой трубы. Сварные соединения — стыковые, тавровые и угловые; большинство из них выполняются электрошлаковой сваркой. Последнее обстоятельство определяет некоторые особенности конструкции и последовательность выполнения сборочно-сварочных операций. Угловые и тавровые соединения элементов собираются при помощи косынок и диафрагм, стыковые — при помощи скоб. В местах, недоступных для постановки формующих медных охлаждаемых подкладок, применяют остающиеся стальные пластины. Последовательность выполнения сборочно-сварочных операций выбирается так, чтобы концы каждого из электрошлаковых швов можно было вывести за пределы тела детали. Поэтому общей сборке сложной детали обычно предшествует сборка и сварка относительно простых узлов. При этом, для уменьшения угловых сварочных деформаций, желательно, чтобы каждый собранный под сварку узел имел замкнутое сечение. Применительно к станине пресса усилием 4000 Т (рис. 21-7) последовательность и содержание основных сборочно-сварочных операций показана на рис. 22-6. Первым узлом является тумба 1. Сначала в замкнутое сечение собирают ее боковые стенки, и электрошлаковые швы (1) и (2) выполняют с полным проплавлением привариваемого элемента (рис. 22-6, а). Затем устанавливают горизонтальные листы тумбы и выполняют первые пары швов (3) и (4) (рис. 22-6, б). Участки первых пар швов, препятствующие установке карманов и выводу усадочных раковин вторых пар швов, удаляются из зазора огневой резкой. Готовая тумба входит в сборку второго, более крупного узла — стойку (рис. 22-6, в). Замкнутое сечение образуется присоединением элементов полустоек: 2 и 3; швы (5), (6), (7) и (8) выполняются электрошлаковой сваркой. Формирование корпуса станины завершается сборкой стоек с траверсой 4 и сваркой электрошлаковых швов (9), (10), (II) и (12) (рис. 22-6, г). Затем в полустойках 3 огневой резкой вырезают пазы под трубу 5. Следует заметить, что образование пазов резкой не плоских заготовок, а уже сваренного узла с удалением части шва, является приемом, характерным для конструкции, выполняемых электрошлаковой сваркой. Целесообразность такого приема объясняется трудоемкостью подготовки и зачистки стыков в местах начала и конца каждого электрошлакового шва. В этом случае выполнить длинный непрерывный шов с последующим удалением его части резкой оказывается выгоднее, чем выполнять два более коротких шва. Завершение сборки и сварки станины требует ряда кантовочных операций. Так, установка трубы 5 и лап 9 и 10 и сварка полуавтоматом под флюсом многослойных швов (14) и (15) производится, как показано на рис. 22-6, д, а установка крышек 6, 7 и 8 и выполнение электрошлаковых швов (16) и многослойных швов (17), (18), (19), (20), (21) и (22) — на рис. 22-6, е. При изготовлении деталей тяжелых машин завершающими операциями являются термическая и механическая обработкапосле сварки. Рамы и станины с толщиной свариваемых элементов более 100 мм, как правило, подлежат термообработке. При этом для деталей, эксплуатирующихся в условиях нормальных температур и изготовленных из сталей, сохраняющих высокие пластические свойства в зоне термического влияния, можно ограничиться проведением высокого отпуска. При более жестких условиях сварную деталь для улучшения свойств сварных соединений обычно перед высоким отпуском подвергают нормализации. Точность размеров станин и рам в