Основные понятия о процессах обработки отверстий и режущем инструменте, используемом на сверлильных станках
Сверление, зенкерование и развертывание являются основными технологическими способами обработки резанием круглых отверстий различной степени точности и с различной шероховатостью обработанной поверхности. Все перечисленные способы относятся к осевой обработке, т.е. к лезвийной обработке с вращательным главным движением резания при постоянном радиусе его траектории и движении подачи только вдоль оси главного движения резания. Сверление — основной способ обработки отверстий в сплошном материале заготовок. Просверленные отверстия, как правило, не имеют абсолютно правильной цилиндрической формы. Их поперечное сечение имеет форму овала, а продольное — небольшую конусность. Диаметры просверленных отверстий всегда больше диаметра сверла, которым они обработаны. Разность диаметров сверла и просверленного им отверстия называют разбивкой отверстия. Для стандартных сверл диаметром 10...20 мм разбивка составляет 0,15...0,25 мм. Причиной разбивки отверстий являются недостаточная точность заточки сверл и несоосность сверла и шпинделя сверлильного станка. Сверление отверстий без дальнейшей их обработки проводят тогда, когда необходимая точность размеров лежит в пределах 12... 14-го квалитетов. Наиболее часто сверлением обрабатывают отверстия для болтовых соединений, а также отверстия для нарезания в них внутренней крепежной резьбы (например, метчиком). Зенкерование — это обработка предварительно просверленных отверстий или отверстий, изготовленных литьем и штамповкой, с целью получения более точных по форме и диаметру, чем при сверлении. Точность обработки цилиндрического отверстия после зенкерования — 10... 11-й квалитеты. Развертывание — это завершающая обработка просверленных и зенкерованных отверстий для получения точных по форме и диаметру цилиндрических отверстий (6...9-й квалитеты) с малой шероховатостью Ra 0,32... 1,25 мкм. Сверла предназначаются для сверления сквозных или глухих отверстий в деталях, обрабатываемых на сверлильных, токарно-револьверных и некоторых других станках. В зависимости от конструкции и назначения различают следующие сверла: 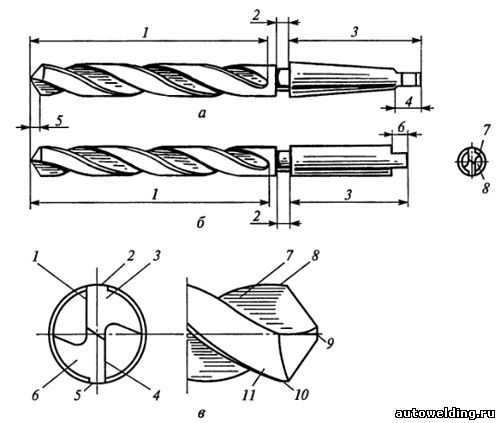
Рис. 2.22. Спиральные сверла: а и б — элементы спирального сверла соответственно с коническим и цилиндрическим хвостовиками; в — кромки и поверхности спирального сверла; 1 — рабочая часть; 2 — шейка; 3 — хвостовик; 4 — лапка; 5 — режущая часть; 6 — поводок; 7 — зуб; 8 — винтовая канавка; 9 — поперечная кромка; 10 — кромка ленточки; 11 — спинка зуба 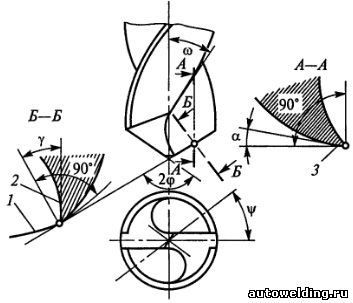
Рис. 2.23. Углы спирального сверла: α — задний угол; γ — передний угол; Ψ — угол наклона поперечной режущей кромки; ω — угол наклона винтовой канавки; 2φ — угол при вершине; 1 — задняя поверхность; 2 — передняя поверхность; 3 — режущая кромка 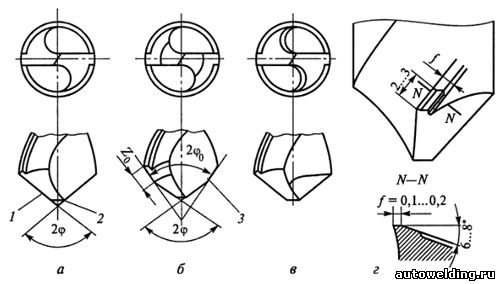
Рис. 2.24. Формы заточки спиральных сверл: а — обыкновенная; б — двойная: 1 — главная режущая кромка; 2 — поперечная режущая кромка; 3 — вспомогательная режущая кромка; 2φ — главный угол при вершине сверла; 2φ0 — вспомогательный угол при вершине сверла; Z0 — ширина зоны второй заточки; в — подточка поперечного лезвия и ленточки; г — подточка ленточки: f — ширина ленточки - спиральные с цилиндрическим и коническим хвостовиками, предназначенные для сверления стали, чугуна и других конструкционных материалов;
