Сварка в углекислом газе
Особенности переноса электродного металла при сварке в углекислом газеПри сварке в СO2 проволоками Св-08ГС и Св-08Г2С в основном используют процесс с частыми принудительными короткими замыканиями и процесс с крупнокапельным переносом (табл. 3.1). При сварке порошковыми проволоками применяют процесс с непрерывным горением дуги, а при сварке активированной проволокой — струйный процесс (рис. 3.1). 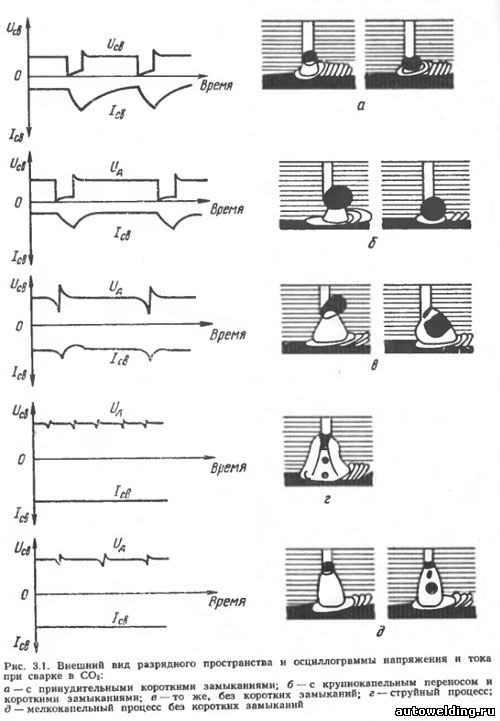
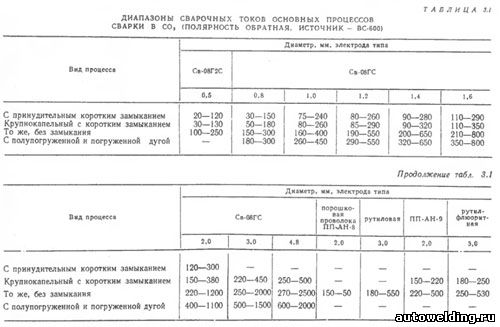
Процесс с частыми принудительными короткими замыканиями получают при сварке в СO2 проволоками ф0,5—1,4 мм путем изменения сварочного тока, обеспечивающего изменение скорости плавления электрода и давления дуги. Весь процесс можно разделить на ряд подобных повторяющихся циклов (рис. 3.1). Теплота, выделяемая дугой, интенсивно расплавляет электродную проволоку и деталь. При этом длина дуги быстро увеличивается. По мере уменьшения сварочного тока скорость расплавления проволоки и давление дуги уменьшаются. В результате капля электродного металла и ванночка сближаются, замыкая разрядный промежуток. Дуга гаснет, напряжение резко уменьшается, а сила тока в цепи возрастает С увеличением тока растет электродинамическая сила и приводит к ускорению перехода капли в ванну и образованию шейки между электродом и каплей. Утоненная шейка перегревается проходящим током и перегорает со взрывом. Напряжение резко возрастает, и зажигается дуга. После этого все явления повторяются. Основные параметры данного процесса: среднее напряжение процесса сварки Uсв, среднее значение сварочного тока Iсв, максимальный ток Iк.з., минимальный ток Imin, длительность горения дуги Iд, длительность короткого замыкания t к.з., длительность цикла T= t д+ t к.з., скорость нарастания тока при коротком замыкании разрядного промежутка каплей ΔIк.з./Δt и скорость снижения тока при горении дуги ΔIд/Δt. С повышением напряжения увеличивается длительность горения дуги и всего цикла, а частота коротких замыканий уменьшается, возрастают потери на окисление и разбрызгивание, а форма шва несколько улучшается. При повышении напряжения процесс переходит в крупнокапельный. Характер течения процесса с частыми принудительными короткими замыканиями в большой степени зависит от скорости нарастания Iк.з. в цепи (ΔIк.з./Δt). При сварке проволоками ф0,8÷1,4 мм при ΔIк.з./Δt> 200÷300 кА/с процесс стабилен, но сопровождается повышенным разбрызгиванием. При ΔIк.з./Δt<40 кА/с процесс протекает с редкими короткими замыканиями, импульсный характер изменения силы тока выражен слабо и на низких напряжениях процесс протекает нестабильно. При средних значениях ΔIк.з./Δt=60÷180 кА/с процесс протекает стабильно и отличается небольшим разбрызгиванием. Характер процесса и технологические характеристики сварки в СO2 в определенной степени зависят также от наклона внешней характеристики источника питания дуги. При пологопадающих внешних характеристиках источника тока увеличение угла наклона характеристики приводит к некоторому увеличению внешней составляющей длины дуги; дуга более подвижная и эластичная, ширина разогрева изделия и ширина шва несколько увеличиваются. Сочетание падающей внешней характеристики с высокими регулируемыми скоростями нарастания тока короткого замыкания и регулировкой амплитудных значений тока короткого замыкания дает возможность получать процесс сварки в СO2 с принудительными короткими замыканиями и процесс сварки в СO2 без коротких замыканий с хорошими технологическими характеристиками. Процесс с крупнокапельным переносом наблюдается при сварке проволоками ф0,5—1,6 мм на повышенных напряжениях, а для проволок > ф1,6 мм — в широком диапазоне режимов сварки кремниймарганцевыми проволоками. При низких напряжениях процесс протекает с короткими замыканиями, а при высоких — без них. Процесс с крупнокапельным переносом обычно сопровождается повышенным разбрызгиванием. Для уменьшения разбрызгивания и улучшения формирования шва при сварке с короткими замыканиями рекомендуется снижать значение ΔIк.