основном обеспечивается путем последующей механической обработки. Характерными примерами сварных валов большого размера могут служить валы мощных турбин. Конструкция валов гидравлических турбин проста, это массивная труба с одним или двумя фланцами. Заготовки обечаек обычно получают ковкой, заготовки фланцев — также ковкой или иногда в виде стальных отливок. Так, валы Красноярской ГЭС (рис. 22-7) выполнены из кованых заготовок Ст. 25ГС. На сборку среднего стыка обечайки 2 поступали после черновой механической обработки с припуском 20 мм на сторону. Сборка стыка под электрошлаковую сварку выполнялась с переменным зазором: 33 мм под карманом для наведения сварочной ванны и 38 мм в плоскости, повернутой на 90° от кармана в направлении вращения. После выполнения среднего стыка (рис. 22-7), сваренные обечайки проходили высокий отпуск и подвергались промежуточной механической обработке. Затем выполнялись сборка и сварка стыков с фланцами 1 и 3. Чистовую механическую обработку, обеспечивающую точность размеров готового вала, производили после нормализации и высокого отпуска. Отличительной особенностью выполнения кольцевых стыков весьма большого сечения является трудность обеспечения непрерывности процесса сварки от начала до заварки замка. Такая непрерывность необходима как из соображений качественного выполнения шва (при нарушении процесса неизбежно возникновение несплавления кромок и возможно образование трещин), так и соблюдения величины и направления ожидаемой сварочной деформации излома осей стыкуемых деталей. Так как время сварки может составлять десятки часов, то возникает опасность отказа аппаратуры и прежде всего выхода из строя мундштуков, направляющих электродную проволоку в сварочную ванну. Сменить мундштуки без остановки процесса сварки невозможно, а остановить процесс недопустимо. Поэтому для сварки кольцевых швов большого сечения используют специальную установку (рис. 22-8) с двумя дублирующими сварочными головками. При выходе работающей головки из строя, ее место тотчас занимает вторая головка и процесс сварки прерывается лишь на весьма непродолжительное время. 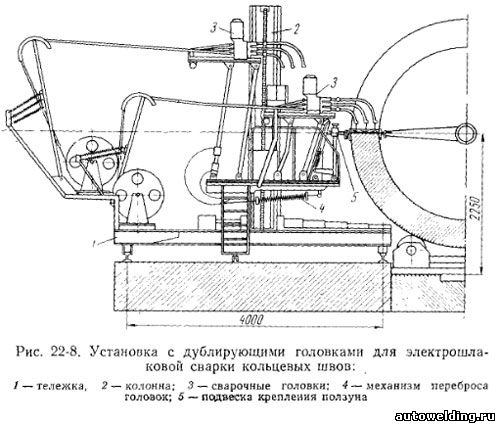
Валы газовых и паровых турбин изготовляют из жаропрочных сталей, что затрудняет получение заготовок большого размера с помощью литья и ковки. Поэтому крупные валы сваривают из поковок относительно небольшого размера и простой формы. Так, на рис. 22-9 показан ротор газовой турбины, составленный из отдельных дисков и концевых частей. При разработке конструкции и технологии изготовления подобных изделий основными требованиями являются жесткое ограничение величины сварочных деформаций искривления продольной оси ротора и получение надежного проплавления швов при их односторонней сварке. Необходимость соблюдения жесткого допуска на искривление продольной оси ротора от сварки вызывается наличием внутренних замкнутых полостей, смещение которых относительно оси вращения вызывает неуравновешенность. При работе на высоких числах оборотов такая неуравновешенность совершенно недопустима, а ее устранение ограничено недоступностью внутренних полостей для механической обработки. Поэтому необходима точная сборка и прецизионная технология сварки. Кованые заготовки дисков после механической обработки центрируются относительно друг друга направляющими поясками, требуемая величина зазора в разделке обеспечивается постановкой проставок. Собранные элементы плотно стягиваются между собой тягами 1 (рис. 22-9) с компенсирующими усадку пружинами 2, и в вертикальном положении ротор подается на сварку. 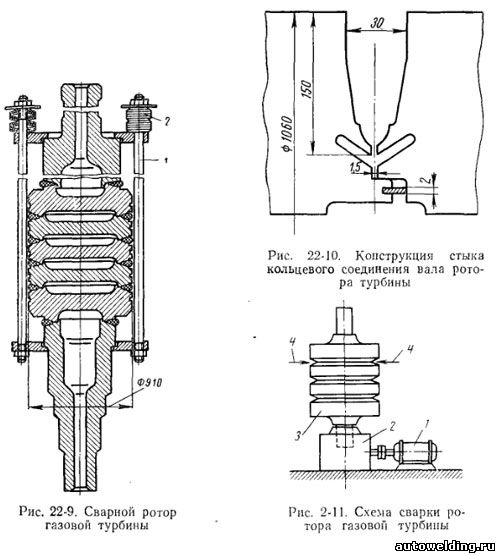