- оснащенные пластинками из твердых сплавов, предназначенные для обработки деталей из чугуна (особенно с литейной коркой) и очень твердой и закаленной стали;
- глубокого сверления (одно- и двустороннего резания), используемые при сверлении отверстий, длина которых превышает диаметр в пять раз и более;
- центровочный инструмент (центровочные сверла и зенковки), предназначенный для обработки центровых отверстий обрабатываемых деталей.
Спиральное сверло и элементы его рабочей части приведены на рис. 2.22. Углы и формы заточки спирального сверла показаны на рис. 2.23 и 2.24. Формы заточек сверл выбирают в зависимости от свойств обрабатываемых материалов и диаметра сверла. Для повышения стойкости сверла и производительности обработки производят двойную заточку сверла под углами 2φ = 116...118° и 2φ0 = 70...90° (рис. 2.24, б).Подточка поперечной кромки (рис. 2.24, в) и ленточки сверла (рис. 2.24, г) облегчает процесс сверления отверстий. Подточка поперечной кромки снижает осевую силу, а подточка ленточки уменьшает трение ленточек о стенки отверстия и повышает стойкость сверл. При подточке длина поперечной кромки уменьшается до 50 %. Обычно производится подточка сверл диаметром более 12 мм, а также после каждой переточки сверла. В зависимости от обрабатываемого материала углы при вершине сверл выбирают по табл. 2.10, а задние и передние углы — по табл. 2.11. Для сверления заготовок из чугуна и цветных металлов применяют твердосплавные сверла. Эти сверла из-за нестабильности работы редко применяют при сверлении заготовок из сталей. Сверла диаметром от 5 до 30 мм оснащают пластинами или коронками из твердого сплава. Недостатками конструкции сверл с припаиваемой пластиной из твердого сплава являются ослабление корпуса инструмента и расположение места, где припаивается пластина, в зоне резания, т. е. в зоне высоких температур. Сверла с припаянными встык коронками из твердого сплава лишены этих недостатков. Таблица 2.10. Углы при вершине сверла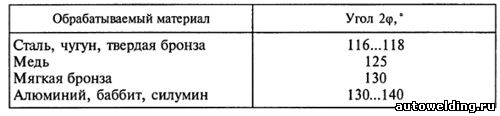
Таблица 2.11. Задние и передние углы сверла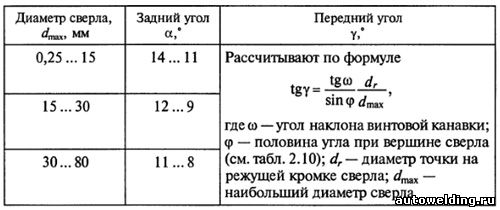
Примечания. 1. Задние углы даны для точек режущей кромки, расположенных на наибольшем диаметре сверла dmax. 2. При расчете угла γ принимают dr= dmax. Для успешной работы твердосплавных сверл необходимо обеспечить их повышенную прочность и жесткость по сравнению со сверлами из быстрорежущей стали, это достигается увеличением сердцевины до 0,25 диаметра сверла. Зенкеры предназначены для обработки литых, штампованных и предварительно просверленных цилиндрических отверстий с целью улучшения чистоты поверхности и повышения их точности или для подготовки их к дальнейшему развертыванию. Зенкеры применяют для окончательной обработки отверстий с допуском по 11... 