Электроды для рельефной сварки
При рельефной сварке применяют электроды с плоской рабочей поверхностью, размеры которой обычно превышают размеры сварного соединения. Поэтому площадь соприкосновения электродов с деталями при рельефной сварке несколько больше, а плотность тока и давление в контакте — меньше, чем при точечной сварке. Это улучшает условия работы электродов и приводит к тому, что при одинаковой интенсивности охлаждения их стойкость при рельефной сварке выше, чем при точечной. Некоторые авторы ставят под сомнение тезис о высокой стойкости электродов при рельефной сварке. В производственных условиях без переточки электродов на рельефных машинах сваривают не более 1000—1500 соединений, что не лучше аналогичных показателей при точечной сварке. В большинстве случаев причиной относительно невысокой стойкости электродов является их недостаточное охлаждение. Обеспечить при рельефной сварке такие же условия охлаждения электродов, что и при точечной, не всегда удается из-за сложности электродных устройств. Однако при рациональной конструкции электродного приспособления, обеспечивающей достаточную интенсивность охлаждения электродов, их стойкость может быть весьма высокой. Так, при рельефной сварке сепараторов шарикоподшипников в приспособлении с электродами, аналогичными точечным (см. рис. 85), число сепараторов, свариваемых без переточки электродов, достигает 20 000. 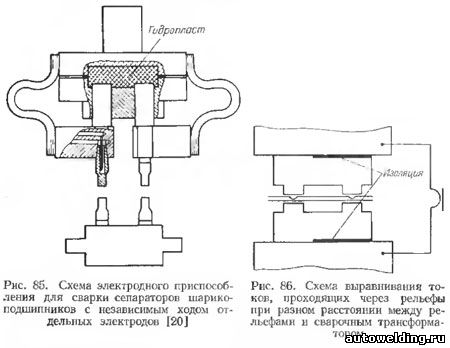
Все разновидности электродов можно разделить на три основные группы. Первую группу составляют электроды для индивидуальной рельефной сварки, применяемые при сварке одного рельефа в листовых нахлесточных соединениях или при Т-образной приварке одной детали. Ко второй группе относятся электроды, предназначенные для групповой рельефной сварки, преимущественно нахлесточных соединений. Наконец, к третьей группе можно отнести электроды, обеспечивающие подвод тока к боковым поверхностям привариваемых деталей при некоторых разновидностях Т-образной сварки. Электроды первой группы конструктивно близки к электродам для точечной сварки. В простейшем случае они представляют собой обычные цилиндрические электроды с плоской рабочей поверхностью увеличенного диаметра (рис. 80, а). Такие электроды предусмотрены ГОСТ 14111—69. Они могут успешно применяться для сварки не только одного, но и нескольких рельефов при их кучном расположении. 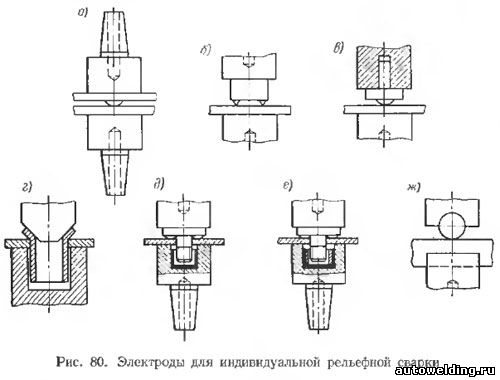
Электроды с плоской рабочей поверхностью можно использовать также во многих случаях Т-образной сварки, например при приварке к листам бонок, гаек, коротких стержней и других деталей ограниченной длины, подвод тока к которым производится со стороны их торцовой поверхности (рис. 80, б). В более сложных случаях в одном или обоих электродах делают отверстия для размещения в них выступающих частей привариваемой детали (рис. 80, в—е). Если привариваемая деталь, контактирующая с одним электродом, располагается в отверстии второго, то для предотвращения шунтирования тока в это отверстие запрессовывают изолирующую втулку (рис. 80, Для предохранения изоляции от быстрого износа в отверстие электрода нередко запрессовывают также вторую втулку — стальную (рис. 80, е). При малых размерах привариваемой детали один из электродов может одновременно выполнять функции приспособления для установки детали в положение перед сваркой. С этой целью на поверхности электрода могут быть закреплены упорные штыри, пластинки и другие устройства, ограничивающие и фиксирующие положение деталей в пространстве. При приварке труб с развальцовкой используют электроды с конусной поверхностью, расположенной под углом 45° к продольной оси (рис. 80, г). Электроды первой группы применяют также при сварке труб и стержней вкрест (рис. 80, ж). В этом случае на рабочей поверхности электродов делают выемку с цилиндрической поверхностью радиусом, равным радиусу свариваемых стержней (труб). Глубина выемки должна быть несколько меньше радиуса стержня. Такие электроды совмещают функции подвода тока и передачи усилия с функциями фиксации деталей. В том случае, если точная фиксация стержней по отношению друг к другу не является