Однопроходная сварка не может обеспечить симметрии сварочных деформаций из-за неравномерности поперечной усадки по периметру кольцевого шва, поэтому сварку выполняют во много слоев. Полный провар в корне шва достигается специальной конструкцией разделки или применением остающихся кольцевых подкладок. Оригинальную конструкцию стыка применяют в ЧССР (рис. 22-10). Посадочная ступенька и упорное кольцо из малоуглеродистой стали толщиной 2 мм обеспечивают высокую точность сборки ротора и необходимую податливость стыка при сварке. Это весьма важно с позиции предупреждения образования трещин в соединении. Притупление разделки выбрано из условия получения полного провара корня шва. Специальные наклонные каналы уменьшают жесткость кромок при выполнении корневого слоя и тем самым предотвращают образование в нем трещин, а также обеспечивают лучшие условия для ультразвукового контроля сварного соединения. Первые слои швов выполняют при вращении ротора 3 от мотора 1 через редуктор 2. Вертикальное расположение оси ротора 3 имеет цель исключить влияние силы тяжести (рис. 22-11). Для обеспечения симметрии сварочных деформаций каждый корневой шов выполняют одновременно двумя диаметрально расположенными сварочными головками 4 вольфрамовым электродом в аргоне. Затем в этом же положении ряд слоев укладывают плавящимся электродом в среде С02. После заполнения той части разделки, которая необходима для обеспечения определенной жесткости ротора, он переносится в центровой вращатель с горизонтальным расположением оси, и основная часть разделки заполняется многослойной сваркой под флюсом в нижнем положении. Такая технология позволяет предотвратить искривление настолько, что биение сваренного вала не превышает 0,5 мм на длине 5 м.Сварные колеса в тяжелом и энергетическом машиностроении достаточно разнообразны. Среди них рабочие колеса мощных гидротурбин выделяются как размерами, так и сложностью процесса изготовления. Так, например, рабочее колесо турбины Красноярской ГЭС (рис. 22-12) имеет диаметр свыше 8 м, что намного превышает габарит подвижного состава железных дорог. Поэтому возможность его изготовления целиком в условиях Ленинградского металлического завода, без расчленения на монтажные блоки, была обеспечена только благодаря наличию водного пути от места расположения завода-изготовителя до места монтажа. 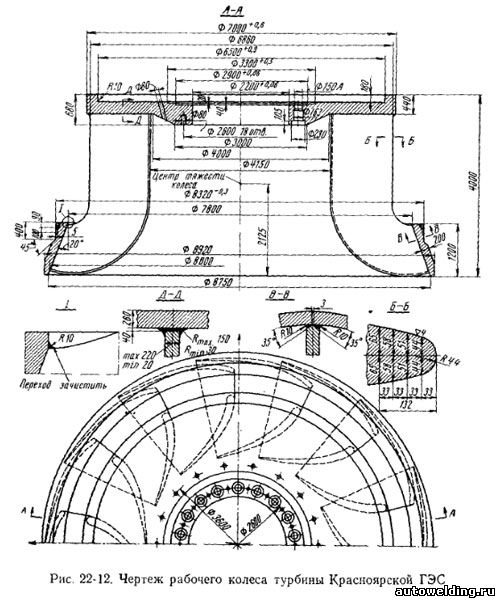
Рабочее колесо состоит из верхнего и нижнего ободов и лопастей. Последовательность и содержание основных этапов процесса его изготовления показаны на рис. 22-13. Верхний обод выполнен из двух литых заготовок стали 20ГС-Л с максимальной толщиной 500 мм. Отливки проходили предварительную механическую обработку по всем поверхностям, за исключением поверхности по наружному диаметру. Затем заготовки собирали п кольцо и устанавливали в вертикальное положение под электрошлаковую сварку, причем для компенсации неравномерности поперечной усадки по длине шва зазор в нижней части стыка задавали в пределах 25—27 мм, а в верхней 50—54 мм. После сварки верхний обод подвергался высокому отпуску и поступал па