12-му квалитетам и обеспечивают параметр шероховатости Rz 20...40 мкм. Конструктивно зенкеры выполняют хвостовыми цельными, хвостовыми сборными с вставными ножами, насадными цельными и насадными сборными. Зенкеры изготовляют из быстрорежущей стали или с пластинами твердого сплава, напаиваемыми на корпус зенкера или корпус ножей у сборных конструкций. Хвостовые зенкеры (подобно сверлам) крепят с помощью цилиндрических или конических хвостовиков, насадные зенкеры имеют коническое посадочное отверстие (конусность 1:30) и торцовую шпонку для предохранения от провертывания при работе. Зенкер (рис. 2.25, а) состоит из рабочей части l, шейки l3, хвостовика l4 и лапки е. Рабочая часть зенкера имеет режущую l1 и калибрующую l2 части. Зенкеры имеют три, четыре, а иногда шесть режущих зубьев, что способствует лучшему по сравнению со сверлами направлению их в обрабатываемом отверстии и повышает точность обработки. 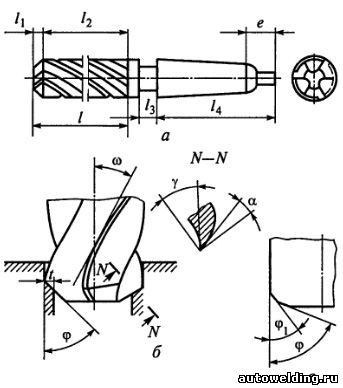
Рис. 2.25. Зенкер: а — элементы зенкера: l — рабочая часть; l1 — режущая часть; l2 — калибрующая часть; l3 — шейка; l4 — хвостовик; е — лапка; б — режущая часть зенкера: α — задний угол; γ — передний угол; φ — угол главной режущей кромки; ω — угол наклона канавки зенкера; t — глубина резания; b — режущая кромка: φ1 — угол вспомогательной режущей кромки Зенкеры из быстрорежущей стали изготовляют хвостовыми цельными диаметром 10...40 мм, хвостовыми сборными с вставными ножами диаметром 32...80 мм или насадными сборными диаметром 40... 120 мм. Зенкеры, оснащенные твердосплавными пластинами, могут быть составными и сборными. Составные хвостовые зенкеры имеют диаметры 14...50 мм, насадные — 32...80 мм, насадные сборные — 40... 120 мм. Таблица 2.12. Передние углы зенкеров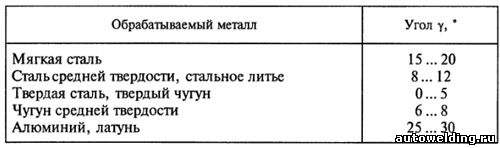
Угол наклона винтовой канавки (рис. 2.25, б) зенкеров общего назначения ω = 10...30°. Для обработки твердых металлов берут меньшие, а для мягких — большие значения углов. Для чугуна угол ω= 0°. Для отверстий с прерывистыми стенками независимо от свойств обрабатываемого металла ω= 20...30°. Передний угол зенкеров у выбирают по табл. 2.12. Задний угол α зенкера на периферии равен 8... 10°. Угол при вершине φ выбирают по табл. 2.13. Таблица 2.13. Угол режущей части (заборного конуса) зенкера
Угол наклона винтовой канавки ω зенкера при обработке деталей из стали, чугуна и бронзы равен 0°. Для усиления режущей кромки на зенкерах с пластинками из твердых сплавов со выбирают положительным и равным 12... 15°. Ленточки вдоль края винтовой канавки на калибрующей части служат для направления зенкера. Ширина ленточки f= 0,8... 2,0 мм. Для повышения стойкости зенкера длину ленточки подтачивают на 1,5...2 мм (так же, как у сверла). Развертка — осевой режущий инструмент — предназначена для предварительной и окончательной обработки отверстий с точностью, соответствующей 6... 11-му квалитетам, и шероховатостью поверхности Ra 2,5 ...0,32 мкм. Основные элементы развертки даны на рис. 2.26, а. Развертки подразделяются: - по типу обрабатываемых поверхностей — на цилиндрические и конические;
- способу применения — на ручные и машинные;
- методу крепления на станке — на хвостовые и насадные;
- инструментальному материалу режущей части — на быстрорежущие и оснащенные твердым сплавом;
- конструктивным признакам — на цельные, изготовленные из одного инструментального материала; составные неразъемные со сварными хвостовиками; составные неразъемные с припаянными пластинками из твердого сплава и составные разъемные с вставными ножами.