обязательной, а требования к чистоте их поверхностей невысоки, сварку стержней вкрест можно производить, применяя электроды с плоской рабочей поверхностью, не имеющей выемок. Центральная и посадочная части электродов первой группы, как правило, не отличаются от соответствующих частей электродов для точечной сварки. Электроды первой группы устанавливают в электродержателях с помощью конусной посадки, реже на резьбе. В большинстве случаев эти электроды могут быть установлены в стандартных электродержателях обычных точечных машин. Водяное охлаждение электродов первой группы осуществляется так же, как электродов для точечной сварки. Электроды, применяемые для одновременной сварки нескольких рельефов, имеют иную конструкцию. В простейшем случае для этой цели можно использовать плиты с плоской рабочей поверхностью (рис. 81, а). Однако такое решение чаще всего оказывается нерациональным. В связи с ограниченной площадью контакта с деталями износ электродов при рельефной сварке имеет местный характер. Обычно он начинается с образования углублений на поверхности электрода, противолежащего детали с рельефами. Для устранения вмятин необходима обработка всей поверхности электродной плиты, что влечет за собой значительный расход материала. Кроме того, при применении плит со сплошной рабочей поверхностью возрастает опасность шунтирования тока по заусенцам и выступающим участкам деталей, находящимся между рельефами. 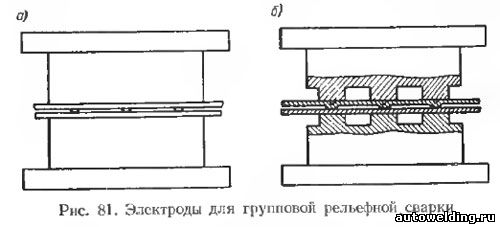
Вероятность шунтирования тока может быть уменьшена при использовании плит с выступающими частями, соответствующими расположению рельефов на деталях (рис. 81, б). Однако наиболее целесообразно применение составных электродов, состоящих из основания и сменных электродных вставок. Основание изготавливают из материала с высокой электропроводностью, его конструкция должна обеспечить интенсивное водяное охлаждение с подводом охлаждающих каналов, по возможности ближе к электродным вставкам. Электродные вставки изготавливают из менее электропроводного, но более твердого материала. Применение такой конструкции приводит к резкому уменьшению износа электродов и расхода электродных материалов и к облегчению ухода за состоянием электродных поверхностей. Крепление электродных вставок в основаниях может осуществляться различными способами: запрессовкой (рис. 82, а, б); с помощью болтов (рис. 82, в); конической посадкой (рис. 82, г); посадкой типа ласточкина хвоста (рис. 82, д) резьбовой посадкой (рис. 82, е—ж) пайкой (рис. 82, з). Посадка типа ласточкина хвоста удобна при кучном расположении рельефов, когда одна вставка применяется для сварки нескольких рельефов одновременно. При резьбовом креплении вставок резьбу следует разгрузить от силовых нагрузок опорой на заплечики (рис. 82, е) с помощью стальной вставки (рис. 82, ж) или контргайки. При коническом креплении в качестве вставок можно использовать электроды первой группы с конической посадочной частью, аналогичные электродам точечных машин. 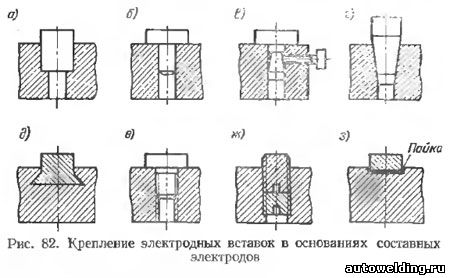
Распространенным способом крепления является припаивание электродных вставок к основанию твердым припоем (рис. 82, з). Для уменьшения потерь дорогостоящего материала вставок глубина выемок в основании не должна превышать 0,7—0,8 мм. Высоту вставок для уменьшения температуры их поверхности следует выбирать в пределах, не превышающих 0,3—0,5 от их диаметра. Вставки припаивают к основанию низкотемпературными серебряными припоями. Применение высокотемпературных припоев нерационально в связи с опасностью нагрева основания до температур, вызывающих его коробление и окисление. В случае применения массивных оснований электродные вставки удобнее припаивать к бронзовым переходникам, которые, в свою очередь, крепятся к основаниям с помощью винтов. Для зачистки поверхностей вставок переходники демонтируют и заменяют запасными, что требует минимальных затрат времени. Недостатком такой конструкции является появление лишнего контактного сопротивления и ухудшение отвода теплоты от вставок, приводящие к увеличению их нагрева. При жестком закреплении электродных устройств в контактных плитах