механическую обработку, где внутренняя поверхность обода, примыкающая к лопастям, обрабатывалась окончательно, а остальные поверхности с припуском. Лопасти рабочего колеса выполнялись кокильной отливкой из стали 20ГС-Л. Требуемая точность формы обеспечивалась рубочными и наплавочными работами с проверкой по пространственному шаблону и последующей шлифовкой. Для повышения стойкости против кавитационного износа часть выпуклой поверхности лопастей подвергалась наплавке ленточным электродом безникелевой стали 30Х10Г10 под флюсом. После шлифовки наплавленной поверхности и механической обработки торца, примыкающего к верхнему ободу, лопасти поступают на сборку. 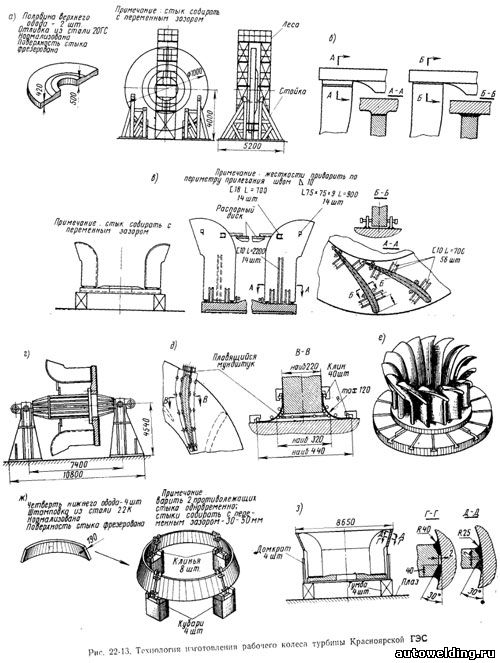
Сборка начинается с разметки гладкой внутренней поверхности верхнего обода под установку лопастей по шагу и профилю. Отказ от использования приливов-пеньков (рис. 22-13, б), которые в известной степени задавали положение лопастей, позволяет повысить точность их размещения и облегчить обработку поверхности обода. Четырнадцать лопастей последовательно устанавливали на верхний обод с соблюдением зазора в стыке: снизу 37 и вверху 47 мм, и закрепляли с помощью приварки скоб н технологических жесткостей (рис. 22-13, в). Затем на верхнем ободе закреплялась ось с цапфами и с ее помощью собранный узел устанавливали на стойках специального кантователя (рис. 22-13, г). Этим обеспечивалась возможность поворота узла в положение, удобное для выполнения каждого стыка электрод шлаковой сваркой плавящимся мундштуком. Плавный переход от тела лопасти к телу верхнего обода задавали соответствующей формой медных подкладок, охлаждаемых водой, их крепление с помощью клиньев показано на рис. 22-13, д. После сварки и промежуточного высокого отпуска производили обработку торцов лопастей под сопряжение с нижним ободом на карусельном станке (рис. 22-13, е) и подготовку кромок под К-образную разделку. Нижний обод собирали из четырех штампованных заготовок стали 22К толщиной 190 мм, как показано на рис. 22-13, ж. После попарного выполнения стыков электрошлаковой сваркой) и высокого отпуска обод подвергали механической обработке с оставлением припуска 15 мм по внешнему диаметру на чистовую обработку. Общую сборку колеса производили, как показано на рис. 22-13, з. При помощи гидравлических домкратов нижний обод поднимали и вводили в сопряжение с кромками лопастей. Сварка производилась одновременно 2—4 сварщиками диаметрально противоположных стыков полуавтоматами в среде СО2. Сваренное колесо проходило полный цикл термообработки: нормализацию и высокий отпуск, после чего выполнялась окончательная механическая обработка. Применительно к изготовлению радиально-осевых колес крупных гидротурбин возможны и другие конструктивно-технологические решения, отличающиеся от только что рассмотренного выше. Так, рабочее колесо Плявиньской ГЭС выполнялось из двух частей, исходя из необходимости перевозки по железной дороге, причем заводская сварка осуществлялась преимущественно вручную обмазанным электродом. Такая технология изготовления представлена на рис. 22-14. 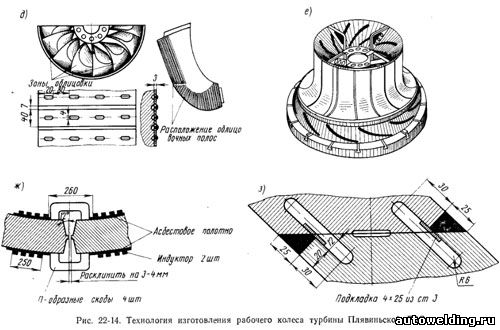
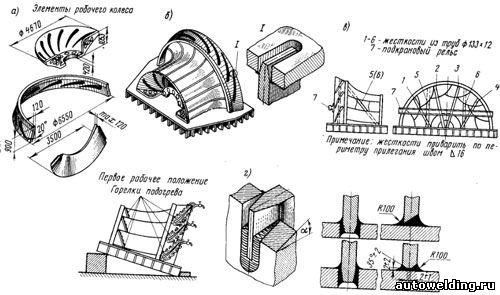