Конструкция регулируемых разверток позволяет восстанавливать их диаметр при переточках, что увеличивает срок работы инструмента. Стандартные развертки имеют прямые канавки, т.е. угол наклона канавок ω = 0°. Для уменьшения шероховатости обработанной поверхности, а также для развертывания отверстий с пазами применяют развертки с винтовыми канавками, имеющими наклон, обратный направлению рабочего вращения. Для разверток с винтовыми канавками угол ω приведен в табл 2.14. Таблица 2.14. Угол наклона ω для разверток с винтовыми канавками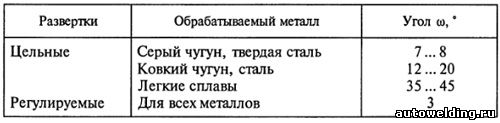
Угол конуса заборной части φ развертки (рис. 2.26, б) выбирают по табл. 2.15. Таблица 2.15. Угол конуса заборной части разверток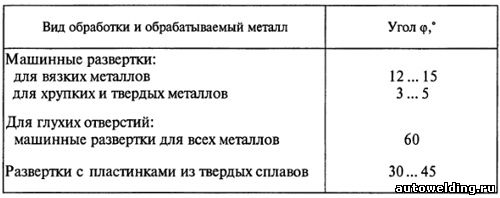
Задний угол α (рис. 2.26, в) берется равным 15°, большие величины а принимают для разверток малых размеров. Задний угол на калибрующей части равен 0°. 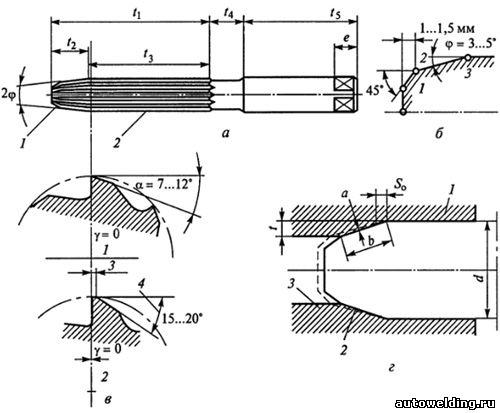
Рис. 2.26. Развертка: а — элементы развертки: t1 — рабочая часть; t2 — режущая часть; t3— калибрующая часть; t4 — шейка; t5 — хвостовик; е — квадрат; 1 — направляющий конус; 2 — цилиндрическая часть; 2φ — угол заборного конуса; б — элементы режущей части развертки: 1 — 2 — поверхность направляющего конуса; 2 — 3 — режущая часть; φ — угол главной режущей кромки; в — зубья развертки в поперечном сечении: 1 — режущая часть; 2 — калибрующая часть; 3 — ленточка; 4 — угол спинки; α — задний угол; γ — передний угол; г — элементы резания разверткой и обозначение поверхностей на обрабатываемой детали: t — глубина резания; а — толщина стружки; b — ширина стружки; S0 — подача на оборот; d — диаметр развернутой поверхности; 1 — развернутая поверхность; 2 — поверхность резания; 3 — развертываемая поверхность Для чистовых разверток при резании хрупких металлов передний угол γ равен 0° (см. рис. 2.26, в), для черновых — γ = 8°, у котельных разверток γ= 12... 15°, у разверток с пластинами из твердых сплавов γ берется от 0 до -5°. Метчики предназначены для образования резьбы в отверстиях. Рассмотрим метчики, образующие профиль резьбы путем снятия стружки и установленные на сверлильных, токарно-револьверных и других станках. Конструктивные элементы и профиль резьбы метчика показаны на рис. 2.27. 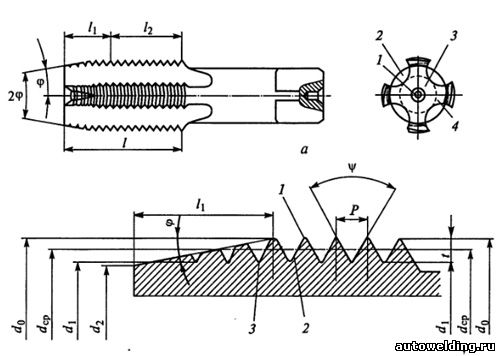