параллельность рабочих поверхностей электродов после приложения сварочного усилия может нарушиться из-за деформации консолей сварочной машины. Этого можно избежать, применяя устройства с электродами, перемещающимися в общих направляющих, которые обеспечивают параллельность рабочих поверхностей электродов вне зависимости от деформации машины и нарушения параллельности ее плит. С одним вариантом такого устройства мы уже познакомились, рассматривая конструкцию машин типа МТК и МРК. На рис. 83 приведена схема электродного устройства, в котором параллельность электродных плит 4 обеспечивается направляющими колоннами 2, изолированными от нижнего основания 5 изолирующими втулками 1. Верхнее основание 3 либо вообще не должно быть связано с верхней контактной плитой машины (в этом случае при подъеме верхней контактной плиты электродные плиты 5, 3 раздвигаются под действием специальных пружин), либо должно иметь с плитой шарнирное сочленение. Электродные устройства такого типа могут устанавливаться на плитах любых рельефных машин. 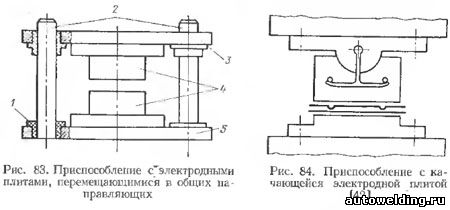
Сохранение параллельности рабочих поверхностей электродов еще не является гарантией равномерного распределения тока и усилия между отдельными рельефами. Распределение тока и усилия может оказаться неравномерным из-за неравенства высоты отдельных рельефов. Неравенство высоты рельефов меньше влияет на качество сварки при применении самоустанавливающихся электродных плит, закрепленных на цилиндрической или шаровой опоре. На рис. 84 показана схема приспособления с качающейся электродной плитой, используемого для одновременной сварки двух рельефов. Распределение давления тем равномерней, чем больше расстояние между свариваемыми рельефами и, следовательно, чем больше плечо силы сжатия. При сварке трех рельефов электроды целесообразно крепить на шаровой опоре. Если число одновременно свариваемых рельефов больше трех, применение шаровой опоры уже не может обеспечить их равномерное сжатие при отсутствии равенства hp. Наиболее равномерное распределение усилия между рельефами, не зависящее от параллельности электродных плит, износа электродов и неравенства высоты рельефов может быть достигнуто при применении электродных устройств с автономным ходом отдельных электродов, опирающихся на масло, гидропласт или индивидуальные пружины (рис. 85). Сварочный ток к электродам подводят с помощью гибких шин, один конец которых соединяется с электродным основанием. Для равномерного распределения усилия между рельефами достаточно, если устройство с независимым ходом электродов будет размещено с одной стороны свариваемого изделия. Электроды, расположенные с другой стороны, могут иметь жесткое закрепление. Электродные приспособления с плавающими электродами следует применять при сварке особо ответственных изделий, таких, как, например, сепараторы шарикоподшипников, а также во всех случаях групповой рельефной сварки, когда качество соединений должно быть особенно высоким. В отечественной промышленности такие приспособления еще не получили широкого распространения; кроме приспособлений, применяемых при сварке сепараторов шарикоподшипников, в литературе описано только одно приспособление с автономным ходом электродов — для рельефной сварки панели проигрывателя. Приспособления такого типа разрабатывались во ВНИИЭСО; имеются сведения о разработке ряда новых электродных приспособлений с автономным ходом электродов в ИЭС им. Патона. Распределение тока между отдельными рельефами зависит не только от степени их обжатия, но и от сопротивления контуров, образующихся при прохождении через рельефы сварочного тока. Поэтому в рельефах, находящихся дальше от сварочного трансформатора, протекают меньшие токи, чем в рельефах, расположенных ближе. Свариваемые изделия при групповой рельефной сварке следует располагать по возможности таким образом, чтобы различие в размерах и сопротивлении контуров разных рельефов было минимальным. При большой разнице в расстоянии между рельефами и трансформатором выравнивание токов облегчается при установке в основаниях приспособлений изолирующих прокладок, как показано на рис. 86. 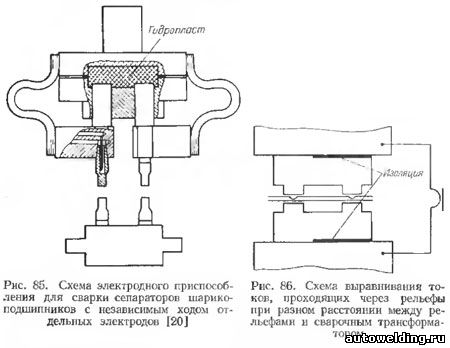
