Требования к сварным конструкциям при точечной и шовной сварке
Одно из основных требований — удобство подхода электродов к зоне сварки (узлы «открытого» или «полуоткрытого» типа). Наиболее удобны для сварки открытые панели (рис. 20.8), наименее — узлы коробчатой формы, обечайки и трубы малого диаметра и т. п. Детали для точечной и шовной сварки обычно изготовляют из листов и профилей. Если к конструкции не предъявляются требования по герметичности, то применяют точечную сварку; шовная сварка обеспечивает получение прочных плотных швов. При изготовлении герметичных отсеков, баков и т. п. выполнение элементов жесткости меньшей толщины при местном разрушении не нарушит плотности обшивки. При затрудненном доступе к зоне сварки используют одностороннюю сварку. 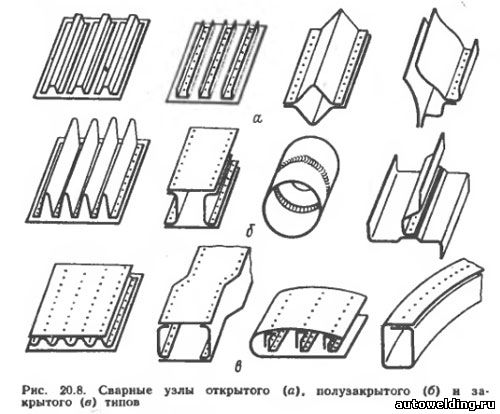
ГОСТ 15878—79 устанавливает основные конструктивные элементы соединений (рис. 20.9) для групп А и Б. Соединения группы А более прочны вследствие больших диаметров ядра. 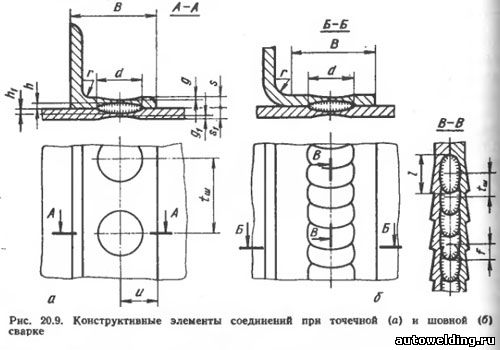
Наиболее важные элементы, определяющие прочность (герметичность) сварных соединений — расчетный (минимальный) диаметр ядра (точечная сварка) и ширина шва (шовная сварка). При достижении требуемых их величин обеспечивается необходимая и стабильная прочность (плотность швов). Фактический диаметр ядра должен быть не меньше указанного в табл. 20.4. 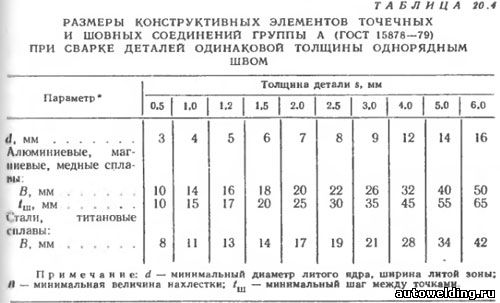
При наладке режима сварщик устанавливает диаметр ядра (dном) на 15—25 % больше минимального, указанного в табл. 20.4, для компенсации колебаний параметров режима, например, уменьшения тока, состояния поверхностей деталей и т. п. Для расчетов d рекомендуется ряд эмпирических формул: d=2s+ (2÷3) мм, d=5s1/2 или 4s23. Повышение технического уровня современных сварочных машин позволяет в ряде случаев уменьшить d на 20—30 %, с одновременным увеличением количества точек, что дает возможность снизить энергоемкость процесса, массу соединений за счет уменьшения ширины нахлестки, повысить циклическую прочность соединений и стойкость электродов и, следовательно, производительность процесса (ГОСТ 15878—79). Международный институт сварки предлагает стандарт, в котором предусмотрено три ряда dmin и dном (табл. 20.5). При этом выделяются две группы — стали и алюминиевые сплавы, для которых dmin и dcр (или dном) меньше, так как для их соединения требуются токи большей силы. 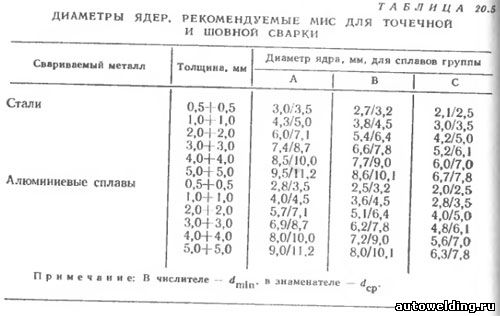