з./Δt (например, путем увеличения индуктивности цепи и включения в цепь балластного сопротивления). Для получения стабильного процесса сварки в СO2 с хорошим формированием шва и небольшим разбрызгиванием необходимо строго соблюдать определенные соотношения между током и напряжением (рис. 3.2). Для повышения производительности процесса и уменьшения разбрызгивания целесообразно вести сварку с погружением дуги в ванну так, чтобы внешняя составляющая дуги была равна 2—3 мм. Этот процесс реализуется на повышенных токах (табл. 3.1). 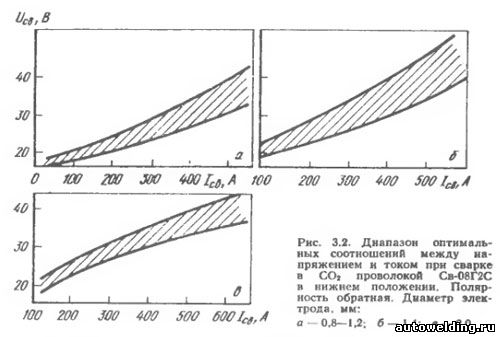
Струйный процесс в СO2 можно получить только при использовании проволок, активированных цезием, рубидием, калием, натрием, барием, церием и солями РЗЭ. Процесс протекает без разбрызгивания с хорошим формированием шва. Сварку проволоками, активированными солями рубидия и цезия, можно выполнять также с наложением импульсов тока. Однако до настоящего времени этот процесс не нашел широкого практического применения. При использовании порошковых проволок рутил-флюоритного типа сварка протекает с крупнокапельным переносом. Процесс во многом подобен сварке проволокой СВ-08Г2С сплошного сечения. При использовании порошковых проволок рутилового типа процесс сварки ведут с непрерывным горением дуги и переносом капель среднего размера, сопровождающимися небольшим разбрызгиванием и хорошим формированием шва. В последние годы разработаны: проволока с дополнительным сердечником-фитилем, заполненным в основном оксидом титана (АПАН-2), и проволока, легированная РЗЭ (Св-14Г2Сч). Эти проволоки при сварке в СO2 на повышенных токах (более 30 А для ф1,6 мм) обеспечивают хорошее формирование шва и малое разбрызгивание. При сварке в смесях СO2+O2 (15—30%) могут выполняться процессы с крупнокапельным переносом и с частыми короткими замыканиями. Добавление кислорода к СO2 незначительно изменяет характер процесса (он характеризуется более высоким окислительным потенциалом защитной среды и большей жидкотекучестью ванночки). Для сварки используют проволоки с повышенным содержанием раскислителей. Формирование шва несколько лучше, чем при сварке в СO2, но поверхность шва покрыта шлаком. В смесях Аr+СO2 (до 15%) могут быть получены струйный и крупнокапельный процессы, а при содержании >20% СO2 — процессы с частыми короткими замыканиями и крупнокапельный. Сварка в смеси Аr+20—25% СO2 или 20% СO2 и 5% O2 обеспечивает лучшее формирование шва и меньшее разбрызгивание, чем сварка в СO2. Перенос металла с электрода на изделие определяет технологические характеристики и области применения процессов сварки плавящимся электродом. Различают следующие основные виды переноса электродного металла при сварке в СO2 и его смесях (см. рис. 3.1): с принудительными короткими замыканиями, крупнокапельный с естественными короткими замыканиями разрядного промежутка, то же без коротких замыканий, перенос каплями среднего и малого размера без коротких замыканий и, наконец, струйный перенос. При крупнокапельном переносе на электроде образуются капли диаметром >1,5 диаметра электрода. Если капля больше длины разрядного промежутка, то переход ее в ванну сопровождается коротким замыканием разрядного промежутка и погасанием дуги. Если капля меньше длины разрядного промежутка, то переход ее в ванну происходит без