Применение роботов
Промышленным роботом называют автоматический манипулятор с программным управлением. Несмотря на сложное устройство, робот достаточно прост в управлении. Дело в том, что программирование робота осуществляют «обучением» на основе приемов ручного труда. Благодаря универсальности и высокой производительности промышленные роботы по эффективности нередко не уступают специализированным автоматам, но в отличие от них могут переходить от одной работы к другой простой сменой программ. Применение роботов может быть выгодно и в крупносерийном производстве и в условиях частой смены вида выпускаемой продукции, т, е. в серийном и мелкосерийном производстве. Робот может заменить рабочего, особенно на однообразных операциях. В отличие от человека он не утомляется, не совершает субъективных ошибок и способен развивать большие усилия. В итоге повышается однородность качества изделий, возможно ускорение процесса производства переходом на непрерывную круглосуточную работу. В сварочном производстве за рубежом наибольшее применение получили роботы, перемещающие клещи контактной сварки. Для выполнения таких операций используют механизмы с пятью (и более) степенями подвижности и относительно простую позиционную систему управления, задающую только координаты точек, где требуется осуществить сварку. Характерным примером оборудования такого назначения является робот типа «Unimate», выпускаемый в США и в других странах. Внешний вид робота с таблицей степеней подвижности, направлений отдельных перемещений и скоростей движения показан на рис. 13.44, а схема основных исполнительных механизмов — на рис. 13.45. Вал 3 вращает поперечину 1 вокруг вертикальной оси с помощью гидроцилиндров 6 и пары рейка — шестерня 2, 4. Поворот поперечины вокруг горизонтальной оси задается гидроцилиндром 5, закрепленным на валу 3. Поступательное перемещение «руки» осуществляет гидро-цилиндр 8. Наклон «кисти» 7 относительно оси 10 и вращение площадки 11 для крепления инструмента вокруг оси 12 обеспечиваются системой гидроцилиндров и зубчатых колес, расположенных в «кисти» и в цилиндрических штоках 9. 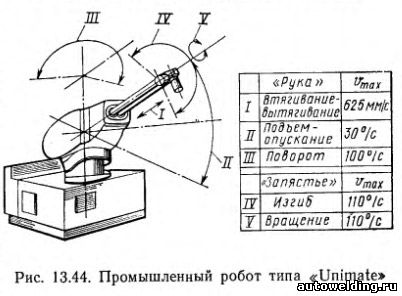
Работе предшествует «обучение» робота. Для этого опытный рабочий на первом узле последовательно перемещает инструмент от одного рабочего положения к другому, вводя координаты каждой из этих точек в запоминающее устройство нажатием кнопки «Память». Если на пути между соседними свариваемыми точками оказывается препятствие, например элементы зажимного приспособления, то в память робота вводят кородинаты дополнительных точек, определяющих траекторию движения инструмента в обход препятствия, Выполнение программы начинается после того, как собираемый или свариваемый узел займет требуемое исходное положение и сигнал об этом поступит в запоминающее устройство. По каждой степени подвижности перемещение задается гидроцилиндром с управляющим сервоклапаном. Каждый гидроцилиндр имеет детектор положения, связанный с запоминающим устройством. Орган сравнения, в который поступают сигналы команд и сигналы детекторов положения, по значению их разности управляет перемещением штоков гидроцилиндров, пока рабочий орган не займет положения, заданного программой. Затем дается сигнал на включение инструмента. Окончание сварочной операции служит, в свою очередь, сигналом для дальнейшего движения инструмента к месту выполнения следующей операции. Существенным достоинством робота является возможность быстрой смены программ, хранящихся в памяти машины. В зависимости от характера выполняемой операции на руке робота могут быть закреплены клещи для контактной сварки, сварочная головка для дуговой сварки, захватное устройство. При контактной точечной сварке робот быстро перемещает значительную массу сварочных клещей от одной точки к Другой; при этом возникают большие инерционные нагрузки. Напротив, условия работы промышленного робота при дуговой сварке облегчаются сравнительно малой массой сварочной головки (3—5 кг) и плавным режимом движения со скоростью 3—50 мм/с. С другой стороны, используемая при контактной сварке относительно простая позиционная система управления не может обеспечить перемещение инструмента по непрерывной траектории с заданной скоростью движения, т. е. оказывается непригодной для выполнения таких технологических операций, как тепловая резка, дуговая сварка и т. д. Несмотря на кажущуюся простоту, движения сварщика представляют собой сложный комплекс пространственных перемещений, зависящих как от конфигурации свариваемых деталей, так и от технологических особенностей процесса сварки. Операции такого рода требуют использования более сложной многопозиционной или контурной системы управления, позволяющей непрерывно управлять как перемещением, так и его производными по времени. 
