Контроль качества рельефной сварки
Вопросы контроля качества соединений при рельефной сварке разработаны в очень малой степени. Поэтому в производственной практике целесообразно использовать опыт контроля точечной и роликовой сварки. При этом одни рекомендации по контролю точечной и роликовой сварки могут быть применены без существенных поправок, в то время как другие нуждаются в уточнениях и изменениях. Ниже описываются некоторые особенности контроля качества соединений, характерные для рельефной сварки. Основная задача контроля качества состоит в определении размеров и прочности сварных соединений и выявлении дефектов сварки. При рельефной сварке могут возникать те же дефекты, что и при точечной. Качество соединений зависит не только от процесса сварки, но и от ряда смежных операций, таких как подготовка поверхности деталей, сборка деталей, подготовка электродов и приспособлений и т. д. Все эти операции подлежат контролю. При рельефной сварке необходимо, кроме того, контролировать размеры и расположение рельефов, а также состояние кромок деталей и свариваемых поверхностей. Не допускаются заусенцы, неровности, забоины и другие дефекты, приводящие к касаниям деталей вне зоны соединения. Наличие поверхностных дефектов особенно опасно при больших размерах деталей, при наличии криволинейных поверхностей и при сварке в нескольких плоскостях. Контроль качества сварки может производиться разрушающими и неразрушающими методами. Разрушающими методами испытывают контрольные технологические образцы, изготовленные из того же материала и свариваемые на тех же режимах, что и контролируемые детали. Таким образом, испытание контрольных образцов (образцов-свидетелей) является косвенным методом контроля, позволяющим судить о качестве свариваемых деталей лишь при условии полной идентичности условий сварки деталей и контрольных образцов. Качество сварки на контрольных образцах определяют их разрушением в тисках (технологическая проба), изучением макро- и микроструктуры соединений на шлифах и по результатам механических испытаний. В зависимости от свойств соединения и способа приложения нагрузки разрушение образцов технологической пробы может происходить со срезом в плоскости соединения или с вырывом сварной точки. Оценка размеров и качества соединений при их разрушении с вырывом затруднена. В отличие от точечной и шовной сварки сквозной вырыв соединений при рельефной сварке возможен и при отсутствии расплавления и не является, таким образом, признаком наличия литой зоны. Если разрушение образцов происходит со срезом в плоскости соединения, то на изломе можно замерить диаметр литого ядра и пластического пояска, а также обнаружить внутренние поры и трещины (рис. 41, а). В этом случае оценка качества соединения по результатам технологической пробы является более достоверной. 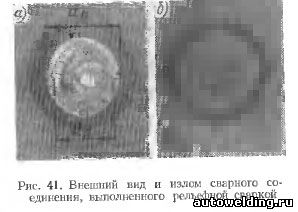
Наиболее полное представление о наличии и размерах литой зоны может быть получено в результате исследования макроструктуры соединений на поперечных шлифах. Шлифы изготавливают, разрезая контрольные образцы перпендикулярно поверхности по центру сварного соединения. Техника изготовления, травления и исследования шлифов при рельефной сварке такая же, как при точечной и шовной. Однако следует помнить, что в связи с высокой несущей способностью соединений, выполненных рельефной сваркой в твердой фазе, их прочность в меньшей степени определяется размерами литой зоны, чем прочность точечно-сварных соединений. В некоторых случаях (например, при рельефной сварке оцинкованной стали) наличие литой зоны вообще не влияет на работоспособность сварного соединения и не является обязательным. Поэтому исследование макроструктуры соединений так же, как и технологическая проба, не всегда позволяет правильно оценить качество рельефной сварки. Наиболее достоверным показателем качества соединений, выполненных рельефной сваркой, является их прочность, определяемая при механических испытаниях контрольных образцов на срез и отрыв. Размеры образцов для механических испытаний при рельефной сварке такие же, как и при точечной. Важным показателем механических свойств соединений является пластичность, характеризуемая отношением прочности образцов на отрыв к прочности на срез. Так же, как и при технологической пробе, разрушение образцов при испытаниях на срез и отрыв может происходить как со срезом, так и с вырывом сварного соединения, причем характер разрушения не является показателем качества сварки. Сварку и испытание контрольных образцов производят при отработке нового режима, а также после длительных перерывов в работе машины, в начале и конце сварки партии изделий, а в особо ответственных производствах после сварки определенного количества соединений. Периодичность сварки и число контрольных образцов устанавливают в зависимости от группы ответственности соединений с учетом рекомендаций отраслевых и производственных нормалей. Контроль качества соединений непосредственно на сварном узле производят с применением неразрушающих методов. Простейшим из них является внешний осмотр. При внешнем осмотре соединений, полученных в результате сварки по выштампованным рельефам, в первую очередь следует обращать внимание на степень заполнения полости лунки металлом. Полное заполнение лунки, вызванное интенсивным