Все элементы этого колеса выполнялись литьем из стали 20ГС-Л. Нижний и верхний ободы отливались из двух частей и до поступления на общую сборку проходили нормализацию и фрезеровку плоскостей разъема, а после спаривания подвергались предварительной обточке, с чистовой обработкой внутренних поверхностей, сопрягаемых с лопастями. После разметки этих поверхностей и огневой вырезки пазов под лопасти ободы разбирались на две половины для передачи на общую сборку. Отливки лопастей после отжига подвергали механической обработке для обеспечения требуемой геометрической формы и состояния поверхности. Кроме того, их торцы подрезали огневой резкой и подрубали так, чтобы при сборке под сварку они входили в соответствующие пазы верхнего и нижнего ободов. Так как рабочее колесо изготовлялось из двух половин, то две лопасти, попадающие в плоскость разъема, делались разрезными и впоследствии сваривались при монтаже. Для совпадения плоскостей разъема обеих половин колеса необходимы точная сборка каждой из половин и предотвращение искажений этой плоскости при сварке и термообработке. Обеспечение этого достигалось приваркой половин ободов по плоскости разъема к плоскости достаточно жесткой технологической плиты (рис. 22-14, б). Затем в пазы ободов заводили хвостовики лопастей и прихватывали, разрезные лопасти, кроме того, прихватывали к плите по плоскости разъема. Сборка завершалась установкой дополнительных технологических элементов жесткости (рис. 22-14, в). Приварка лопастей к ободам производилась способом «поперечной горки» электродами типа Э50А путем заполнения разделки в пазах с последующей зачисткой корня шва и выведением галтельных переходов (рис. 22-14, г). Для предотвращения образования трещин применяли предварительный, сопутствующий и заключительный подогрев многопламенными газовыми горелками до температуры 120—200° С. При выполнении сварных соединений полуколесо вместе с технологической плитой кантовали в три различных пространственных положения. Освобождение сваренного полуколеса от связей с жесткой плитой производили только после завершения сварки и прохождения высокого отпуска для снятия остаточных сварочных напряжений. Затем выпуклые части лопастей каждого полуколеса подвергали облицовке полосами кавитационно стойкой стали 1Х18Н9Т размером 500x50x3 мм. Эти полосы приваривали к лопастям полуавтоматами в среде СО2, швы зачищали заподлицо с поверхностью облицовки (рис. 22-14, д). Заводское изготовление завершалось окончательной механической обработкой колеса, временно собранного из двух половин (рис. 22-14, е). На место монтажа колеса доставлялись по железной дороге в разобранном виде. Конструкцией колеса предусмотрено соединение стыков верхнего обода на болтах, а нижнего — с помощью сварки. Такое решение определяется, с одной стороны, невозможностью осуществить болтовое соединение нижнего обода из-за жесткого ограничения габаритов стыка, а с другой стороны,— стремлением избежать искажений окончательно обработанной поверхности верхнего обода, которой он присоединяется к фланцу вала гидротурбин. Стыки нижнего обода сваривались ручной сваркой способом «поперечной горки» одновременно четырьмя; сварщиками попарно «дуга в дугу». Подогрев до температуры 120—200°С производили с помощью индукторов (рис. 22-14, ж). Эти же индукторы использовали для высокого отпуска стыков обода после сварки. Стыки разъемных лопастей сваривали многослойной сваркой вручную без подогрева», (рис. 22-14, з). Николаев Г.А. "Расчет, проектирование и изготовление сварных конструкций"
|