Выбор и расчет механизма привода сварочных кантователей
В практике изготовления сварных металлоконструкций широко применяют цапковые двухстоечные кантователи и манипуляторы-позиционеры с механическим и пневматическим приводом. 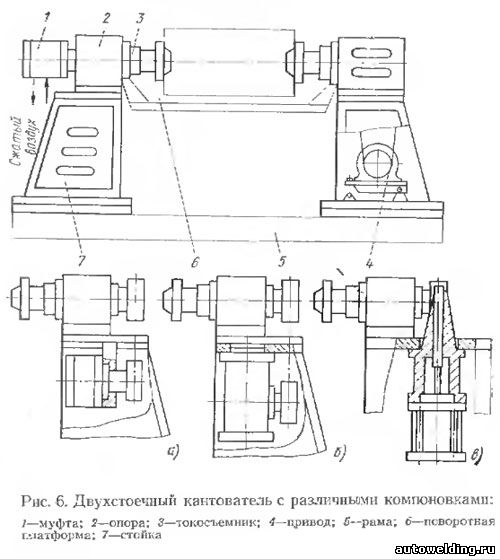
Типовая конструкция сварочного двухстоечного кантователя с различными компоновками привода показана на рис. 6, а — в, а пневматические схемы привода даны на рис. 19. 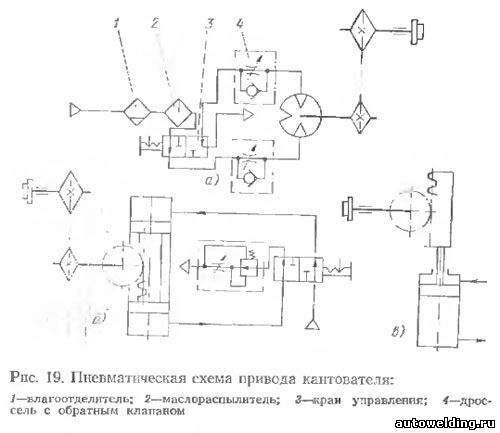
По конструктивному исполнению пневматические приводы делят на три типа: 1) с неполноповоротным пневмомотором и приводной звездочкой на конце штока (рис. 19,a); 2) с цилиндром двустороннего действия со встроенной в его среднюю часть реечной передачей (рис. 19,б); 3) с силовым органом, состоящим из цилиндра одностороннего действия и реечной передачи (рис. 19, в). Пневматические приводы имеют ряд недостатков: не обеспечивается плавность поворота, большие габаритные размеры силового органа (при необходимости создать значительные усилия), чувствительность к падению давления в воздушной сети и к влажности сжатого воздуха. Для обеспечения плавного перемещения поршня в начале его хода в пневматическую схему введен регулируемый дроссель с обратным клапаном (рис. 19, а), который создает дополнительное сопротивление в нерабочей полости цилиндра. Та же цель достигается установкой дросселя (без обратного клапана) после крана управления в магистрали сброса воздуха в атмосферу (рис. 19, б), постановкой демпферов на штоке или в крышках цилиндров. Наиболее часто применяют механизмы поворота с гидроприводом. Их преимущество — легкость создания больших крутящих моментов, необходимых при повороте тяжелых узлов. Наибольшее распространение благодаря своей простоте и надежности нашли механизмы поворота кантователей с электромеханическим приводом. Для вращения поворотной платформы манипулятора часто используют электродвигатели постоянного тока, позволяющие регулировать число оборотов для обеспечения заданной скорости сварки. Подъем же стола и его наклон осуществляется от асинхронных электродвигателей. Основными параметрами манипуляторов являются грузоподъемность и крутящие моменты относительно оси вращения и опорной плоскости планшайбы. Манипулятор подбирают по трем параметрам свариваемого изделия: по весу, расстоянию от центра тяжести до опорной плоскости планшайбы и от центра тяжести до оси вращения. По весу свариваемых изделий устанавливают грузоподъемность манипулятора, а затем определяют значения крутящих моментов по формулам Mo=Gρ; Mп=GH, где Mo — момент относительно оси вращения, кгс*м; Mп — момент относительно опорной плоскости планшайбы, кгс*м; G — вес свариваемого изделия, кгс; ρ — расстояние от центра тяжести изделия до оси вращения, м; Н — расстояние (высота) от центра тяжести изделия до плоскости планшайбы, м. Если свариваемое изделие крепится через промежуточное приспособление, то вес свариваемого изделия должен быть принят с учетом веса приспособления, а величина H должна быть принята с учетом его высоты. Полученные расчетные значения моментов не должны превышать величины допускаемых моментов, указанных в паспорте манипулятора или типаже. Из рис. 20 видно, что с удалением центра тяжести от поверхности планшайбы (по оси X) или с удалением центра тяжести от оси вращения (по оси У) допускаемый вес изделия уменьшается. 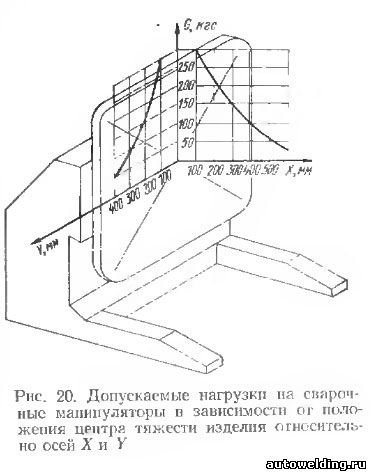