короткого замыкания. Основными силами, обусловливающими крупнокапельный перенос, являются сила тяжести, силы поверхностного натяжения, давление плазменных потоков и реакция испарения. На малых токах отрыв капли от электрода и направление ее полета определяются в основном силой тяжести, а на больших токах — электродинамической силой. Поэтому процессы с крупнокапельным переносом электродного металла применимы для сварки в нижнем положении. С повышением напряжения дуги, увеличением диаметра электрода и переходом на прямую полярность диаметр капель увеличивается. С увеличением силы тока диаметр капель уменьшается. При сварке с крупнокапельным переносом без коротких замыканий разбрызгивание металла происходит в основном из-за случайного вылета за пределы шва крупных капель и систематического выброса мелких капель с электрода (рис. 3.3,а). Помимо этого из ванны выбрасываются мелкие капли, что вызвано выделением СО. Разбрызгивание сравнительно велико. При сварке с принудительными короткими замыканиями разбрызгивание происходит из-за выброса мелких капель вследствие взрыва шейки и выброса остатка капли с электрода (рис. 3.3,б). Для уменьшения разбрызгивания рекомендуется подбирать оптимальные скорость нарастания и силу тока Iк.з., а также увеличивать наклон внешней характеристики источника питания дуги. Это достигается включением в сварочную цепь дросселя или дросселя и балластного реостата. С повышением напряжения разбрызгивание усиливается, а с увеличением тока оно сначала усиливается, а затем ослабевает (рис. 3.4). Наличие на проволоке ржавчины способствует разбрызгиванию в связи с взрывом крупных капель. В начале сварки и при нарушениях процесса наблюдается резкое увеличение разбрызгивания в результате выброса нерасплавленной части электрода и расплескивания ванны. 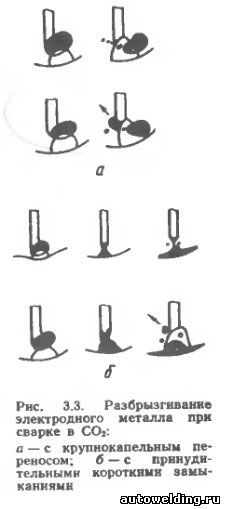
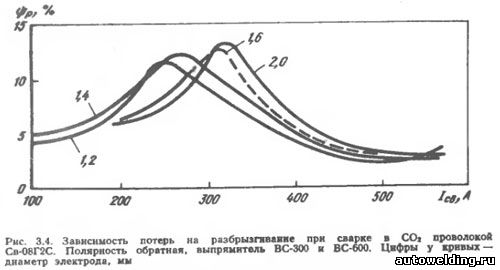
Перенос каплями среднего размера происходит при сварке порошковой проволокой рутилового типа, активированными проволоками и с принудительным управлением путем наложения импульсов тока, изменения силы тока при сварке, пульсирующей и вибрирующей подачи электрода. Разбрызгивание при этом переносе незначительное. При струйном переносе жидкий металл на электроде вытянут в виде конуса, с конца которого отрываются мелкие капли диаметром менее 2/3 диаметра электрода. Перенос определяется электродинамической силой, силами поверхностного натяжения, давлением плазменных потоков и реакцией испарения. Сила тяжести невелика, поэтому электродный металл переносится в ванну при сварке во всех пространственных положениях. Струйный перенос электродного металла наблюдается при сварке в СO2 активированной проволокой и в смесях Аr+СO2 (<25%). Минимальный ток, при котором наступает струйный перенос, называют критическим Iкр. С увеличением диаметра электрода Iкр возрастает. Разбрызгивание при струйном переносе незначительное. Сварочная проволокаСварочные проволоки выпускают с тонким медным покрытием и без него. На поверхности проволоки, а также в надрывах поверхностного слоя имеется технологическая смазка. В некоторых случаях проволоки покрывают антикоррозионными смазочными материалами, которые вносят в зону дуги водород и азот. В результате этого снижается стабильность процесса, повышается разбрызгивание, ухудшается формирование шва и понижается ударная вязкость металла шва. Особенно процесс сварки в СO2 ухудшается при наличии на проволоке ржавчины и нитрата натрия, входящего в состав некоторых смазочных материалов. Механическая очистка и травление проволоки немного повышают стабильность процесса и уменьшают содержание водорода. В наибольшей степени удалить