Газы и аппаратура для кислородной резки
Кислород и горючие газыДля резки должен применяться кислород возможно более высокой чистоты. Практически применяют кислород чистотой 98,5—99,5%. Чем выше чистота кислорода, тем резка протекает быстрее, а расход кислорода меньше. Для подогрева изделия при резке широко применяют горючие газы — заменители ацетилена. В первую очередь используются: коксовый, природный, нефтяной и паролизный газы, пропан, пары керосина. При использовании газов-заменителей расход их через резак можно определить, зная коэффициент замены ацетилена. Значения этого коэффициента принимаются равными: для метана и природного газа 1,5, для городского газа 1,8, для пропана 0,6. Сечения каналов в резаках для газов-заменителей рассчитывают по допустимому расходу газа через мундштук, пользуясь нормами, приведенными в табл. 70. 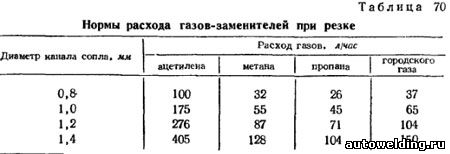
РезакиРезак представляет собой горелку для кислородной резки металлов. Схема резака изображена на рис. 165, а. Он имеет рукоятку 9 и корпус 10, в который вставлена смесительная камера 14, присоединяемая к корпусу накидной гайкой 13. В смесительную камеру ввернуто сопло инжектора 12. Ацетилен поступает в резак по шланговому ниппелю 8, а кислород — по ниппелю 7. 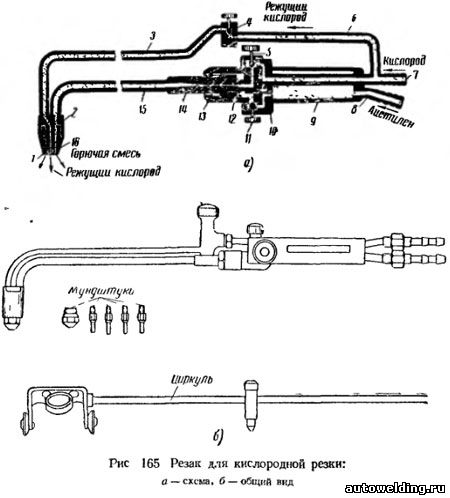
Кислород, поступающий через ниппель 7, идет по двум направлениям: часть его, используемая для подогревающего пламени и регулируемая вентилем 5, поступает в центральный канал инжектора 12, подсасывая ацетилен, количество которого регулируется вентилем 11. Из смесительной камеры горючая смесь по трубке 15 проходит в головку 2 резака, а затем, выходя через зазор между наружным мундштуком 16 и внутренним 1, сгорает, образуя подогревающее пламя. Другая часть кислорода проходит по трубке 6 через вентиль 4 и далее по трубке 3 также поступает в головку 2 резака, откуда выходит через центральный канал внутреннего мундштука 1, образуя режущую струю кислорода. Регулирование давления кислорода и подбор мундштуков в зависимости от толщины разрезаемого металла производится до данным табл. 71. 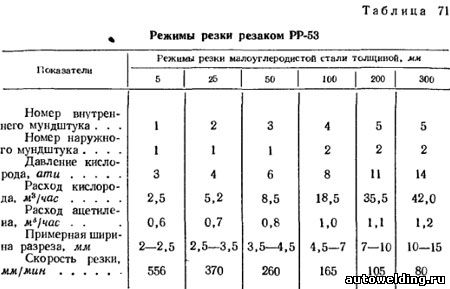
Давление ацетилена колеблется в пределах от 0,02 до 0,1 ати. Внешний вид резака РР-53 показан на рис. 165, б. КеросинорезыВ керосинорезах в качестве горючего используют керосин. Керосинорез К-51 (рис. 166) состоит из резака, бачка для жидкого горючего, шлангов, тележки и циркуля. Схема резака керосинореза изображена на рис. 167. Кислород через ниппель, вентиль 9 и инжектор 4 поступает в смесительную камеру головки 3. Здесь он смешивается с парами керосина или бензина, поступающими через второй ниппель и вентиль 7 в асбестовую набивку испарителя 11, в которой происходит испарение керосина под действием пламени вспомогательного мундштука 12. Горючая смесь выходит наружу через кольцевой зазор между мундштуками 1 и 2, образуя подогревающее пламя. Мощность и состав пламени регулируются вентилем 9 и маховичком 10, изменяющим положение инжектора в смесительной камере. Кислород проходит через вентиль 6 по трубке 5 в центральный канал мундштука 1. Для удобства работы резак снабжен рукояткой 8, в которой размещаются трубки для подвода керосина и кислорода. 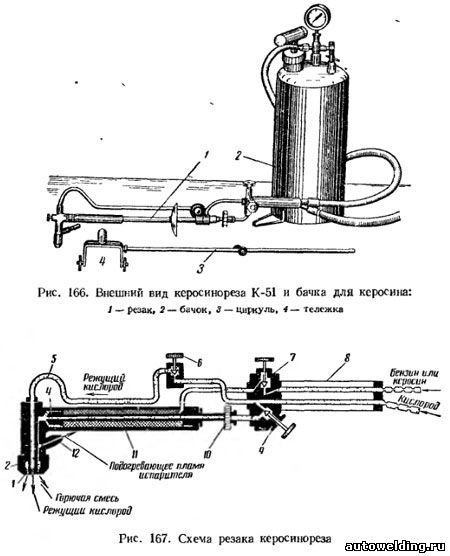