Следует также обратить внимание на то, что для сталей dср больше dmin на 15%, а для алюминиевых сплавов — приблизительно на 25 %, что очевидно свидетельствует о меньшей стабильности процесса сварки сплавов алюминия из-за их высокой активности к кислороду, насыщению влагой и т. п. Величина проплавления (относительная высота ядра) h/s должна находиться в пределах 20—80 % толщины каждой детали. Для титановых сплавов из-за их низкой теплопроводности проплавление может достигать 95 %, а для большинства сплавов оно составляет ~50 %. Глубина вмятины g (g1) должна быть меньше 20 % толщины детали, и лишь при сварке деталей неравных толщин эта величина на тонкой детали может достигать 30 %. Минимальное расстояние (шаг) tш между центрами соседних точек выбирается из условия ограничения шунтирования тока при сохранении высокой прочности шва. Перекрытие литых зон герметичного шва f должно быть не меньше 25 % длины литой зоны l. В среднем же перекрытие устанавливается 50%. Минимальная величина нахлестки В — наименьшая ширина сопрягаемой части соединяемых деталей без учета радиуса скругления соседних элементов (стенки, полки). При r<2s в нахлестку включают не только радиус, но и толщину стенки. Расстояние от центра точки или оси шва до края нахлестки не должно быть меньше 0,5В во избежание раздавливания края. Расстояние между осями соседних рядов (С) на 20 % больше tш. Абсолютные размеры конструктивных элементов увеличивают при росте толщины деталей. При сварке деталей неравных толщин размеры выбирают в соответствии с толщиной более тонкой детали. Некоторые размеры (см. табл. 20.4) зависят от металла деталей. Рельефную сварку чаще всего применяют для соединения стальных деталей. При этом за один импульс тока можно сваривать до 15—20 рельефов. Наибольшее распространение нашла сварка внахлестку деталей из листов с рельефами разных форм, полученными холодной штамповкой. Наиболее часто применяют одиночный рельеф (рис. 20.10,а). Для увеличения площади соединений при ограниченных размерах нахлестки используют рельефы продолговатой формы (б) для получения герметичных соединений — кольцевые рельефы (в). 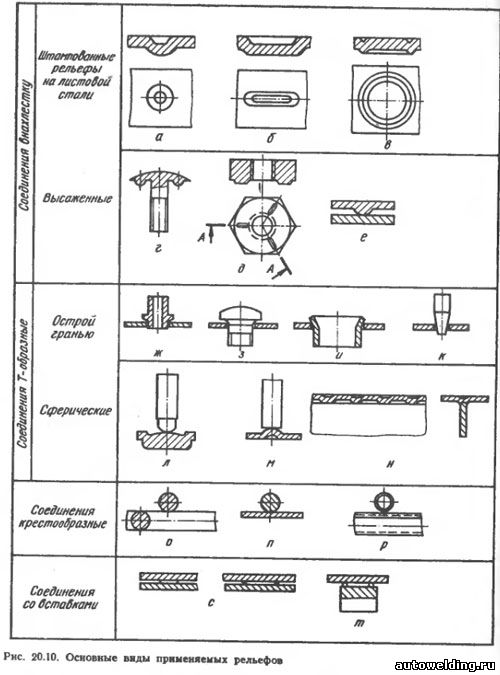