Рис. 2.27. Конструктивные элементы и профиль резьбы метчика: а — основные части: l1 — режущая часть; l2 — направляющая часть; l — рабочая часть; 1 — центровые отверстия; 2 — канавки; 3 — сердцевина; 4 — зуб; 2φ — угол конуса режущей части; φ — угол конуса; б — профиль резьбы: 1 — вершина резьбы; 2 — профиль резьбы; 3 — основание резьбы; Р — шаг резьбы; ψ — угол резьбы; t — глубина резьбы; d1 — внутренний диаметр; dср — средний диаметр; d0 — наружный диаметр; d2 — диаметр сердцевины; φ — угол конуса Стружечные канавки, пересекая резьбовые витки, образуют зубья метчика; каждый зуб представляет собой многониточный резьбовой резец. Резцы режущей части имеют главные кромки, которые располагаются на конусе, и вспомогательные кромки, которые являются частью резьбового профиля. Число резцов z1 режущей части определяется по формуле Z1 = l1z/P, где l1 — длина режущей части, мм; z — число зубьев метчика; Р — шаг резьбы, мм. Направляющая часть l2 в резании не участвует, а служит для самоподачи (ввинчивания) метчика и является резервом при переточках. Для уменьшения трения и устранения защемления резьбовых витков на направляющей части метчика резьбу выполняют с обратной конусностью, т.е. диаметры d, dср и d1 измеренные у хвостовика, на 0,02...0,005 мм меньше одноименных диаметров на режущей части (рис. 2.27, б). Для облегчения входа метчика в отверстие под резьбу диаметр d2 переднего торца метчика на 0,1... 0,3 мм меньше внутреннего диаметра резьбы d1 Величину угла в плане φ рассчитывают по формуле tgφ = (d - d1)/(2l1). Углы зубьев режущей l1 и направляющей l2 частей метчика (см. рис. 2.27, а) показаны на рис. 2.28. По способу получения задних поверхностей метчики относятся к затылованному инструменту. 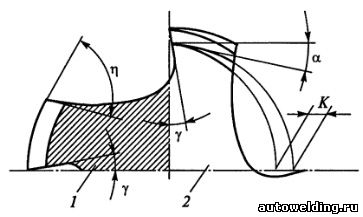
Рис. 2.28. Углы зубьев режущей и направляющей частей метчика: 1 — направляющая часть; 2 — режущая часть; γ — передний угол; η — задний угол; α — задний угол; К — величина падения затылка Задний угол а режущей части измеряют в плоскости, перпендикулярной оси вращения метчика, между касательными к окружности и задней поверхности. Метчики из быстрорежущей стали изготовляют со шлифованным профилем резьбы, метчики из углеродистой стали делают без шлифования профиля резьбы. Передние углы режущей и направляющей частей измеряют в плоскости, перпендикулярной оси вращения метчика между касательной к передней поверхности и прямой, проходящей через ось вращения и рассматриваемую точку кромки метчика. Б.И. Черпаков, Т.А. Альперович. "Металлорежущие станки".
|