нагревом металла деталей, указывает обычно на образование в соединении литой зоны (рис. 41, б). Однако в некоторых случаях, таких как сварка на весьма мягких режимах, сварка оцинкованных сталей и в ряде других, лунка может быть заполнена металлом и при отсутствии литой зоны. Таким образом, заполнение лунки не может служить достоверным признаком хорошей сварки. В то же время наличие незаполненной лунки чаще всего свидетельствует об отсутствии расплавления и невысокой прочности соединений. Изменение степени заполнения лунки при сварке деталей с неизменной настройкой машины также указывает на нарушение условий сварки и на вероятное ухудшение качества сварных точек. Наличие вмятин с характерным потемнением металла на поверхности деталей является признаком сильных конечных выплесков, сопровождающихся образованием усадочных пор и трещин. К числу неразрушающих методов контроля качества сварных соединений относится просвечивание рентгеновскими лучами с использованием рентгеноконтрастных материалов (РМК). Метод контроля с введением в зону сварки РМК разработан недавно и применяется при точечной и роликовой сварке различных сталей и сплавов. Можно предполагать, что этот метод может быть применен также и при рельефной сварке. В настоящее время данных о его использовании при рельефной сварке нет. Последние годы все большее внимание уделяется развитию неразрушающих методов контроля, основанных на измерении в процессе сварки различных параметров режима, прямо или косвенно связанных с процессом формирования сварного соединения. Контроль может производиться по электрическим и физическим параметрам, таким как напряжение и мощность на электродах, сопротивление свариваемых деталей, перемещение электродов, вызванное тепловым расширением деталей, изменение амплитуды ультразвуковых колебаний, пропускаемых через зону сварки и др. Рядом исследователей рассмотрены особенности применения контроля по параметрам режима при рельефной сварке. Так, Ю.Н. Ланкиным была проведена работа по выявлению электрического параметра, наиболее полно отражающего качество сварных соединений при рельефной сварке сепараторов шарикоподшипников. Рассматривались следующие параметры: средний за время сварки ток, время сварки, произведение сварочного тока на время сварки, среднее за время сварки напряжение на свариваемых деталях, произведение напряжения на деталях на время сварки, напряжение на деталях в конце сварки, снижение напряжения на деталях от максимального значения в начале процесса до минимального в конце сварки, сопротивление свариваемого изделия в конце сварки, энергия, затрачиваемая на сварку, и средняя за время сварки мощность, выделяемая в сварном соединении. Оценка тесноты связи между перечисленными параметрами и качеством соединений производилась по величине корреляционного отношения η или коэффициента корреляции r между прочностью соединений и соответствующим параметром. Было установлено, что оптимальным (из числа рассмотренных) косвенным показателем, имеющим наибольшее значение корреляционного отношения с прочностью, является среднее за время сварки падение напряжения на свариваемых деталях (η = 0,8). Из этого можно сделать вывод о принципиальной возможности использовать этот показатель как параметр контроля качества соединений при рельефной сварке. Однако практические пути для реализации при рельефной сварке этого метода контроля пока не намечены. Наиболее отработанным методом контроля качества соединений в процессе сварки является в настоящее время контроль по перемещению подвижного электрода машины (дилатометрический контроль). В результате нагрева и расплавления металл в зоне сварки расширяется и раздвигает сварочные электроды. Учитывая вдавливание электродов в поверхность деталей, их расхождение при точечной и шовной сварке несколько меньше, чем тепловое расширение металла, однако при применении рациональных режимов это различие невелико. В связи с трудностями замера перемещения верхнего электрода относительно нижнего контроль теплового расширения металла при сварке в производственных условиях производят измерением перемещения верхнего электрода относительно верхней консоли сварочной машины. При этом возникает погрешность, вызванная возможным изменением Fсв, а следовательно, и прогиба нижней консоли. Эта погрешность тем больше, чем меньше жесткость машины и чем больше силы трения в приводе давления. Контроль качества сварки по перемещению подвижного электрода возможен лишь в том случае, если сварка выполняется на машинах, удовлетворяющих условию Fтр/δM≤0,05, где Fтр — сила трения в приводе сжатия, даН; М — жесткость силового контура машины, даН/мм. Следует отметить, что повышенная жесткость корпуса и консолей и малое трение в приводе давления машины являются теми особенностями, которые в первую очередь должны быть присущи оборудованию для рельефной сварки. Поэтому современные рельефные машины, как правило, удовлетворяют указанному выше условию и вполне пригодны для дилатометрического контроля. Проведение этого контроля затруднено при сварке на старых машинах типа МРП и МТП в связи с повышенным трением в приводе давления этих машин. При рельефной сварке перемещение электрода hэл складывается из двух противоположно направленных составляющих: перемещения, равного изменению высоты рельефа при его смятии hр и перемещения Δ, вызванного тепловым расширением деталей во время их нагрева. При этом основную долю перемещения электродов составляет их сближение, вызванное смятием рельефа (см. рис. 15). Раздвигание электродов, как результат теплового расширения деталей, составляет незначительную часть их общего перемещения. Это затрудняет получение достоверных результатов при контроле качества рельефной сварки по раздвиганию электродов. 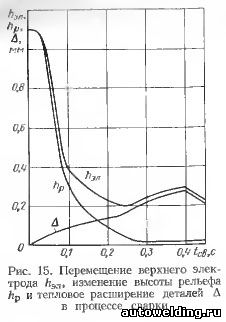