водород и азот из процесса, повысить ударную вязкость шва, улучшить стабильность процесса сварки и формирование шва, а также уменьшить разбрызгивание можно путем прокаливания проволоки при 200—250 °С в течение 1,5—2 ч. Ржавчина на проволоке приводит к резкому снижению стабильности процесса и повышению разбрызгивания. Для ее удаления рекомендуется химическая или электрохимическая очистка проволоки и механическая очистка с последующим прокаливанием при 150—250 °С в течение 1,5—2 ч. Для надежной подачи по гибким шлангам и хорошего контактирования с токоподводящим наконечником сварочной горелки проволоки должны иметь определенную жесткость. Мягкие и чрезмерно жесткие (пружинистые) проволоки плохо подаются по шлангам. Технологические особенности процесса сварки в СO2Основными параметрами режима сварки в СO2 и его смесях являются: род защитного газа; полярность и сила тока; напряжение сварки; диаметр, скорость подачи, вылет, наклон и колебания проволоки; скорость сварки; расход и состав защитного газа. Сварку в СO2 обычно выполняют на постоянном токе. Однако возможна сварка и на переменном токе. Сварочный ток и диаметр проволоки выбирают в зависимости от толщины металла и расположения шва в пространстве. Стабильный процесс сварки с хорошими технологическими характеристиками можно получить только в определенном диапазоне силы тока, который зависит от диаметра и состава электрода и рода защитного газа (см. табл. 3.1). Сила тока определяется полярностью тока, диаметром, составом, скоростью подачи (рис. 3.5) и вылетом электрода, составом защитного газа, а также напряжением дуги. Регулируют силу тока изменением скорости подачи проволоки (рис. 3.5). Сила тока определяет глубину провара и производительность процесса. 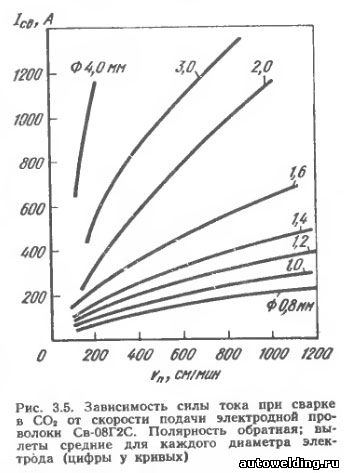
Второй важнейший параметр режима сварки — напряжение процесса сварки. С повышением напряжения увеличивается ширина шва и улучшается формирование валика. Однако одновременно возрастают излучение дуги и угар элементов, а также повышается чувствительность дуги к «магнитному дутью». При пониженных напряжениях ухудшается формирование шва, а при сварке на повышенных напряжениях увеличивается разбрызгивание. Оптимальные напряжения сварки (см. рис. 3.2) зависят от силы тока, диаметра и состава электрода, а также рода защитного газа. Сварка в СO2 проволокой Св-08Г2С на прямой полярности отличается большей длиной дуги, сильным излучением, а в ряде случаев большим разбрызгиванием, чем на обратной полярности. На прямой полярности скорость расплавления электрода в 1,6—1,8 раза выше, а глубина провара и ширина шва меньше, чем на обратной. Влияние скорости варки такое же, как и при сварке на обратной полярности. Наклон электрода до 15° «углом вперед» и «углом назад» не отражается на характеристиках процесса сварки. Наклон электрода «углом вперед» на 15—30° несколько уменьшает глубину провара и увеличивает ширину шва. При наклоне электрода на 15—30° «углом назад» формирование шва несколько ухудшается. Сварка в СO2 проволокой Св-14Г2Сч ведется на прямой полярности; достигаются хорошие технологические характеристики процесса, малое разбрызгивание и хорошее формирование шва. Состав защитного газа существенно влияет на технологические характеристики процесса. Так, в среде СO2+O2 (<15%), Аr+СO2(>20%) и Аr + O2+СO2(>20%) можно выполнил, сварку во всех пространственных положениях. Смеси СO2+O2 (>20%), Аr + СO2 (<20%) и Аr+O2 + СO2 (<20%) пригодны для сварки стационарной дугой в нижнем положении и с наложением импульсов во всех положениях. При сварке в СO2, СO2+O2 и Аr+СO2 (>20%) на всех режимах и в смесях Аr+O2+СO2 (<20%) и Аr+СO2 (<20%) на токах менее