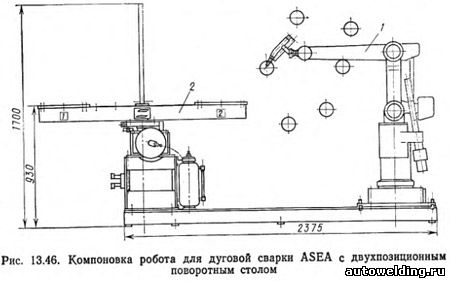
Примером робота такого типа может служить робот ASEA (рис. 13.46). Использование электропривода в сочетании с жесткой механической конструкцией обеспечивает малую погрешность позиционирования (±0,2 мм). Система управления позволяет программировать кривые траектории движения при различных скоростях. При этом кривая разбивается на ряд прямолинейных участков, число которых выбирают, исходя из требуемой точности. В процессе программирования исполнительный орган вручную последовательно устанавливают в требуемые положения и нажатием кнопки на панели управления координаты фиксируются в памяти машины. Затем в промежутках между зарегистрированными позициями вводят такие параметры, как скорость движения, ускорение, продолжительность остановки, а также параметры сварочного процесса. При использовании таких роботов в серийном и мелкосерийном производстве для позиционирования деталей целесообразно использовать два манипулятора или поворотный стол 2 с двумя приспособлениями для сборки. В то время как робот 1 занят сваркой изделия на одной позиции, оператор имеет возможность подготовить к сварке узел на другой позиции. При дуговой сварке в ряде случаев целесообразно разделять функции между механизмами перемещения сварочной головки и манипулятором, служащим для перемещения свариваемого изделия. При этом оба устройства работают совместно по единой программе. Такой прием позволяет не только упростить кинематику « уменьшить число степеней подвижности самого робота, но и снизить требования к системе управления. Схема подобного устройства показана па рис. 13.47. Простая схема робота портального типа обеспечивает программируемое перемещение сварочной головки 1 по трем взаимно перпендикулярным направлениям х—х, у—у, z—z и установочное вращение и наклон ее относительно вертикальной оси. Манипулятор 2, на столике которого закрепляется деталь, позволяет устанавливать ее или вращать по программе относительно осей а—а и b—b. 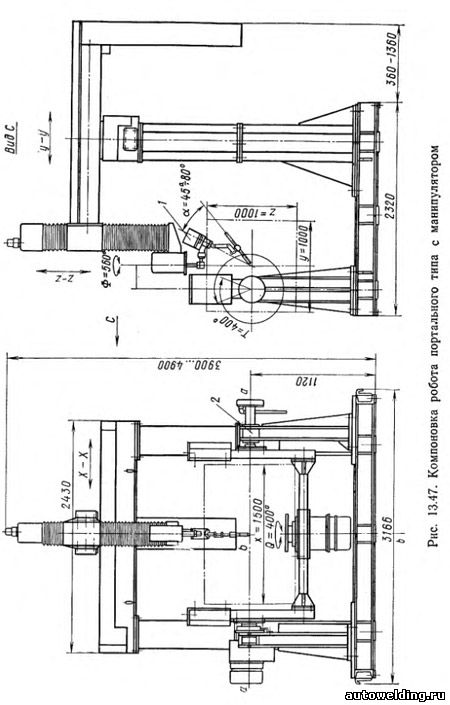
Надо иметь и виду, что робот может обеспечить стабильно высокое качество выполнения соединений только при отсутствии существенных отклонений размеров и формы свариваемых элементов. Поскольку такие отклонения все же неизбежны, то наличие жесткой программы является существенным недостатком роботов первого поколения. Предполагается, что роботы второго поколения будут оборудованы системами обратной связи, с помощью которых рабочая программа будет автоматически корректироваться при изменении положения изделия или его отдельных элементов. Кроме того, широкому внедрению роботов в сварочное производство будет способствовать решение ряда специфических сварочных задач. Однако создание роботов второго поколения вряд ли вытеснит роботов первого поколения, более дешевых и простых. Возможности использования промышленных роботов в сварочном производстве не исчерпываются операциями контактной и дуговой сварки. Не менее важно использовать их для загрузки и разгрузки автоматически действующих установок, а также при сборке. В этом случае на «руке» робота устанавливают захватное устройство. С помощью этого устройства робот захватывает детали из положения, заданного при базировании, исключая смещение их в процессе транспортирования, ориентирует и подает детали на сборку, освобождая их после установки в требуемое положение. Источник: Николаев Г.А. "Сварные конструкции. Технология изготовления. Автоматизация производства и проектирование сварных конструкций" Читайте также:
|