Манипуляторы обычно имеют плавно регулируемую скорость вращения планшайбы в широком диапазоне, так как свариваемые на них узлы могут быть разного диаметра к могут иметь разные толщину и катет шва. Частота вращения n планшайбы (об/мин) манипуляторов может быть определена по формуле 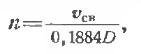
где Vсв — скорость сварки, м/ч; D — диаметр кругового шва, мм. Стабильность заданной скорости сварки обеспечивается системой обратной связи с тахогенератором, соединенным с электродвигателем набором шестерен. Выбор минимального по мощности привода и повышение его эксплуатационной надежности существенно зависит от конструкции манипулятора с закрепленным на его поворотной платформе изделием. Для уменьшения влияния на механизм привода инерционных масс конструкция манипулятора должна обеспечивать минимальное смещение центра тяжести всей поворотной системы, причем в момент включения привода инерционные силы могут быть значительными, поэтому их следует учитывать при выборе мощности привода (при расчетах передачи на прочность). Устранение влияния инерционных сил достигается совмещением центра тяжести вращающихся масс с осью вращения, рациональным размещением на поворотной платформе свариваемого изделия либо постановкой противовесов. В качестве предохранительного звена в конструкции манипулятора должен быть предусмотрен срезывающийся палец. Расчет механического привода манипулятора в зависимости от принятой конструктивной схемы приведен в табл. 3. 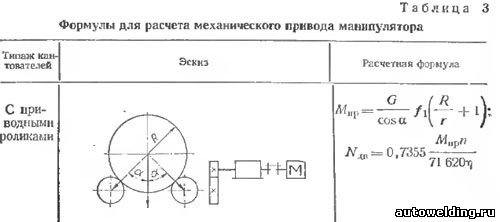
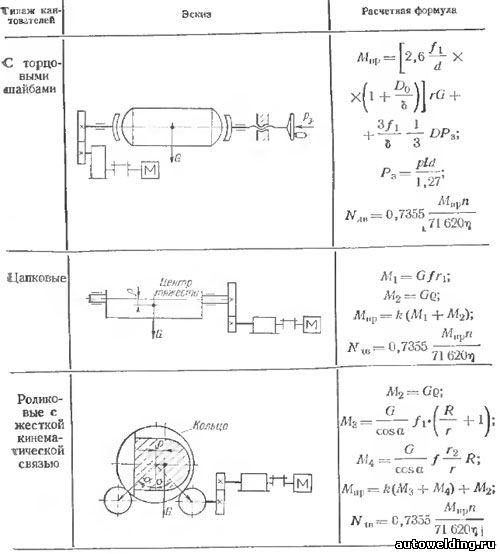
В формулах: Mпр — приведенный момент манипулятора, кгс * см; М1 — момент трения скольжения, кгс * см; M2 — момент, необходимый для преодоления статической неуравновешенности вращающейся платформы с изделием, кгс * см; M3 — суммарный момент от трения качения роликов по бандажам колец относительно оси колец, кгс * см; M4 — момент трения скольжения на цапфах роликов относительно оси колец, кгс * см; G — вес изделия, кгс; R — радиус изделия (кольца), см; г —радиус ролика, см; r1 — радиус цапфы, см; r2 — радиус цапфы роликов, см; Q — расстояние от центра тяжести вращающихся частей до оси цапф манипулятора (до оси колец), см; Pв — осевая сила зажатия изделия, кгс: p — допустимое давление, кгс/см2 (сталь по стали 130—200, сталь по бронзе 60—90, сталь по чугуну 15—25); n — частота вращения изделия, об/мин; l — длина цапфы, см; D — средний диаметр беговой дорожки шариков упорного подшипника, см; D0 — диаметр внутреннего кольца радиального подшипника, см; d — диаметр цапфы, см; δ — диаметр шарика, см; f1—коэффициент трения качения; f—коэффициент трения скольжения; k — коэффициент, учитывающий инерционные силы, k=1.2÷1,3; α — угол наклона роликов, град; η— КПД всех передаточных звеньев от электродвигателя к изделию.
|