Значительно надежней использовать в качестве параметра контроля величину сближения электродов, происходящего после сварки (Авт. свид. № 241563). Вслед за выключением сварочного тока металл зоны соединения охлаждается, что приводит к его усадке и сближению электродов на величину предшествующего теплового расширения. При этом в отличие от перемещения электродов при нагреве, вызванного не столько тепловым расширением металла, сколько процессом смятия рельефа, сближение электродов при охлаждении зоны сварки определяется только усадкой металла соединения. Поэтому величина сближения электродов после выключения тока и качество сварного соединения находятся между собой в весьма тесной корреляционной зависимости. Следует отметить, что контроль качества соединений по сближению электродов целесообразно осуществлять не только при рельефной, но также и при точечной сварке в тех случаях, когда перемещение электродов при нагреве обусловливается помимо теплового расширения металла другими проходящими при сварке процессами. Так, например, при точечной сварке на режимах, приводящих к значительному нагреву наружных поверхностей деталей (сварка с шунтированием тока, сварка на мягких режимах, сварка с применением электродов с относительно малым диаметром рабочей поверхности и т. д.), наблюдается значительное вдавливание электродов в деталь, приводящее, несмотря на продолжение роста литого ядра, к прекращению раздвигания электродов или даже к их сближению. Это существенно ухудшает надежность контроля качества сварного соединения по раздвиганию электродов. Осуществление контроля по сближению электродов после выключения тока позволяет исключить искажающее влияние процесса вдавливания электродов в деталь и дает, тем самым, более точную оценку величины теплового расширения деталей. Исследования показали, что между величиной сближения электродов после выключения сварочного тока Δ и прочностью Рср соединений при рельефной сварке имеется довольно тесная линейная связь, характеризуемая сравнительно небольшой колеблемостью результатов отдельных измерений относительно их средних значений (рис. 42). 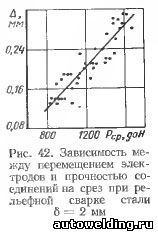
Коэффициент корреляции, характеризующий тесноту зависимости между Δ и Рср, Расчет показывает, что при такой тесноте связи между Δ и Рср диапазон колебаний прочности сварных соединений при данной величине сближения электродов составляет с вероятностью 0,9 примерно ±10% от среднего значения Рср. Для контроля качества сварки по перемещению электродов разработано несколько типов контрольно-регистрирующей аппаратуры: АДК-1, ПДК-2М, ПДК-3, АКС-1, АКС-2. Контроль по сближению электродов можно осуществлять с помощью прибора АКС-2, конструкции ВНИИЭСО. В приборе применен бесконтактный фотоэлектрический датчик, позволяющий измерять перемещение электрода в обоих направлениях с точностью ±0,01 мм. Датчик содержит две растровые решетки, одна из которых (неподвижная) вместе с корпусом датчика закреплена на консоли машины, а вторая (подвижная) с помощью магнитной системы зацепления связана с ползуном. При движении одной решетки относительно другой происходит периодический разрыв луча света, освещающего фотодиоды. Измерение перемещений сводится к счету импульсов, возникающих при освещении и затемнении фотодиодов. Прибор имеет цифровую индикацию измеряемого перемещения и позволяет запоминать наибольшее перемещение до начала следующего импульса тока. Оперативная индикация состояния — «качественная сварка», «непровар» и «перегрев» — осуществляется с помощью цветных сигнальных ламп. Индикация состояния зависит от соотношения между достигнутым перемещением и уровнями установленного задания. На приборе устанавливают два уровня. Если перемещение находится в диапазоне между первым и вторым, это эквивалентно качественной сварке. Перемещение ниже первого уровня соответствует непровару, выше второго уровня — перегреву. Уровни перемещений выбираются из анализа экспериментальных зависимостей между Δ и Рср (dя (рис. 42) с учетом вероятного разброса данных. Прибор АКС-2 может быть использован для дилатометрического контроля качества сварных соединений при рельефной сварке одиночными рельефами. Применение этого метода контроля для групповой рельефной сварки возможно при использовании приспособлений с независимым ходом отдельных электродов, при условии замера перемещения каждого электрода в отдельности. Для этой цели потребуется разработка специальных датчиков перемещения, конструкция которых должна соответствовать конструкции электродных приспособлений. Практического опыта применения контроля качества соединений по перемещению электродов при групповой рельефной сварке в настоящее время нет. Гиллевич В.А. Технология и оборудование рельефной сварки. -Л. 1986 См. также: Контактная сварка, Контактная рельефная сварка
|