Керосин должен подаваться в резак под давлением 0,5—2 ати. Для этого служит бачок емкостью 5 л, снабженный ручным воздушным насосом, манометром и запорным вентилем. Режимы резки керосинорезом приведены в табл. 72. 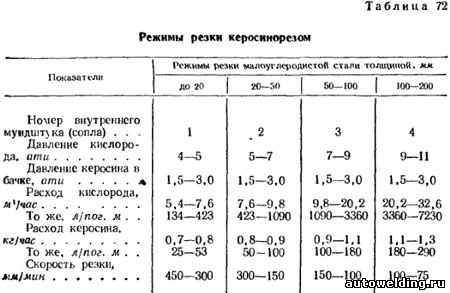
Для зажигания пламени керосина испаритель сначала нагревают паяльной лампой, горелкой или другим источником тепла. Предварительно в бачок насосом накачивают воздух до давления 2—2,5 ати, затем открывают вентиль подачи подогревающего кислорода и вентиль подачи горючего в резак, после чего регулируют подогревательное пламя, которое должно иметь правильную, слегка колоколообразную форму. При работе с керосинорезом нужно особенно следить за плотностью соединения мундштуков с головкой резака, а также за тем, чтобы не было пропусков газа и жидкости в местах соединений и в вентилях. При негерметичности соединений и вентилей резака керосинореза керосин может попасть в кислородный шланг, что приводит к обратному удару пламени в шланг и его взрыву. Для защиты кислородного шланга от обратных ударов пламени применяются обратные клапаны с теплопоглотителем из мелкой латунной сетки, устанавливаемые на кислородном ниппеле керосинореза. Перед заливкой в бачок керосин необходимо фильтровать. Испаритель резака следует систематически разбирать и очищать от нагара, тщательно промывая в горячей воде асбестовую набивку испарителя. При этом не следует менять плотность набивки, так как иначе резак может работать неустойчиво. Сильно прогоревшую набивку необходимо заменять новой. Шланг для подачи жидкого горючего нужно хорошо закреплять на ниппелях резака и бачка, так как при срыве шланга керосин начнет вытекать сильной струей и может вспыхнуть. Нельзя применять в керосинорезах бензин вместо керосина, так как это может привести к вспышкам, обратным ударам и ожогам вследствие более высокой летучести паров бензина. В этом случае следует использовать резаки, специально рассчитанные для работы на бензине и имеющие иные размеры каналов в инжекторе и мундштуках, чем у керосинорезов. В настоящее время керосин используется также в горелках для сварки легкоплавких металлов, пайки и поверхностной закалки в качестве заменителя ацетилена. Принцип устройства и работы этих горелок такой же, как и у керосинореза, только в них отсутствуют вентили, трубки и каналы для режущего кислорода. В машинах для резки применяются керосинорезы с механическим распылением керосина струей кислорода и последующим испарением его в мундштуке головки. Глизманенко Д.Л. "Сварка и резка металлов"
|