Сплавы с малой жаропрочностью рекомендуют сваривать по сплошным рельефам, например по сплошному выступу в виде полусферы (г). При сварке крепежных изделий рельефы высаживают вхолодную (г, д). Для получения Т-образных соединений часто применяют рельефы с острой гранью (ж, к). Широко используются соединения, когда одна из деталей (стержень) сваривается с развитой поверхностью другой детали— листом (л, м). Рельеф выполняется на конце стержня или листа. Таким же образом можно соединить трубы с листом или два листа, в которых рельефы расположены на торце листа или в плоскости детали (к). Рельефной сваркой могут быть получены и соединения вкрест проволок, стержней и труб (соответственно о, п, р), имеющих естественные рельефы. Такие рельефы могут быть выполнены в виде вставок-концентраторов (с, т), если формирование рельефов высадкой или штамповкой затруднено. За счет вставок можно легировать металл ядра. Когда необходимо соединить детали разной толщины или из разных сплавов, рельефы располагают на более толстой детали или из более прочного сплава. Размеры сферических рельефов, формы пуансонов и матриц приведены на рис. 20.11. Для определения этих размеров (мм) обычно используют следующие формулы: 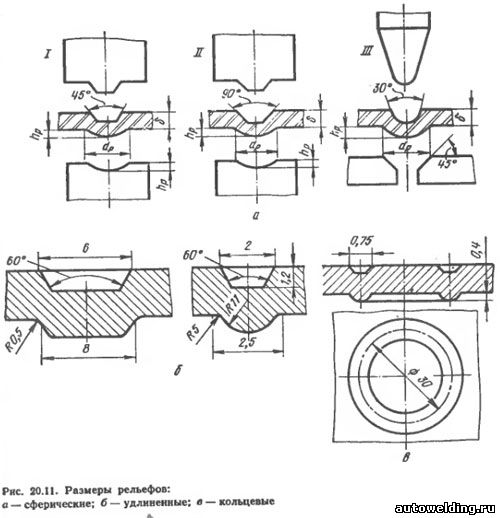
dp = 2s + 0,75, hp = 0,4s+0,25, или dp = (0,5÷0,7) s, hp = (0,2÷0,25) dp. При этом диаметр ядра обычно на 20—50 % больше dp. Допуски на высоту и диаметр рельефа составляют соответственно ±0,05 и 0,1 мм при толщине детали ≤1,25 мм и ±0,12 при толщине >1,25 мм. Размеры соединений приведены в табл. 20.6. 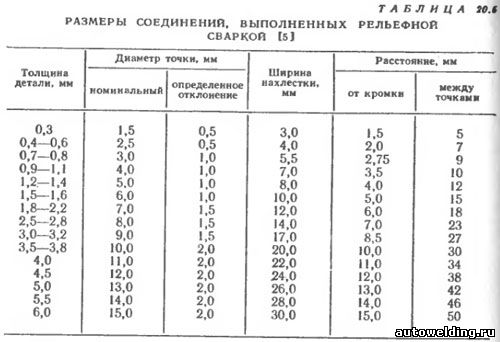
МИС рекомендует для сварки малоуглеродистой стали рельефы, размеры которых приведены на рис. 20.12. 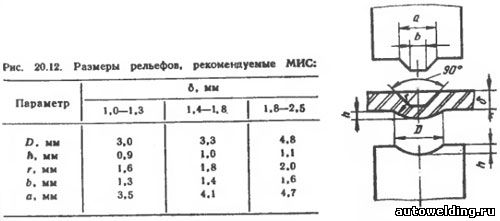
Волченко В.Н. Сварка и свариваемые материалы т.2. -M.1996 См. также: Контактная сварка, точечная сварка, шовная сварка
|