критических значений форма провара треугольная. При сварке в смесях Аr+СO2 (<10%) и Аr + O2+СO2 (<10%) на токах, превышающих критические значения, наблюдается узкое глубокое проплавление в средней части провара. С уменьшением содержания в смеси СO2, увеличением силы тока и уменьшением диаметра электрода глубина узкого проплавления увеличивается. Химический состав проволоки, смазка и загрязнения, находящиеся на проволоке и свариваемом металле, могут оказывать влияние на силу тока, длину дуги, напряжение и характер процесса. Вылет электрода при сварке проволоками ф0,5—1,4 мм влияет на стабильность процесса сварки. Это обусловлено изменением нагрева электрода на вылете проходящим током. Допустимый вылет электрода зависит от диаметра, удельного электросопротивления электрода и сварочного тока. При малых вылетах затрудняется видимость зоны сварки и возможно подплавление токопровода, а при больших — нарушается стабильность процесса. При сварке проволоками ф1,6 мм и более влияние вылета электрода на стабильность протекания процесса сварки намного меньше. В этих случаях сварку можно выполнять при нормальных и повышенных вылетах. Увеличение вылета позволяет повысить коэффициент расплавления электрода и уменьшить глубину провара. Влияние свойств источника питания существенно сказывается на технологических характеристиках при ведении процесса с короткими замыканиями в СO2 и смесях Аr+СO2, Аr+O2 + СO2. В этих случаях для получения стабильного процесса, хорошего формирования швов и небольшого разбрызгивания необходимо питать дугу от источника с определенными динамическими свойствами по току (рис. 3.6). Оптимальные скорости нарастания Iк.з. зависят прежде всего от диаметра электрода. Для получения хорошего формирования шва при сварке в нижнем положении целесообразно понижать скорость нарастания Iк.з., повышать напряжение и использовать для питания дуги источники с пологопадающей внешней характеристикой и комбинированной внешней характеристикой. При чрезмерном уменьшении скорости нарастания Iк.з. затрудняется начало сварки и снижается стабильность процесса сварки. При сварке в СO2 без коротких замыканий на средних и больших токах, а также в смесях Аr + O2+СO2 и Аr + СO2 скорости нарастания Iк.з. оказывают значительно меньшее влияние на течение процесса. В этих случаях оптимальные характеристики источника питания определяются прежде всего диаметром электрода и родом защитного газа, а также условиями получения хорошего начала и окончания сварки. 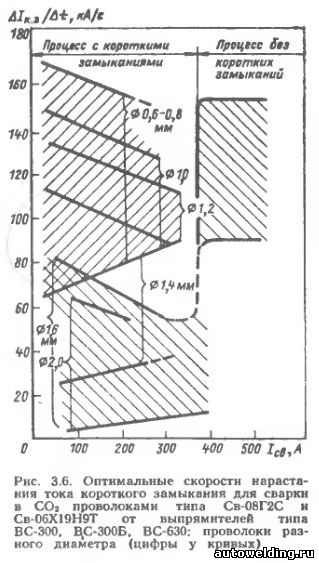
Сборка соединений под сварку плавящимся электродом в СO2 зависит от типа соединения, толщины металла, расположения шва в пространстве, способа сварки (автоматическая или полуавтоматическая). Требования к качеству сборки и подготовки соединения под полуавтоматическую сварку в СO2 проволоками ф0,8—2,5 мм должны соответствовать ГОСТ 14771—76. Чем выше качество сборки соединения, тем выше производительность в процессе сварки. По возможности рекомендуется собирать и сваривать соединения в приспособлениях без прихваток. При сборке на прихватках последние следует устанавливать с обратной стороны соединения. Прихватку можно выполнять контактной сваркой, сваркой неплавящимся электродом и сваркой тонкой проволокой в СO2. Размеры прихваток и их расположение зависят от толщины металла и типа свариваемого соединения. Прихватки перед сваркой должны быть тщательно очищены. При выполнении прихваток в СO2 проволоками ф0,8— 1,4 мм сборку осуществляют короткими швами, которые не перевариваются, а остаются в соединении как основные швы. Продолжение: Техника сварки в углекислом газе См. также: Сварка электрозаклепками и точками в СO2
|