В рассмотренных типах электродов их рабочие поверхности служат одновременно для подвода тока к деталям и передачи на них сварочного усилия. В электродах третьей группы, применяемых при Т-образной сварке деталей типа стержней, труб и полос большой длины и малого сечения, эти функции, как правило, разделены. Подвод тока к торцовым поверхностям таких деталей может привести к их перегреву с последующей потерей формы, а потому нецелесообразен. Для снижения тепловых потерь в деталях и исключения их перегрева и деформации сварочный ток следует подводить к боковым поверхностям деталей в непосредственной близости от места сварки. Конструкции электродных устройств, осуществляющих боковой токоподвод, весьма разнообразны. В большинстве случаев ток подводят с разных сторон привариваемой детали, хотя при Т-образной сварке листов допустим односторонний токоподвод. Усилие зажатия развивается с помощью пневматических, пружинных или иных приводов. Устройства для бокового подвода тока не только подводят ток к деталям, но и фиксируют их положение в пространстве, выполняя функции сборочно-сварочных приспособлений. При сварке труб и других деталей круглого сечения подвод тока к деталям следует производить с обеих сторон, так как односторонний токоподвод может привести к неравномерному тепловыделению по периметру соединения и к ухудшению качества сварки. Наилучшее качество соединений при сварке деталей круглого сечения достигается при подводе тока с помощью цанговых зажимов (рис. 87), обеспечивающих более равномерное распределение тока по сечению деталей. 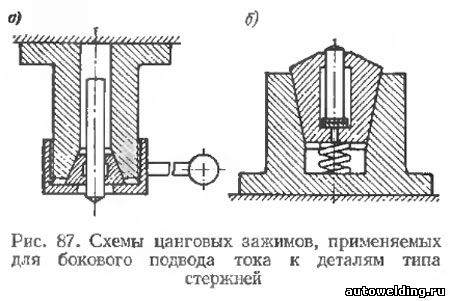
Стойкость электродов при рельефной сварке в большой мере зависит от интенсивности их охлаждения. При применении составных электродов чаще всего ограничиваются устройством водяного охлажления в одних основаниях (рис. 88, а). Электродные вставки охлаждаются при этом только за счет теплопередачи в основание, что не всегда достаточно. Уменьшение нагрева электродных вставок достигается при устройстве в них непосредственного проточного водяного охлаждения, как в электродах для точечной сварки (рис. 88, б). Такая система охлаждения более сложна, но и более эффективна; она может применяться при креплении электродных вставок с помощью конусной и резьбовой посадок. В электродных устройствах с независимым ходом отдельных электродов обычно также устраивают проточное водяное охлаждение каждого электрода в отдельности (см. рис. 85). 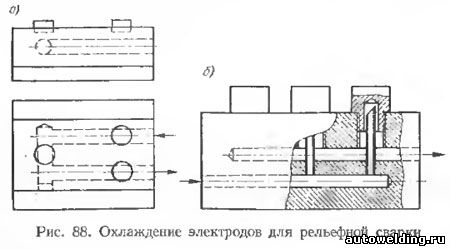
Основания составных электродов и индивидуальные электроды рекомендуется изготавливать из электродных материалов 2-го класса, имеющих твердость не менее НВ 120 и относительную электропроводность не менее 75% от электропроводности чистой отожженной меди. В отечественной промышленности наиболее широкое применение в качестве электродного материала 2-го класса нашла хромовая бронза типа БрХ, изготавливаемая в виде прутков, плит и полос. Плиты и полосы поставляются в термически обработанном, а прутки — в термически не обработанном состоянии. Термомеханическая обработка, улучшающая свойства бронзы, проводится по следующему циклу: закалка с температуры 980—1000° С, охлаждение в воде, холодная деформация 40—50% и отпуск в течение 4—5 ч при температуре 460°. До термообработки твердость бронзы составляет НВ 100—110, а электропроводность 70%. После термообработки твердость может быть повышена до HВ 140—150, а электропроводность до 80—85%. Термообработка хромовой бронзы может производиться также по упрощенному циклу, включающему только операции закалки и отпуска, без промежуточной холодной деформации. Свойства бронзы после такой термообработки будут несколько ниже. Для изготовления электродов и электродных оснований следует применять бронзу только в термообработанном состоянии. Для изготовления вставок составных электродов целесообразно использовать медно-вольфрамовые сплавы, обладающие особо высокой твердостью. Медно-вольфрамовые вставки можно устанавливать также на индивидуальных электродах. Гиллевич В.А. "Технология и оборудование рельефной сварки". -Л. 1978 См. также: Контактная рельефная сварка
|